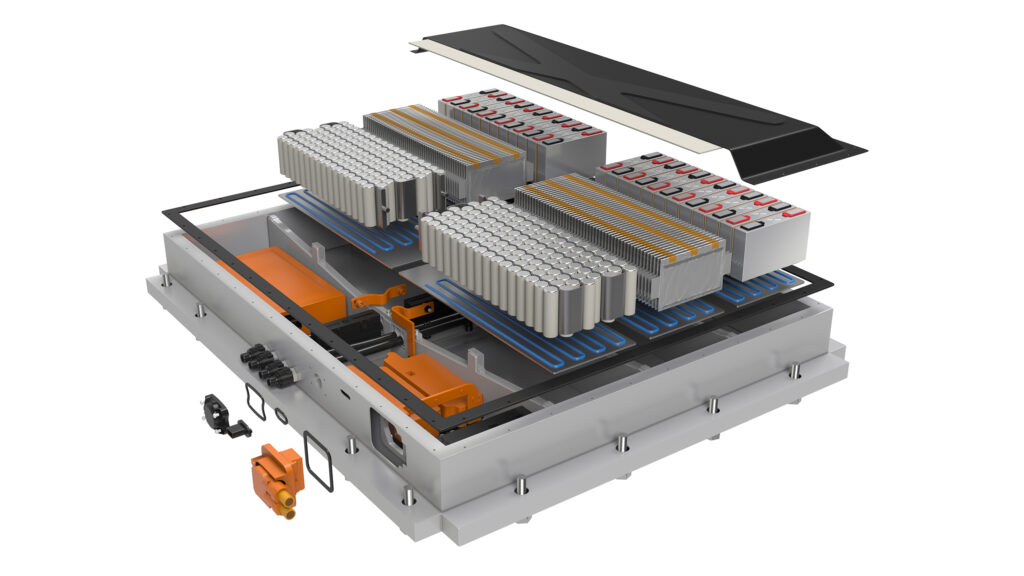
Advances in structural adhesives are supporting the development of bigger, more efficient and safer battery packs.
With the advent of bigger battery packs in electric vehicles to improve performance and range comes the challenge of managing the heat build-up in lithium-ion batteries, in order to reduce the risk of thermal runaway.
Higher temperatures also affect battery adhesives and conductive materials, while the shift to 800-volt systems requires a new generation of non-silicone insulators and connectors. Automotive Industries (AI) spoke to Andreas Lutz – Director Global Technology Adhesive & Sealants and Jacek Reutt – Business Development Leader for E&I at DuPont.
AI: What new technologies and solutions did you present at the Battery Show Europe 2024?
Lutz: There is a trend for battery technology to go cell to plate. For that, DuPont needed to develop and commercialize a product which combines structural adhesive properties with thermal conductivity.
The adhesive will play an important role in the structural integrity of the battery designs. There is also a need for adhesives that bond to new substrates, such as bare aluminum instead of coated aluminum.
Additional properties required of the adhesive is the ease of manufacturing. There must be a certain open time to allow for assembly.
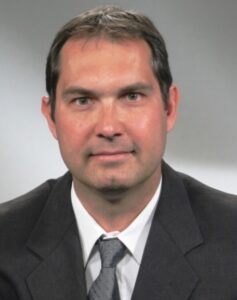
Reutt: We are the sister department to adhesives, we design and supply printed circuit boards, and general interface materials, electromagnetic and heat shielding,
There is currently a focus on busbars, which need to be adequately insulated to protect the battery against thermal runaway.
We have developed an electrical isolating and heat dissipating material that can be wrapped round the busbar in layers in order to support fast charging.
AI: With the new designs and trends in EV battery packs where do you see the biggest challenges and opportunities for DuPont?
Lutz: Combining good durability with higher strength and thermal conductivity, together with broad substrate adhesion to the various kinds of substrates.
These include bare aluminum and PET. For that you need a broad range of different chemistries.
Reutt: Another trend we see is towards composite battery housing materials, in order to reduce weight.
DuPont has materials for the bonding of composites.
AI: Can DuPont materials enable design of EV batteries to be safer, more durable, and go the distance?
Lutz: It is an excellent opportunity for DuPont because we are not only a chemical formulator.
We develop polymers, curing accelerators, and adhesion promoters, which we then use in our formulations. Our customers appreciate that innovation partnership where we can develop any kind of chemistry.
AI: Do DuPont innovations extend to manufacturing as well?
Lutz: We are very proud that we built capabilities in all the regions, serving our customers in Asia Pacific, in North America and Europe.
Reutt: For us it is very important to have local to local manufacturing.
The Laird™ MFS (multi-functional solutions) product family solves multiple EMI, thermal and structural design issues simultaneously using a single process design, which ensures we can provide our customers with the right application and full solution.
Solutions in the MFS portfolio include Metal-ISE: thermally and electro-magnetically enhanced diecast, stamped, deep-drawn precision metal parts at board level (e.g. board level shields and RF absorbers) or
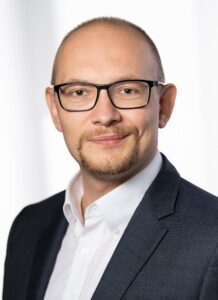
subassembly level (e.g. automotive heatsinks); Structur-ISE: Highly durable mechanically stable solutions at enclosure and I/O interface level (e.g. radomes, using state-of-the-art injection molding or forming capabilities); Hybrid-ISE: Homogeneous single layer or heterogeneous multi-layer polymeric solutions offering multi-functional signal interference mitigation and heat dissipation (e.g. a thermally conductive RF absorber); and Textil-ISE: Electrically conductive fabrics enabling sensor, switch, and heating functionality (e.g. selectively plated stretch fabric).
AI: How can your EV battery assembly adhesives maximize performance and durability?
Lutz: It relies on chemistry. We use special polymers which offer resistance under static, fatigue and dynamic loading to ensure the structural integrity of the battery while in service for at least the 10-year warranty period most of the OEMs are offering their customers.
Battery design is simplified by our products which can bond with bare metal, PET or other substrates, qualities which would not have been required in the past.
AI: Do DuPont adhesives allow manufacturers to use fewer components and, in the process, increase production efficiencies and optimize cost for current and new battery pack design?
Lutz: In a positive sense, because we are the enabler for our customer so that they can realize their new battery design.
There is simplification, but also greater efficiency with higher energy density for more mileage.
AI: Battery repair is of growing interest to the industry. Do you formulate adhesives, sealers, and thermal interface materials with disassembly in mind?
Lutz: This is a hot topic in the research field right now rather than in the development phase. There are various debonding solutions, starting with relatively broad applications that can be integrated into a formulation, or applied as a separate layer.
We are investigating the different concepts and triggers such as temperature and the amount of current to allow for disassembly and recycling.
AI: Are your Global Centers of Excellence for Automotive Electrification addressing specific industry challenges in the field of E-powertrain Efficiency?
Lutz: The DuPont Geneva Innovation Center connects customers with our global network of scientists, chemists, and engineers, focusing on automotive, cosmetics, food packaging, and more.
There is a big focus on 800-volt systems, where traditional insulation layers are no longer effective, which could lead to a short circuit. To meet the need we have developed a custom layer which, in addition to providing the necessary isolation, is thinner than the traditional layer.
This allows our customers to increase the copper content and have a more efficient battery.
Reutt: A ceiling seems to have been reached with resin technology, which is not suited to the higher voltages.
Our engineers believe that silicone technology will provide the solutions. With the acquisition of Laird, we are now in the position to offer applications with thermal conductivity of up to nine Watts per meter Kelvin, with the potential of achieving 44 Watts per meter Kelvin.
More Stories
DuPont materials science advances next generation of EV batteries at The Battery Show
How a Truck Driver Can Avoid Mistakes That Lead to Truck Accidents
Car Crash Types Explained: From Rear-End to Head-On Collisions