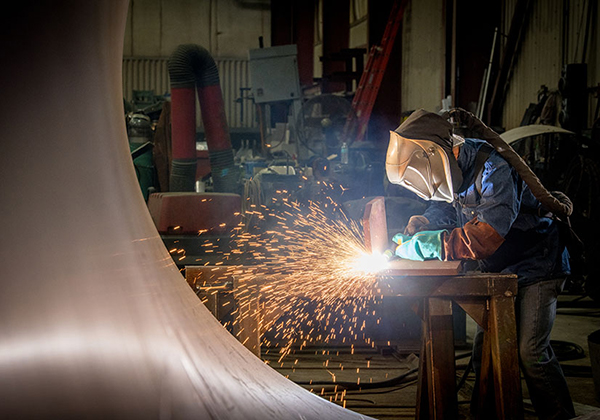
The automotive industry is constantly evolving, and so are the methods used to produce cars. In a market where consumers expect both high quality and rapid production, manufacturers are turning to modern equipment to stay ahead.
From automated assembly lines to precision cutting tools, these new technologies are transforming how cars are built. What once required extensive manual labor and time-consuming processes can now be accomplished more quickly and with greater accuracy.
For companies aiming to meet growing consumer expectations, investing in advanced equipment is necessary. This article explains how modern tools and technologies are setting new benchmarks for efficiency and precision.
So, let’s get started!
1. Efficiency Is No Longer Optional – It’s a Competitive Necessity
Traditional methods cannot keep up with the pace of demand in automotive manufacturing. Time is money, and manufacturers must produce more vehicles faster than ever before. Modern equipment, especially automation, is the answer.
If your production lines are inefficient, you’ll face longer delivery times, higher costs, and lost opportunities. Efficiency today directly translates to competitiveness in the market.
Why You Can’t Ignore Efficiency
- Higher Output: Automated systems perform tasks at a much faster rate than manual labor.
- Cost Reduction: By reducing labor costs and minimizing errors, automation significantly lowers production costs.
- Quicker Time-to-Market: With faster production cycles, manufacturers can bring new models to market more quickly.
Failing to invest in automation means falling behind competitors who are already reaping these benefits.
2. Precision Matters: Customers Demand Perfection
The automotive market is more demanding than ever, and consumers expect precision and quality. Traditional cutting methods leave room for error, but advanced technology is changing that. With new designs requiring higher levels of accuracy, the need for cutting-edge tools has become more urgent. Even a small mistake can lead to costly production delays and material waste.
A portable plasma cutter provides a solution by delivering consistent, precise cuts across a range of materials. These tools allow manufacturers to work with high levels of accuracy, ensuring that even the most intricate parts meet exact specifications. They also offer the added benefit of speeding up production without sacrificing quality.
Modern plasma cutters stand out because they offer several benefits.
- Consistent Performance: The ability to handle various types of metal with ease, ensuring every cut is smooth and exact.
- Faster Operation: These tools are known for reducing cutting time while maintaining accuracy, which helps manufacturers meet tight deadlines.
- Ease of Use: With advancements in portable plasma cutters, operators can now carry out precision tasks even in hard-to-reach areas, ensuring flexibility on the production line.
Investing in high-quality cutting tools minimizes material waste and significantly enhances production efficiency.
3. Innovation Is the Future: Stay Relevant with 3D Printing
The automotive industry is changing rapidly, and manufacturers need to innovate to stay relevant. 3D printing allows for greater creativity in design and faster prototyping, opening up new possibilities in production.
Consumers now expect unique and innovative designs, and you can’t meet those demands using traditional manufacturing alone. 3D printing offers the flexibility to experiment and adapt to changing trends.
Why You Should Be Adopting 3D Printing
- Design Flexibility: Create complex, custom parts with ease—something traditional methods can’t match.
- Speed: Prototypes can be developed in hours, allowing for quicker design iterations.
- Adaptability: As consumer demands shift toward personalized products, 3D printing allows you to adapt quickly.
If you aren’t integrating 3D printing, you are limiting your ability to innovate and deliver the custom designs consumers now expect.
4. Data-Driven Production: The Industry Standard You Can’t Afford to Miss
Data analytics is becoming the backbone of modern manufacturing. Those who do not adopt data-driven production are missing out on crucial insights that can save time and money.
Data is the key to identifying inefficiencies in your production line. Without it, you’re operating in the dark while others optimize every step of their process.
The Power of Data
- Real-Time Decision Making: Data allows you to make quick adjustments to optimize production, preventing costly mistakes.
- Predictive Maintenance: Data analytics predict when equipment will need maintenance, reducing downtime.
- Better Quality Control: Use data to spot trends and ensure that defects are caught early, ensuring higher-quality vehicles.
If you don’t use data to guide your production, you’re working blind while your competitors use it to improve efficiency and product quality.
Wrapping It Up
The automotive industry is at a crossroads. Manufacturers must decide whether to adapt to the new production standards or risk falling behind. Automation, cutting-edge tools like the portable plasma cutter, 3D printing, data-driven manufacturing, and sustainability practices are no longer just improvements—they are essential to staying competitive. Using modern equipment isn’t just about improving production. In fact, it’s about future-proofing your business in a rapidly evolving industry. Don’t get left behind. The time to adapt is now.
More Stories
Automotive Industries (AI) Newsletter April 2025
Bangkok International Motor Show 2025 – The Talk of Sensuous Automotive
Earn GHG reduction values through MOL Pure Car Carrier “Book and Claim (B&C)” service