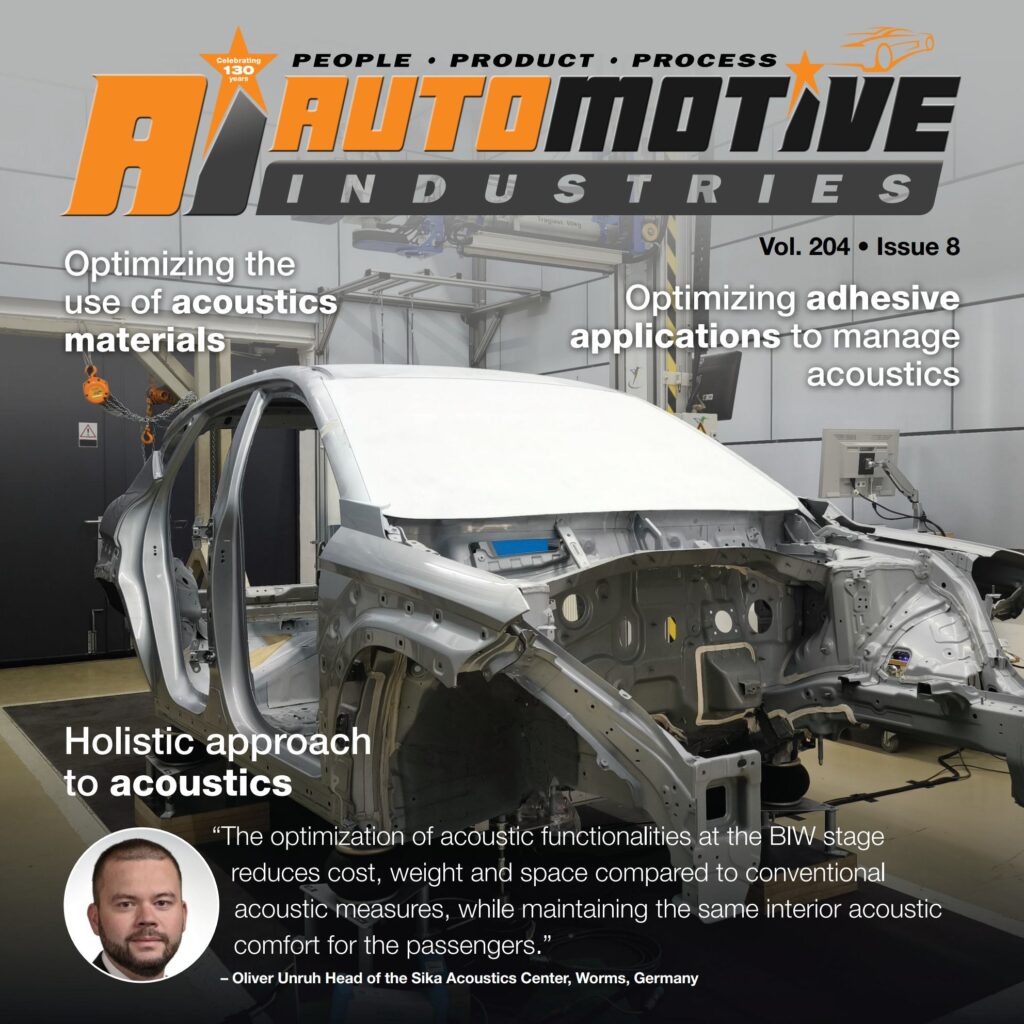
Sika - Optimization of acoustic functionalities at the BIW stage.
Sika Automotive is combining a range of technologies to control and influence in-vehicle noise transfer paths through a holistic approach to acoustics.
Technologies utilized in the system include SikaBaffle®, SikaSeal® and SikaDamp® for noise control; SikaPower® for high strength bonding; Sikaflex® for roof or windshield glass installation; SikaReinforcer® structural inserts for car body structural reinforcements; and SikaBiresin® for dielectrics and potting in electrical componentry.
According to Sika, the technologies contribute significantly to in-vehicle acoustic performance when used as a system rather than deployed individually.
Automotive Industries (AI) asked Oliver Unruh Head of the Sika Acoustics Center, Worms, Germany, what the advantages are of a holistic approach to acoustics.
Unruh: In the process of optimization of acoustic properties of the body-in-white (BIW), relevant noise transfer paths need to be identified and addressed with a combination of established measures such as SikaDamp® damping patches and SikaBaffle® acoustic foams.

Other Sika materials located inside the noise transfer paths are used for sealing, bonding and reinforcement.
The idea behind the holistic approach is to optimize these materials as well for better acoustics.
The optimization of acoustic functionalities at the BIW stage reduces cost, weight and space compared to conventional acoustic measures, while maintaining the same interior acoustic comfort for the passengers.
AI: How do the different technologies complement each other?
Unruh: The technologies complement each other in terms of the specific application scenario and the acoustic frequency ranges they are addressing.
SikaReinforcer® components address driving comfort in the lower frequency range (< 100 Hz).
SikaBaffle® and SikaSeal® foams muffle noise transfer paths in cavities and pillars with respect to airborne noise insulation, absorption as well as vibration damping for mid to higher frequencies.
SikaDamp® technology targets almost the entire audible frequency range of noise radiation from panels and surfaces in the car body.
Specific noise transfer paths, such as noise radiation from wind screens and sunroofs, can be addressed by acoustically optimized direct glazing adhesives which are in development right now.
AI: How do you address specific challenges in the new mobility applications such as e-vehicles?
Unruh: All acoustic functionality improvements that we implement for products relevant for Sika’s holistic approach are conducted with a specific focus on the relevant e-mobility frequency range and specific noise sources and excitation phenomena.
For example, high performance SikaDamp® constrained layer technology is used for the damping of inverter cover vibrations in electric drive units improving annoying tonal noise in e-vehicles.
Our newest product, SikaSeal® pumpable baffle technology is a proven solution to issues in high frequency noise transmission through cavities and pillars, and can be used where traditional baffles do not fit in smaller and narrow cavities
Sika is also exploring opportunities and market needs for acoustic functionalities in entirely new products families such as dielectric potting or battery related materials.
Overall targets are to eliminate vibration, which translates to improved acoustics.
AI: Where do you see the main applications of the holistic approach?
Unruh: While we are primarily focused on automotive applications for car-body acoustics optimization, Sika has a strong business in other important areas such as transportation, marine, construction and modular building.

The introduction of improved acoustic functionalities works as well for products such as marine floor adhesives or water-based adhesives in construction elements.
AI: What do you see as the main acoustics challenges going forward?
Unruh: One big challenge is that occasionally it is not easy to integrate acoustic functionalities in products with other important but contradictory requirements.
To give you an example, SikaPower® structural adhesives are designed to guarantee high level of strength / stiffness, but to improve vibration damping performance, you need to compromise on bonding performance. That starts at the BIW.
AI: How is Sika addressing this challenge?
Unruh: Sika’s capabilities in R&D and in acoustic development enable an efficient screening and preselection of
promising technologies for further acoustic optimization on various relevant levels.
A very basic evaluation of promising candidates is performed at material level, where changes in material properties can be easily implemented and analyzed.
In the next development stage, component level testing addresses the performance of new materials in the proper application scenario.
Finally, best candidates are evaluated on higher levels including the production state BIW or full vehicle on the road.
AI: At what point should Sika be involved in the development of a new platform?
Unruh: For our OEM customers it is getting more and more important to properly address vehicle acoustics in early design stages using simulation models.
Our mission as an acoustic supplier is to provide valid material data and state-of-the-art simulation methods for proper introduction of relevant acoustic materials in virtual models.
When consulted early in the design stage, even during simulation, our customers can benefit from a broader range of acoustics solution possibilities.
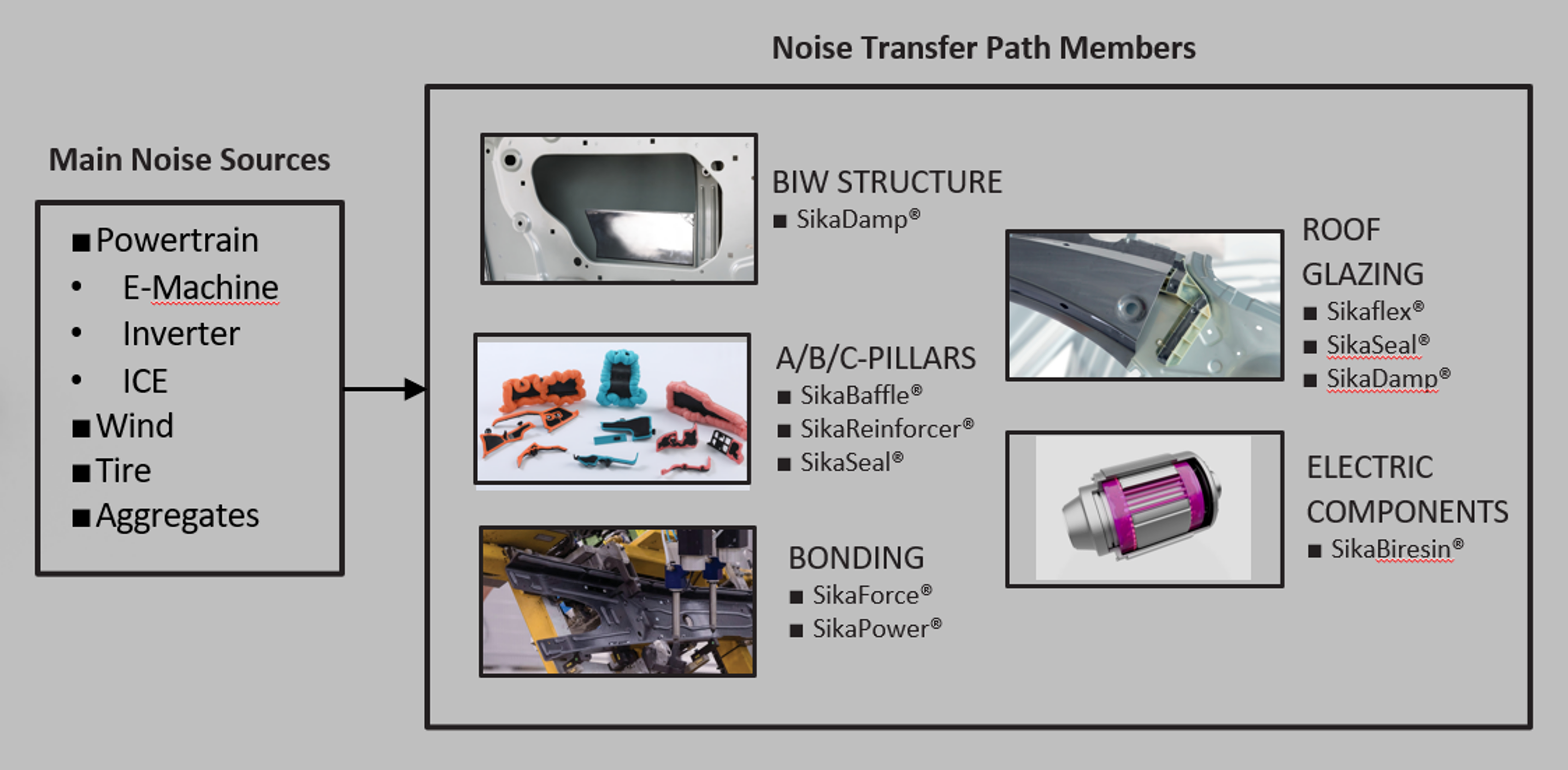
More Stories
DuPont materials science advances next generation of EV batteries at The Battery Show
How a Truck Driver Can Avoid Mistakes That Lead to Truck Accidents
Car Crash Types Explained: From Rear-End to Head-On Collisions