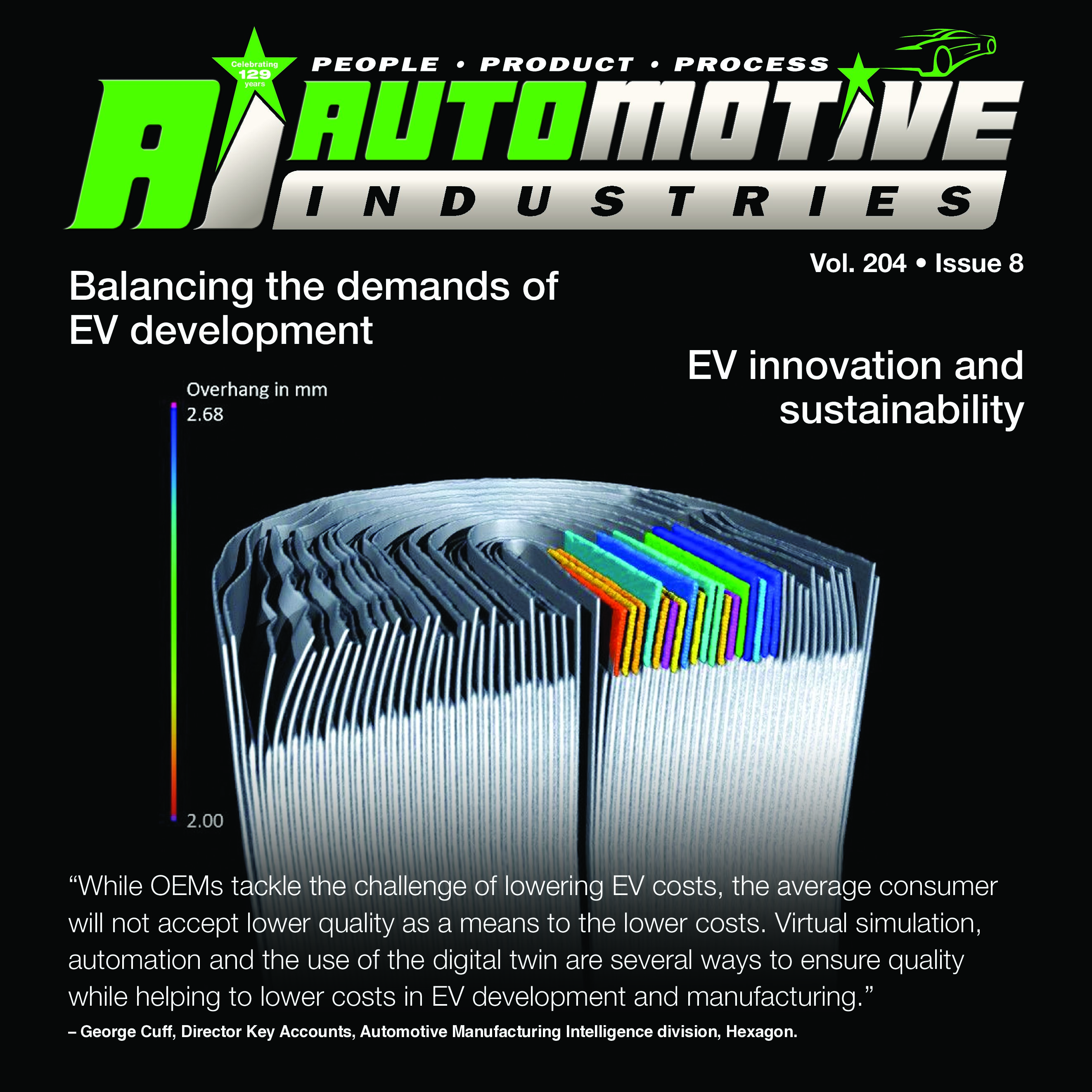
The electric vehicle (EV) industry is at the forefront of technological innovation and sustainability.
As manufacturers aim to meet the rising demand for cleaner, more efficient transportation options, the journey from concept to production presents unique challenges and opportunities.
Rapid changes to battery chemistry and advancements in vehicle-applied technologies create a chaotic environment, all in the presence of cost pressures in the market.
This turbulence is full of opportunities but will require focusing on how companies balance competing demands, assess technological and manufacturing readiness, and utilize tools to enhance collaboration and management. In other words, learning.
Balance Competing Demands and Constraints
The development of EVs is a complex interplay between engineering excellence, environmental considerations, and market viability.
Manufacturers must balance these often-competing demands to deliver products that are not only technologically advanced but also economically feasible and environmentally friendly.
For instance, the drive for longer battery life must be weighed against cost constraints and the availability of raw materials.
Similarly, consumer demand for more features and performance must be balanced with regulatory requirements for safety and emissions.
Readiness
Assessing the Technology Readiness Level (TRL 1-9) is crucial in the EV industry.
This scale helps manufacturers evaluate a technology’s maturity before it is incorporated into a new product.
Key technologies such as battery storage systems, electric motors, and advanced driver-assistance systems (ADAS) must be rigorously tested and refined for EVs.
A high TRL indicates that a technology is ready for integration and mass production, reducing risks and potential delays in the development process.
Parallel to technological assessments, the Manufacturing Readiness Level (MRL 1-10) gauges how prepared a production process is to implement a new product or technology.
For EVs, this includes evaluating the capability of assembly lines to handle novel components like lithium-ion battery packs or custom electric drivetrains.
A high MRL ensures that once the product design is finalized, the transition to mass production can occur smoothly, with minimal disruption and cost overruns.
By providing detailed insights and data analytics, Hexagon tools facilitate the transition from prototype to production, ensuring that technology application and manufacturing processes are optimized and meet stringent quality standards.
This alignment with MRL helps manufacturers streamline their production capabilities, reducing cost and enhancing overall product reliability.
Using Hexagon’s comprehensive suite of solutions, organizations can better manage technology integration and production readiness complexities, ensuring a cost-effective solution.
Shared Learning and Distributed Teams
The global nature of the EV market necessitates collaboration across geographically distributed teams. Shared learning platforms enable engineers, designers, and production staff to exchange knowledge and innovations in real-time.
This collaborative approach helps refine designs and production techniques, ensuring all team members are aligned with the project goals and progress, regardless of their physical location.
Cloud-based collaboration, project management software and virtual reality (VR) simulations are critical in bridging the gap between distributed teams.
Hexagon’s advanced tools can significantly enhance product development when integrated with VR and AR technologies, especially for distributed teams.
By leveraging Hexagon’s precision measurement and quality assurance solutions alongside immersive VR and AR environments, teams can collaboratively design, simulate, and validate products in real-time, regardless of their geographical locations.
This integration fosters seamless communication, reduces errors, and accelerates decision-making processes, ultimately leading to more innovative and high-quality product outcomes.
Tools to Manage
Practical management tools are essential for handling the complexities of EV development.
Project management software, such as Agile frameworks, are increasingly popular for their flexibility and emphasis on iterative progress and feedback.
Additionally, simulation tools and digital twins allow for detailed testing and modification of vehicle components in a virtual environment, minimizing the need for costly physical prototypes.
These tools collectively ensure that project milestones are met, budgets are adhered to, and product quality meets the high standards expected in the competitive EV market.
Through these strategic approaches, EV manufacturers are equipped to navigate the intricate landscape of new product development, ensuring that new EVs not only push the boundaries of technology.
Still, they are also viable and ready for the challenges of modern transportation needs.
Vehicle Evolution: The Battery’s Role in EV Dynamics – The Turbulence of Changing Technology
The landscape of EV technology is marked by rapid evolution, particularly in battery technology.
As manufacturers strive to increase energy density, reduce charging times, and improve safety, they encounter the inevitable turbulence of transitioning from established technologies to newer solutions.
For instance, the shift from lead-acid to lithium-ion batteries has unlocked significant advancements in range and efficiency.
Yet, it also introduces challenges related to battery lifecycle management, recycling, and raw material sourcing.
Incorporating cutting-edge materials like solid-state batteries presents a promising horizon for further improvements.
These technologies promise even greater energy densities and safety profiles.
Still, they also require substantial investment in new manufacturing processes and infrastructure, adding complexity to the industry’s evolution.
Costs and Early Adopters
The financial aspect of adopting new battery technologies in EVs plays a critical role in shaping the market. Initially, the costs associated with advanced battery technologies can be prohibitively high, limiting their accessibility to a broader market.
Early adopters, often driven by a combination of environmental concerns and interest in new technologies, play a pivotal role in this phase.
Their willingness to invest in premium-priced, cutting-edge vehicles helps manufacturers scale up production and eventually bring costs down through economies of scale and technological refinement.
Factors like range are important to the average consumer, but I contend initial cost is the principal deterrent to current EV adoption. The automotive OEMs who will succeed will be the ones that effectively drive out the costs of EVs to be priced at or near ICE vehicles. OEMs can’t do it alone so partnering with their suppliers and technology providers will be critical to their success: George Cuff, Director Key Accounts, Automotive, Manufacturing Intelligence division Hexagon.
As seen with several EV manufacturers, strategic partnerships and collaborations with technology companies specializing in advanced materials and battery solutions are crucial.
These alliances not only help share the financial burden but also accelerate the development and integration of innovative technologies into mainstream vehicle lines.
For example, companies like Hexagon is instrumental in providing high-precision digital solutions that optimize production processes and enhance the quality control measures essential in manufacturing complex battery systems.
Technology and Manufacturing Readiness in EVs – Simulations, Models, and Prototypes: Maturity (Product and Process)
Advancements in EV technology relies heavily on the maturity of both the product and the manufacturing processes.
By leveraging state-of-the-art simulations and prototypes, companies can predict and optimize the performance of EV components under various conditions.
Technologies from companies like Hexagon, which offer extensive modeling capabilities, are crucial in this phase.
These tools allow for a thorough design validation before it even reaches the prototype stage, thus ensuring that both product and process maturity are aligned with industry standards.
Testing (Simulation and Models to Prototypes Comparison)
Testing is pivotal in transitioning from simulations and models to actual prototypes. This step is critical to verify that the simulations accurately represent real-world behaviors.
For instance, Hexagon’s solutions facilitate this transition by providing detailed analytics that compare simulated outcomes with prototype testing results. This enhances reliability and drives further refinements in the prototype development and the simulation models.
While OEMs tackle the challenge of lowering EV costs, the average consumer will not accept lower quality as a means to the lower costs. Virtual simulation, automation and the use of the digital twin are several ways to ensure quality while helping to lower costs in EV development and manufacturing. George Cuff, Director Key Accounts, Automotive Manufacturing Intelligence division, Hexagon.
The Need for Tools
The development of EVs demands a complex array of tools, from CAD software for design to specialized software for battery management systems.
Integrating these tools into a cohesive workflow is essential for efficient design and manufacturing processes.
Tools that can handle large datasets, complex simulations, and real-time data processing are particularly valuable in this highly dynamic field.
Disparate Tools and Workflow the Road to Failure
One of the significant challenges in EV manufacturing is the integration of disparate tools, which can lead to workflow inefficiencies.
An example of this can occur when different departments use incompatible systems for simulation and physical testing, resulting in data silos and miscommunication.
A solution lies in adopting comprehensive platforms, like those offered by Hexagon, which integrate various manufacturing and design tools into a unified environment.
This integration helps minimize errors, reduce cycle times, and improve product quality by ensuring that all teams work with the same data and tools throughout the development workflow.
Driving Cost Out of EV Production with Digital Twin Technology
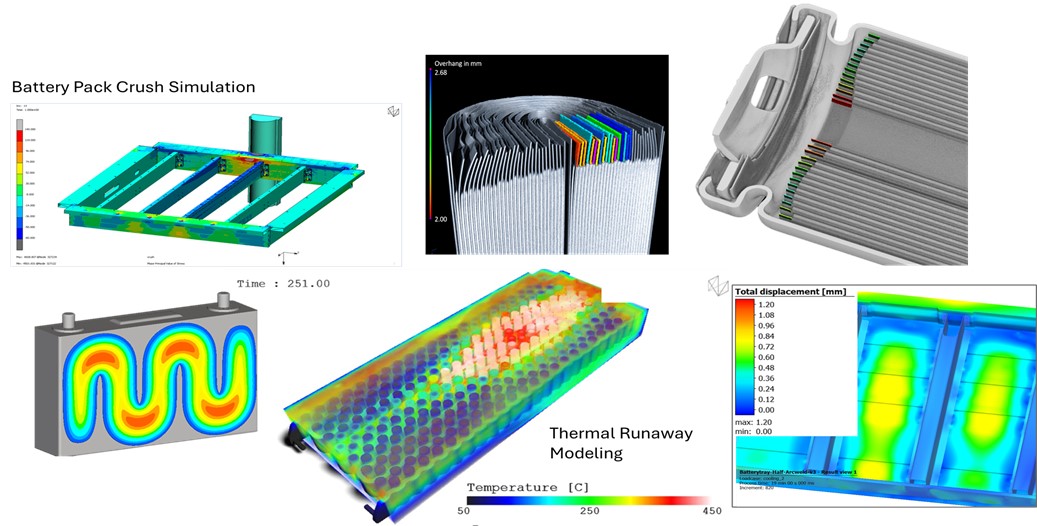
A digital twin is a virtual model designed to reflect a physical object or system accurately.
The concept is applied in product development in the automotive and aerospace industries to optimize physical systems’ operation, maintenance, and design.
Leveraging digital twin technology, as seen in platforms like Hexagon, manufacturers can create highly accurate virtual models of batteries.
These digital twins simulate real-world conditions and behaviors, allowing engineers to test and optimize battery designs using fewer costly physical prototypes (but not zero).
This approach not only slashes the time and expense involved in development but also enhances the sustainability of the manufacturing process.
We can predict how batteries perform under various design solutions and environmental and application scenarios (driving design).
Development is based upon iterations; the quicker we can iterate and learn, the quicker we reach our objective.
The approach minimizes waste and reduces cost and time to market without adversely impacting product quality.
Process Costs: Streamlining Production
Digital twins also play a crucial role in refining production processes.
By simulating the production line within a digital environment, companies can identify inefficiencies and potential bottlenecks before they occur in the real world.
Equipment and configurations for the manufacturing line can be explored.
This proactive problem-solving approach helps maintain a lean manufacturing process, significantly reducing the time and cost involved in EV production.
We can couple these iterations with line-working aspects using virtual or augmented reality.
This virtual environment enables engineers to simulate and analyze the behavior of the manufacturing line under various scenarios without the need for physical prototypes.
Engineers can test configurations, optimize workflows, and identify potential issues before any physical setup begins.
Volume of Units: Scaling with Precision
As EV manufacturers scale up their production to meet increasing market demand, managing the volume of units efficiently becomes increasingly challenging.
Here, digital twin technology offers the ability to test production at different scales, providing insights into the challenges and requirements of increased volume.
This foresight allows companies to efficiently adjust their processes and resource allocation efficiently, ensuring smooth and cost-effective scale-up.
In summary, integrating digital twin technology in EV manufacturing presents a formidable tool in reducing design and process costs while effectively managing large-scale production.
As the EV market grows, adopting such advanced technologies will likely become a standard, driving innovation and sustainability in the automotive industry.
For more on how digital twin technology is shaping the future of manufacturing, visit Hexagon.
Ensuring High Quality to Meet Customer Demand in EVs Through Automation
In EV manufacturing, automation plays a pivotal role in maintaining the quality and reliability that consumers demand.
A noteworthy advancement in this domain is Hexagon’s PRESTO system, which automates battery cell inspection.
This technology allows manufacturers to integrate both near-line and in-line inspection processes seamlessly.
Traditionally, battery cell inspection has been a bottleneck in production lines, often requiring manual intervention that is time-consuming and prone to errors.
The introduction of PRESTO changes this dynamic by employing automated robotic inspection systems.
“The problem lies in the difficulty to define a meaningful measure of performance.” ~W. Edwards Deming, Out of the Crisis
The power of automated robotic inspection lies in its ability to revolutionize the landscape of 3D measurement within the automotive sector.
By utilizing advanced robotics, PRESTO enables precise and efficient inspections, reducing the likelihood of defects and ensuring that each battery cell meets stringent quality standards.
This level of automation is crucial for scaling up production without compromising on quality, aligning with the industry’s push towards more sustainable and reliable EVs.
Measurements – Hexagon MARVELSCAN Handheld Scanner
As the EV industry evolves, the need for more sophisticated and flexible quality inspection tools becomes apparent.
Hexagon’s response to this need is the MARVELSCAN handheld scanner, designed to empower automakers with better metrology solutions that are accessible right from the early stages of the manufacturing process.
This tool exemplifies the shift towards democratizing access to quality data across all levels of production—from design engineers to factory floor workers.
The MARVELSCAN scanner provides a versatile and user-friendly interface that allows for rapid and accurate measurements of components.
This capability is crucial for automakers who aim to integrate innovation into their workflows without the constant need to revisit and rectify issues later in the production cycle.
By making advanced metrology tools like MARVELSCAN available earlier in the process, Hexagon is helping the automotive industry make more informed decisions, thus reducing costly reworks and ensuring that each vehicle meets the high standards expected by today’s consumers.
More information is available at Hexagon’s website to explore how the MARVELSCAN handheld scanner can transform quality inspection processes in automotive manufacturing.
Closing the Gap in EV Product Development
Developing EVs is an intricate process that demands innovation and a streamlined approach to manage its complexity.
The nature of such development involves a blend of diverse skills and expertise, often dispersed across various locations.
This geographic and functional diversity necessitates robust systems supporting seamless team communication and integration.
The rapid pace of the EV market adds another layer of urgency to the development process. Manufacturers are under constant pressure to accelerate product timelines from concept to market. Collaborating effectively across different functions and teams in this dynamic environment becomes critical.
Enter Hexagon’s Nexus, a solution designed to meet these challenges.
Nexus is a pivotal tool in EV development that connects cross-functional teams, data from wherever it was created and technology throughout the product lifecycle for effective decision making.
Leveraging cloud technology, distributed teams can work as if they were in the same room, ensuring that every phase of the lifecycle, from design to production and testing, is interconnected and aligned.
By adopting advanced collaborative technologies like Nexus, EV manufacturers can navigate the complexities of product development more smoothly and bring their innovative vehicles to the eager market faster than ever before.
More Stories
Automotive Industries (AI) Newsletter April 2025
Marelli focuses on Software-Defined Vehicle evolution at Auto Shanghai 2025, introducing the new ProZone zone control unit
Will Cars Function Like Smartwatches in the Future?