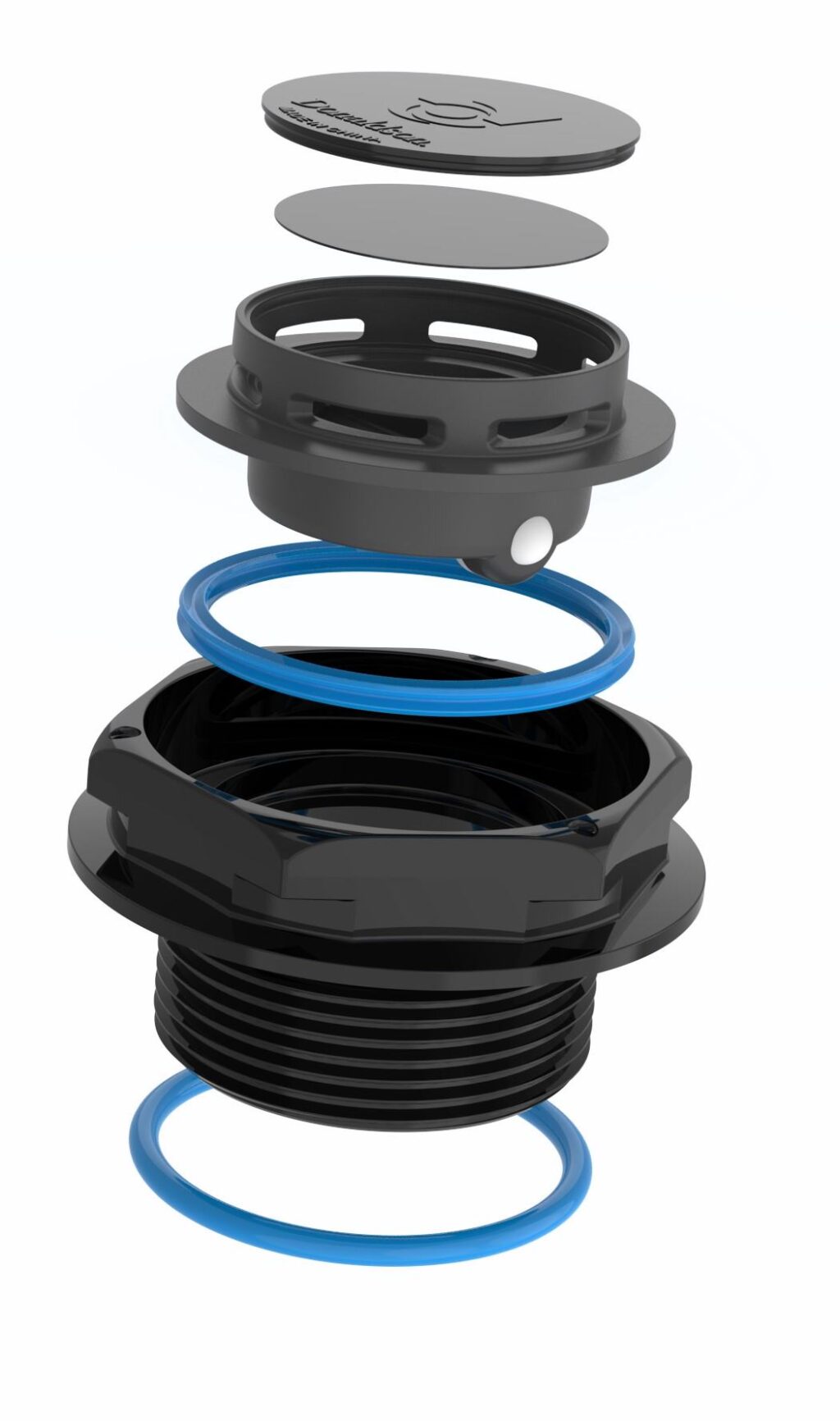
Donaldson has extended its range of battery venting systems with the Dual-Stage Jet, a design that takes electric vehicle (EV) safety to a whole new level by offering the industry’s fastest degassing capabilities, while streamlining the installation process for OEMs.
Launched at The Battery Show in Stuttgart, Germany, Dual-Stage Jet has been designed to meet the increased demands of more complex and powerful batteries – from providing enhanced pressure equalisation and ingress protection under normal operating conditions to allowing gases to escape at rates of approximately 100 lit/sec @ 100 mbar when necessary.
“Customers were telling us that they needed even higher degassing rates than what was available on the market, so the Donaldson Vehicle Electrification Development engineering team came up with a unique, creative design where the poppet and cap can be jettisoned to instantly produce a much larger opening for gas to escape and help mitigate thermal runaway,” explained Shane Campbell, Product Manager for Vehicle Electrification at Donaldson.
“The pressure then rapidly decreases inside the pack, greatly reducing the risk of damage to additional cells and giving occupants extra time to escape from the vehicle.”
Automotive Industries (AI) asked Campbell what the key considerations are for battery vent design.
Campbell: The first is pressure equalization during the normal operation of the battery pack. A vent protects the seals in the pack by allowing airflow in and out as pressure changes due to the heating up and cooling down of the battery.
You could achieve this by having holes in the side of your pack, but then there would be no protection from outside contamination.
Our vents use proprietary Tetratex® expanded polytetrafluoroethylene (ePTFE) membranes for enhanced protection from contamina
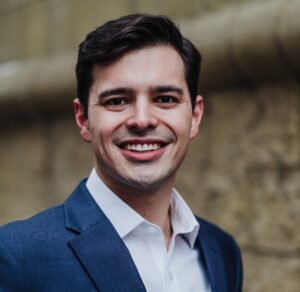
nts like water, automotive fluids, and dirt.
Effectively, it is a sealed system which breathes.
The second consideration is design for edge cases such as thermal runaway, which is rare, but can happen.
In the event of thermal runaway, we need to help mitigate propagation to additional cells.
With dual stage venting, the second stage has a higher airflow to expel hot gas and thereby reduce the temperature and pressure as fast as possible.
AI: What new products / technology did you present at the Battery Show Europe 2024?
Campbell: The focus of the vehicle electrification group was on our battery vents.
We are very excited about the release of our Dual-Stage Jet product. This is in addition to our existing Dual-Stage Burst battery vent.
We also exhibited some of our powertrain vents, and our solutions for fuel cell membranes.
AI: How does the Dual-stage Jet compare with the other products on the market?
Campbell: It is a unique design. We have not seen anyone else use this type of concept for battery venting.
It utilizes spring detent in the middle of the park, so the center body can pop off at a specified pressure.
This provides a very high degassing airflow, which is very important for our customers who have been asking us for higher and higher degassing airflow to help mitigate thermal runaway.
To achieve this, we needed to have the largest possible opening.
The new vent is the result of internal brainstorming and collaboration with customers to determine the best design.
The result is a unique design which is fresh to the market.
AI: What are the benefits?
Campbell: It has highest gassing airflow for its size of any vent in the market.
It also has a special membrane that allows much higher breathing airflow during normal operation, made in-house from Tetratex®.
Donaldson has a large membrane catalog from which to select, so we are not dependent on outside suppliers for our membrane and can select one with the best properties for the application.
At 58mm in diameter, and containing approximately 20% recycled plastic, the vent provides a simple solution to the occasionally tricky problem of performing a battery pack leak test with breathable vent installed.
Temporarily sealing the vent using the supplied leak-check cap is all that is required for manufacturers to carry out tests themselves.
Our customers can therefore perform end of line testing to ensure that their pack is fully sealed.
Another major benefit is that the vents can reduce the number required on a battery pack by 50-90%.
In addition to reducing the total cost of venting, this also leads to significant time and money savings in the assembly, ordering and stock-keeping processes.
AI: Is the new vent now ready / available for vehicle manufacturers?
Campbell: Dual-Stage Jet has been well received at the Battery Show. We have a lot of customers who are interested in this product.
Samples are available for testing and pilot builds.
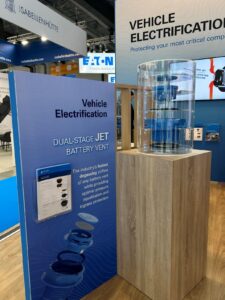
AI: Will Donaldson’s application engineers customize the design to the needs of a customer?
Campbell: One of the strengths of Donaldson is our ability to understand customer needs and to make the necessary adaptations.
The way we work is to develop a core technology, and to modify the attachment methods.
Dual-Stage Jet is available in two configurations – threaded or quarter-turn bayonet fittings.
The spring detent design allows for multiple configurations if we need to change a property such as opening pressure.
AI: What is next for Donaldson?
Campbell: We will continue to innovate in both battery and powertrain venting.
We have some new projects in the works to address different customer needs.
But one area I am very excited is to share our membrane expertise is for fuel cell proton exchange.
That market is, is growing, although it is at present lagging behind battery electric vehicles.
We have a lot of products for different applications whether it’s heavy duty, light duty or electrolyzer.
More Stories
Sensor Fusion and the Next Generation of Autonomous Driving Systems
Unique Experiences in Miami: What to Do Off the Beaten Path
The Factors That Impact the Outcome of a Car Accident Claim