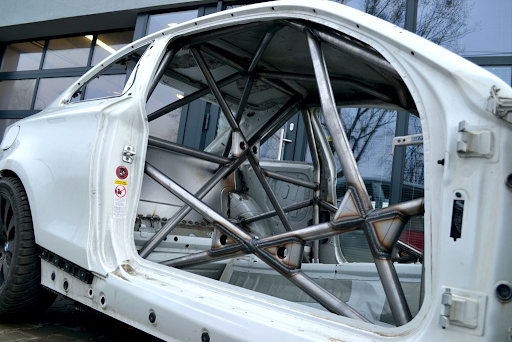
Roll cages are pivotal in enhancing vehicle safety, particularly in motorsports where the risk of rollovers and high-impact collisions is elevated. These frameworks are built within the passenger compartment of vehicles to protect occupants by reinforcing the structure to withstand severe impacts without compromising the interior space.
What Materials Are Commonly Used for Automotive Roll Cages?
Various materials are selected for roll cages based on their strength, weight, and durability. Here’s a look at the primary materials employed:
- Mild Steel: Affordable and widely available, ideal for most amateur racing scenes.
- Chromoly Steel (Chromium-Molybdenum Steel): Offers a higher strength-to-weight ratio, used in professional motorsports.
- Aluminum: Preferred for its lightweight properties though less commonly used due to its lower strength relative to steel.
- Titanium: High strength and extremely lightweight but more expensive, making it less common.
Steel Roll Cages
Steel, particularly mild steel and chromoly, is the most commonly used material in roll cage construction. Mild steel is easier to work with and less costly than chromoly, but chromoly offers a superior strength-to-weight ratio, crucial for maintaining high performance without adding unnecessary weight.
Aluminum Roll Cages
Aluminum roll cages are not as widespread as steel cages due to their lower tensile strength. However, in applications where weight reduction is critical, such as in racing sports cars, aluminum can provide a significant advantage, despite its potential for higher cost and specialized fabrication requirements.
Titanium Roll Cages
Titanium is considered a premium material in roll cage construction due to its exceptional strength and lightness. It is typically used in high-end motorsports where budget constraints are less of an issue. Its corrosion resistance and strength-to-weight ratio are unrivaled, but these advantages come at a higher price point.
How to Choose the Right Material for Your Roll Cage?
Selecting the correct material for a roll cage involves considering the type of vehicle, the nature of the racing, and the governing body’s regulations.
Considerations for Drag Racing
- Weight: Minimizing weight to maximize speed.
- Strength: Ensuring the structure can handle high acceleration forces.
Considerations for Rally and Off-road
- Durability: Materials must withstand rough terrains and repeated impacts.
- Flexibility: Some flexibility is necessary to absorb shocks without fracturing.
Regulatory Requirements and Safety Standards
Compliance with regulations such as those set by the FIA or NASCAR is crucial. These organizations specify acceptable materials and construction methods to ensure safety across all racing disciplines.
What Are the Properties of Roll Cage Materials?
Key properties to consider include:
- Tensile Strength: High tensile strength is crucial to withstand severe impacts.
- Ductility: Materials need enough ductility to deform under stress without breaking, absorbing energy during an impact.
- Corrosion Resistance: Good resistance increases the longevity of the roll cage, especially in harsh environmental conditions.
Analyzing Tensile Strength
The required tensile strength varies based on the type of racing; for instance, vehicles in high-speed races need materials that can handle extreme forces.
Importance of Ductility
A ductile material will bend rather than break upon impact, which is critical in dissipating the energy of a crash more safely.
Corrosion Resistance
Materials like titanium and treated steels offer enhanced corrosion resistance, important for longevity and reliability, especially in outdoor racing conditions.
What Are the Advantages of Each Material?
Each material brings unique benefits to roll cage construction:
- Weight Savings: Critical for performance, especially in racing.
- Strength: Essential for safety and durability.
- Cost-effectiveness: Important for budget-conscious teams.
- Ease of Fabrication: Simplifies the construction and modification processes.
Step-by-Step Guide to Designing a Roll Cage
Designing a roll cage involves several critical steps:
- Design Planning: Considering the vehicle’s structure and intended use.
- Material Selection: Based on the criteria discussed above.
- Fabrication Techniques: Including cutting, bending, and welding, tailored to the material chosen.
- Installation: Ensuring a snug fit within the vehicle without compromising structural integrity.
Design Considerations
Optimizing the design for weight distribution, ease of entry and exit, and compatibility with other safety features.
Fabrication Techniques
Techniques vary with the material; for instance, welding chromoly requires different settings and precautions compared to mild steel.
Tube notching
Tube notching is the method of cutting the end of a tube so it fits snugly against another tube, allowing for a stronger, more precise weld. This technique is essential in roll cage construction because it ensures that the joints are robust and have a high level of structural integrity. With the help of a tube notcher from Roguefab, the cutting process becomes easier.
Installation Tips
Ensuring the roll cage is securely integrated with the vehicle’s frame is paramount. Proper alignment and mounting are crucial for maximizing the effectiveness of the roll cage.
What Are the Latest Innovations in Roll Cage Materials?
Recent advancements include:
Composite Materials
Composites are gaining traction for their high strength-to-weight ratios and innovative applications in roll cage assemblies.
3D Printing of Roll Cage Components
3D printing allows for the creation of complex parts with precise specifications, potentially reducing weight and material waste.
Case Studies: Successful Roll Cage Implementations
Various racing teams have successfully implemented innovative roll cage designs, demonstrating improvements in safety and performance across different racing disciplines.
Common Mistakes in Roll Cage Fabrication and How to Avoid Them
- Inadequate Material Handling: Ensure the material is stored and handled to prevent damage.
- Improper Welding Techniques: Use the correct settings and procedures for each material type.
- Neglecting Fit and Compatibility: Ensure the roll cage fits perfectly within the vehicle’s interior.
Conclusion
Selecting the right material for a roll cage is crucial for both performance and safety in automotive racing. Each material offers distinct advantages and must be chosen based on specific racing needs, vehicle type, and regulatory requirements. With the correct approach to design, fabrication, and installation, a roll cage can significantly enhance the safety and competitiveness of a racing vehicle.
More Stories
Sensor Fusion and the Next Generation of Autonomous Driving Systems
Unique Experiences in Miami: What to Do Off the Beaten Path
The Factors That Impact the Outcome of a Car Accident Claim