
Envalior scope of products and services.
Formally established in April 2023, Envalior is the combination of complementary industry leaders in the engineering materials space, covering performance materials, specialty materials, and intermediates.
One was the former DSM Engineering Materials, and the other was LANXESS High Performance Materials.
Automotive Industries (AI) asked Thomas Brackemeyer, VP Business Performance Materials at Envalior to introduce the company.
Brackemeyer: The impression is that we are new in the industry, but it is only the name.
In truth, the two companies combine a heritage of over 100 years of experience.
Our name Envalior combines “En” (engaging, entrepreneurial, engineering, environmental) and “valior” (value-driven and value-creating).
This combination formed a global engineering powerhouse, which is certainly among the top engineering materials companies globally, with a turnover of about four billion euro.
We have 4,000 employees worldwide, with the two businesses having very complimentary global footprints, in Asia, in Europe and in the Americas.
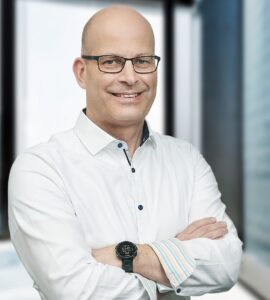
In order to add value to our customers we have organized the business into three divisions. They are performance materials, specialty materials, and intermediates.
Envalior has a portfolio of PA6, PA66, PBT, PA410, PA4T PPA, PA46, TPC, PET, PPS, and composite materials.
AI: What added value does Envalior bring to customers, compared to the two separate entities LANXESS Performance Materials and DSM Engineering Materials?
Brackemeyer: We bring together a unique value proposition and broad portfolio.
The depth of experience and design expertise together with the combined portfolio, the backward integration, and the combined global presence of the two companies, together with our approach to technology, is unique.
There is a strong track record in sustainability in both high performance and innovation materials. I see five main areas of benefit to our clients from this merger.
First is indeed the global reach, with research and development, and manufacturing close to our customers.
Second is a very strong and broad portfolio with innovative performance materials suitable for a diverse range of applications.
These materials support the automotive industry’s journey to new mobility.
Third is our design capability – we are very proud of our well established and strong design and simulation expertise to allow our customers around the globe to design according to latest technology standards from the start of a project.
This combines with the fourth area, which is an exceptional and deep selection of materials, which means that we have the right product for every application. That makes us really strong as a partner with our customers across industries.
Last, but not least, is our reputation as a trusted and solid partner, which is very important in these days with a lot of uncertainties. The company is profitable, so we will continue to be around for some time.
AI: Both companies that formed Envalior focused strongly on the mobility segment. Will Envalior continue to support trends like powertrain electrification, connectivity, and autonomous driving?
Brackemeyer: Absolutely, yes. Future mobility is one of our prime focus areas.
Right now, we are supporting our customers to transform to new mobility, with the process starting from the initial material selection, through the testing of the materials to approval and finally delivery materials. These materials support the transformation through lightweighting where plastics can replace metal in structural parts, which reduces the CO2 footprint of the vehicle.
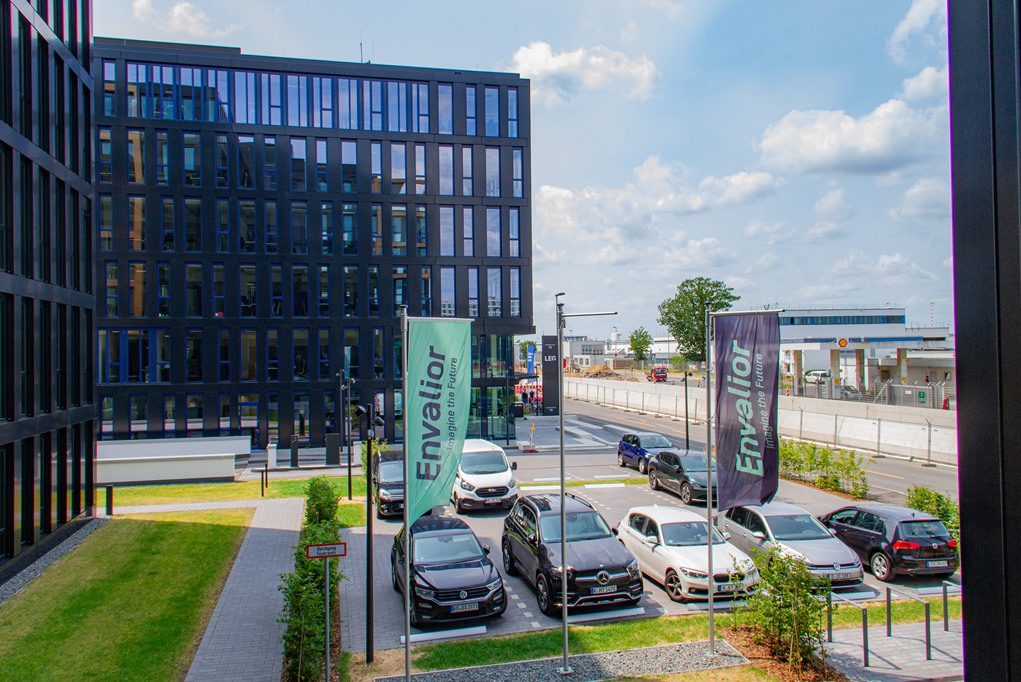
Our materials are used in battery systems and for both electric and hydrogen vehicles.
The materials are found in charging systems, electronic control systems, power electronics, and many other applications.
Three examples can illustrate the contribution we are making:
One is a battery weight reduction. Battery weight impacts range and microparticle emissions from tires and brakes, as well as the driving experience.
Lightweighting is even more important for electric vehicles than it is for cars with internal combustion platforms.
Depending on the platform, a high voltage battery typically adds an additional 400 to 700 kilograms to the car.
Working with our clients, we developed a plastic enclosure based on a combined solution of PA6 and local re-enforcement with Tepex organo sheets, which have high resistance to the extreme conditions of battery fires in a thermal runaway process.
Tests have shown that it can fully replace the aluminum and steel enclosures currently in use.
The second example is reducing charging time of EVs, which is also a very hot topic. We expect the 800-volt charging technology to become mainstream by 2025.
Many Tiers in the industry have started to move away from PBT to a PA 66 solution, purely because a halogen-free PBT with a CTI of 600 volt and good mechanical performance was simply not available in the industry.
This missing piece in the portfolio has been filled by halogen-free PBT, which does not only have a CTI of 600V, but also provides strength at comparable level of PA 66 polyamides, UL94-V0, hydrolysis resistant with an excellent silicone compression set to allow waterproof design concepts which can be adapted to meet customer needs.
Our customers can therefore continue using the easy to process PBT compounds of high dimensional stability and excellent electrical performance while combining the strong mechanics of polyamides with a broad and stable color portfolio in one compound.
The well-known issue of silver migration under the impact of electrical DC fields with PA66 are avoided because PBT is impervious to moisture absorption and has no free ions in the compounds.
The third example comes from our specialty product line, which is providing bearing stiffness at high temperature.
OEMs are reducing the size of electric motors to save on weight, materials, and space.
In order to produce the same power, the motors run at 30,000 rpm and more.
At such high rotation speeds, the performance of the bearings and the use of bearing cages becomes a challenge.
We have demonstrated that Stanyl PA46 outperforms any PA66 or ceramic solutions in mechanical performance and any PEEK alternative in terms of cost.
These three examples show that we have a broad portfolio and have solutions to support the industry through the change. In order to meet growing demand, we have increased production capacity.
The company has completed expansions at its Jiangyin and Changzhou sites, installing new compounding lines.
These locations now produce materials like PA46, PA4T, PA410, PA66, PA6, PBT, and TPC, vital for the automotive and electronics industries. Besides automotive, we also serve electronics, medical, food and health industries.
AI: For the automotive industry, time to market is crucial and a first-time right implementation is critical. How can Envalior help customers in such a dynamic and competitive environment?
Brackemeyer: Envalior has the capabilities to support customers in all the relevant phases of product development, depending on where our customers need us.
We support with material development to tailor-make compounds to meet application requirements, and with concept development to select the right material with the right design for an application.
Via computer aided engineering we can secure concept and series development, and processing support helps customers to solve production issues and reduce scrap rates.
Our part and material testing capabilities allow customized testing of parts and advanced material testing and finally our application test center support full component testing at the specific application requirements to characterize the final performance of an application under actual conditions.
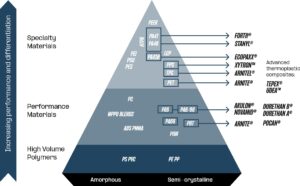
AI: Sustainability is another important topic. What will be the impact of the merger on your sustainability strategy?
Brackemeyer: We have a strong track record of being a front runner in sustainable innovations, and we aim to stay there.
Every day we work on developing carbon efficient and circular technologies within the industry to enable sustainable solutions across the value chain from materials used in customer applications all the way to reducing emissions and energy consumption of our own manufacturing footprint around the globe.
The reduction of the carbon footprint in the manufacturing process is becoming more and more important.
Another focus area is recycling.
We offer recycling based and bio-based grades throughout our portfolio, and we are committed to expand our portfolio in this direction. Both mechanical and chemical recycling are seen to be equally important in this journey in the future.
Here are a few examples that illustrate that we are an industry leader in this area.
We now have a portfolio of around150 bio-based and/or recycled-based grades with best-in-class materials, for instance Durethan ECO (PA6/PA66 with post-industrial recycled glass fibers) Pocan ECO (PBT with post-industrial recycled glass fibers) and Pocan ECO T (PBT/PET Blend with post-industrial recycled glass fibers and additionally post-consumer recycled PET).
Or take our bio-based Stanyl: A bio-based high-temperature polyamide which halves the footprint by 50%.
We are also famous for our Akulon Repurposed. It is made from abandoned recycled fishing nets and reduces carbon footprint even up to 82%.
It is not only used in for instance Samsung’s Galaxy S22 series, Schneider Electric’s Merten Ocean plastics range but also was the world’s first ocean plastic used by Ford in a commercial vehicle, on the Ford Bronco. Together with Ford we received the SPE award for this innovation.
And the additional compounding line in Jiangyin that we opened recently is powered by 100% renewable energy, partly from sourced energy and partly from solar energy generated directly on-site.
AI: What is next for Envalior?
Brackemeyer: We now have one of the broadest material portfolios in the industry, which means we can provide a one stop shop to a range of customers in different industries.
We aim to keep this broad mix of entry materials, whilst at the same time harmonizing overlapping product portfolios where possible ensuring the best solutions for our customers.
At the same time, we will expand our portfolio to support our customers and the transitions in the industry. And we want to do that in the most efficient way, to ensure that our customers benefit from having a sustainable, low-carbon, and very efficient supplier and partner in this industry.
More Stories
Will Cars Function Like Smartwatches in the Future?
Marelli to Showcase Latest “Speed-to-Market” Innovations at Auto Shanghai 2025
Unique Vacation Experiences for the Car Enthusiast