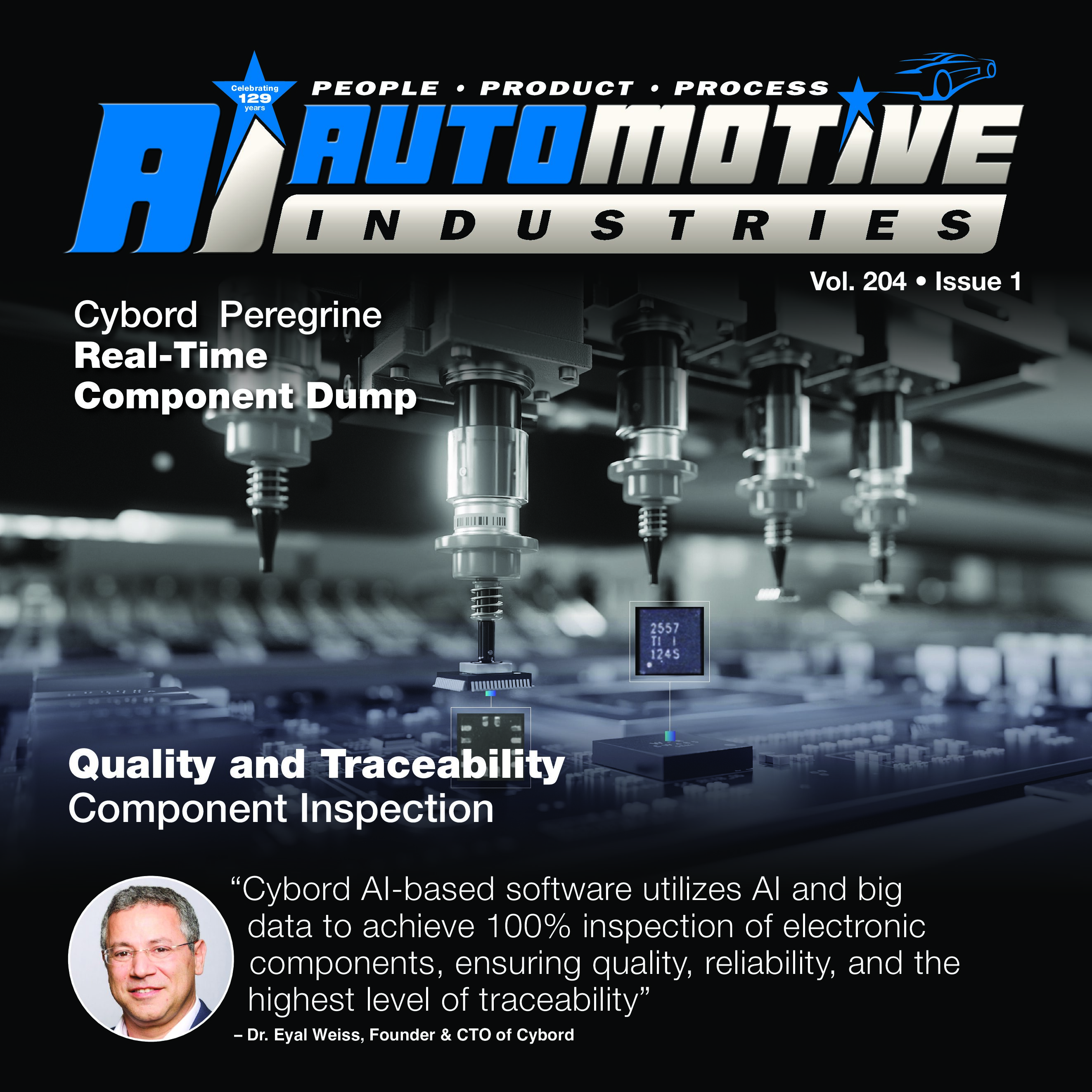
A crisis on a defense project has led to a breakthrough in real-time monitoring of the assembly of electronic components on the assembly line.
Dr. Eyal Weiss, Founder & CTO of Cybord, is an experienced technology development expert who has been managing successful multidisciplinary research and development projects for over 20 years and has won two Israeli security prizes.
A pivotal moment in Eyal’s career led to the founding of Cybord, with the mission to get counterfeit and defective components off production lines.
Following a crisis in a defense mega project caused by defective electronic components, Weiss and his team faced an uphill struggle to identify the root cause of the problem.
They eventually discovered that an inconspicuous 3-cent faulty capacitor was responsible for the crisis.
Highlighting the pervasive threat of defective components infiltrating production lines and jeopardizing the integrity of critical projects.
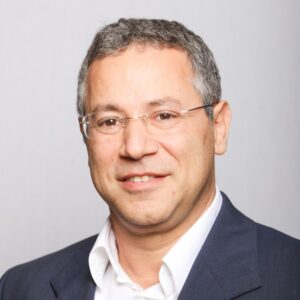
AI: Cybord QCI (Quality Component Inspection) Bottom Side Analysis: You have published a white paper which discusses bottom-side analysis during the pick and place (PnP) operation. How does the Cybord solution utilize this approach to identify and prevent defects such as damage, corrosion, and irregularities in the structure and leads of components?
Weiss: Cybord AI-based software utilizes AI and big data to achieve 100% inspection of electronic components, ensuring quality, reliability, and the highest level of traceability.
Cybord’s QCI solution leverages bottom-side analysis during the PnP operation to meticulously scrutinize electronic components as they are mounted onto printed circuit boards (PCBs).
By capturing detailed images of the bottom side of components during the assembly process, Cybord’s solution employs advanced algorithms to identify and prevent defects like damage, corrosion, and irregularities in component structure and leads.
Through a combination of machine learning and computer vision techniques, Cybord’s system analyzes the captured images in real-time, detecting even subtle abnormalities that may compromise component reliability.
This proactive approach ensures that defective components are swiftly flagged and segregated, preventing them from progressing further along the assembly line.
Furthermore, Cybord’s QCI solution enhances product quality and streamlines manufacturing processes, minimizing the risk of costly rework or recalls.
By providing early detection and intervention, our solution empowers manufacturers to uphold the highest quality assurance standards while optimizing production efficiency.
In essence, Cybord’s QCI solution offers a comprehensive and proactive approach to component inspection, safeguarding against defects and ensuring the integrity and reliability of electronic assemblies.
AI: How does the Automated Optical Inspection (AOI) operation combine with Cybord Traceability Component Inspection (TCI) to ensure that the mounting process was completed correctly?
Weiss: With Cybord’s TCI solution, AOI takes on a new dimension, focusing on component traceability accuracy rather than process issues.
By leveraging the images already captured by the AOI machine, Cybord’s TCI provides insights into the materials used in the assembly process, ensuring the accuracy and integrity of the components utilized.
Through meticulous examination of top-side images and inspection of markings and identifiers, Cybord’s TCI serves as a safeguard against fraud or errors that may occur along the supply chain.
Rather than relying on the documented history of materials, which can be convoluted and prone to inaccuracies, Cybord’s system seeks the source of truth in the components’ markings.
Utilizing advanced image processing algorithms, Cybord’s TCI scrutinizes top-side images to identify key markings and identifiers, including part numbers, serial numbers, date codes, and other unique attributes crucial for traceability and quality control.
These markings provide traceability information and help identify the manufacturer, ensuring visual traceability for all components.
Any discrepancies in authenticity, traceability, or markings are promptly flagged for further investigation, ensuring the mounting process is completed correctly.
Cybord’s TCI captures visual traceability information for each individual component mounted on every PCB, meeting IPC-1782B individual material traceability requirements.
The system provides high-granularity traceability data via an open API, seamlessly integrating with the customer’s traceability systems.
This automated flow of rich traceability data eliminates the need for manual data collection and organization, streamlining processes and enhancing efficiency.
In the event of a failure, this comprehensive information facilitates accurate recalls, reworks, and failure analysis, as quality parameters, top markings, individual lot codes, date codes, and images from both the top and bottom of components are readily available for traceability processing.
By seamlessly integrating with existing production systems, Cybord’s TCI elevates traceability and quality control standards throughout the manufacturing process, ensuring individual material traceability and product integrity.
AI: Can you explain the impact of the new Cybord solution, Peregrine real-time dump, in reducing rework and scrap by enabling the drop of components in 6 ms? How has this addressed the needs of OEM Tier 1 vendors in the automotive industry?
Weiss: In the automotive industry, where uncompromising quality standards and reliability are paramount, Peregrine caters to the needs of OEM Tier 1 vendors by furnishing a robust mechanism to elevate component quality and reliability.
The Peregrine solution is pivotal in driving efficiency and reducing rework and scrap across the manufacturing process.
Peregrine swiftly identifies and eliminates defective or non-compliant components within a mere 5-6 milliseconds by facilitating rapid component inspection between pick-up and placement in the pick-and-place machine.
This swift detection and removal process significantly diminishes rework, failures, and scrap, thereby optimizing production yield and curtailing costs associated with component defects.
Only high-quality components progress through the assembly process by addressing issues on the fly, mitigating the risk of downstream failures and quality issues in the final product.
Given that automotive products cannot undergo rework, the savings are substantial, as every faulty component results in the scrapping of an entire board.
By seamlessly integrating into the production line and furnishing real-time defect detection and removal capabilities, Peregrine empowers automotive manufacturers to uphold stringent quality control standards, enhance operational efficiency, and minimize downtime.
AI: How does Cybord’s AI technology, as outlined in the white paper, ensure 100% compliance with IPC-A-610 standards for electronic assembly acceptance criteria, specifically regarding defects on component leads and terminations?
Weiss: Cybord’s AI technology represents a significant leap forward in quality assurance by enabling real-time compliance verification of all components used and assembled.
Traditionally, standards like IPC-A-610 and IPC-J-STD-001 have been cornerstones in electronic manufacturing, outlining acceptable deviations and defects in the assembly process. However, before the advent of advanced AI technology, no automated means existed to enforce and qualify compliance during production.
Consequently, standards were primarily addressed post-mortem, serving as a method to classify deviations as either acceptable or defective after assembly.
The introduction of Cybord’s AI technology marks a paradigm shift in quality assurance, allowing for proactive qualification based on established standards for the first time.
By leveraging advanced algorithms and image processing techniques, Cybord’s system identifies and addresses defects in component leads and terminations in real-time, ensuring adherence to IPC-A-610 standards during the assembly process.
This transition from responsive compliance post-mortem to proactive compliance signifies a natural evolution in electronic manufacturing, driving efficiency, reliability, and product integrity.
Our white paper demonstrates how Cybord’s AI technology effectively proactively addresses current defects outlined in IPC standards, offering comprehensive quality assurance and compliance verification for electronic assembly processes.
Link to the IPC White Paper – https://cybord.ai/resources/ensuring-ipc-a-610-standard-compliance-by-using-the-cybord-platform/
For instance, IPC-A-610 standards outline common defects such as damage or deformation exceeding specified thresholds relative to the lead’s diameter, width, or thickness.
Cybord’s AI system employs sophisticated AI algorithms trained on a diverse dataset of known defects to analyze images of component leads captured during the assembly process.
By running predictive analyses and comparing lead dimensions against IPC-A-610 standards, the AI system accurately identifies any leads displaying damage or deformation beyond the stipulated thresholds.
Subsequently, these identified defects are flagged for further inspection or rejection, guaranteeing that only components meeting IPC-A-610 standards are accepted during assembly.
Moreover, Cybord’s AI technology extends its capability beyond detecting damage or deformation, proficiently identifying a spectrum of other defects delineated in IPC-A-610 standards.
These include bent or warped leads, corrosion, cleanliness issues, and loss of metallization. Leveraging advanced image processing and machine learning techniques, Cybord’s AI system delivers comprehensive defect detection, thus ensuring the highest level of quality assurance in electronic assembly processes.
AI: What types of defects outlined in IPC-A-610 does Cybord’s system detect, and how does it accomplish this?
Weiss: Cybord’s system employs a unique approach to detect defects outlined in IPC-A-610 by inspecting each component from its bottom side, which becomes invisible after mounting.
The system generates robust AI models that achieve high accuracy and efficiency by utilizing advanced AI methods, including deep neural networks and smart feature clustering.
The key to our system’s success lies in the vast volume of components processed, over four billion, enabling the development of highly accurate models with accuracy levels surpassing 99.9%.
One crucial aspect of our detection method involves evaluating the age and corrosion state of components by correlating the gradual oxidation of their leads.
Initially, brand-new leads exhibit a clear and reflective surface.
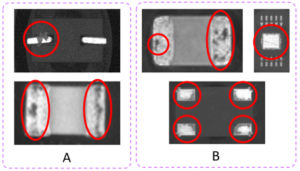
However, as leads age while exposed in their reel, they undergo slow oxidation, leading to increased surface roughness due to intermetallic interactions.
Consequently, the emissivity of the surface changes, which is visually detectable.
Our AI algorithm leverages these changes to accurately estimate the age of the component based on its surface roughness. It is much like the difference between a clear mirror and a distorted dull mirror.
As corrosion progresses, the surface becomes increasingly spotty and wavy, further affecting component visibility.
The system’s predictive models have been extensively validated using real-life data and verified through numerous lab analyses, confirming Cybord’s accurate predictions of component age and corrosion contamination.
It’s important to note that corrosion is strictly prohibited by IPC-A-610 section 10.6.4 for cleanliness and surface appearance.
By proactively identifying and addressing corrosion issues, Cybord’s system ensures compliance with industry standards and enhances overall component quality and reliability.
AI: The white paper mentions the analysis of markings and identifiers. How does Cybord’s AI platform ensure surgical traceability, and what role does it play in avoiding incorrect or missing marking issues as defined in IPC-A-610 Section 10.5?
Weiss: Cybord’s comprehensive inspection and quality assessment processes ensure that all assembled components on every board undergo rigorous scrutiny, achieving the highest level of traceability achievable under IPC-1782B, which focuses on individual component-level traceability.
By capturing and storing images from both the top and bottom sides of components, along with the results and classifications of all visual AI tests, Cybord enables surgical traceability.
In the event of a recall initiated by a component exhibiting distinct visual failure, such as corrosion, the system can precisely locate all boards containing components with clear evidence of corrosion.
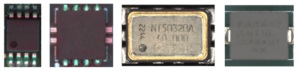
This targeted approach allows for recalling only the affected fraction of the production batch, minimizing disruptions and costs.
Additionally, Cybord leverages the top marking of components as a primary source of truth, providing finer data resolution compared to supplied documents.
By automatically identifying all traceability information encoded on components, smaller subgroups of production lots become visible. In the case of a recall, only the specific marking lot associated with the affected components needs to be recalled, preventing the need for a large-scale recall and optimizing efficiency.
Cybord identifies and verifies markings in real-time, ensuring accurate traceability throughout the manufacturing process.
This capability is crucial in avoiding incorrect or missing marking issues as defined in IPC-A-610 Section 10.5, thereby enhancing quality control and preventing potential defects in automotive electronic components.
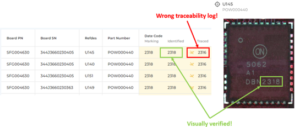
Using deep neural networks trained on billions of processed cases, Cybord’s system effectively detects various component defects, including body defects, distortion, bent leads, and peeling metallization.
These defects are critical to address as they can compromise the integrity and reliability of electronic assemblies.
Our AI models are specifically trained to ensure conformance to IPC-A-610 standards, particularly focusing on the following defect categories:
- Defects on Component Leads/Terminations (Section 8.2.2)
- Bent or Warped Leads (Section 8.3.5.8)
- Cleanliness – Foreign Object Debris (FOD) (Sections 10.6.2 & 10.6.3)
- Loss of Metallization (Sections 9.1, 9.3)
By leveraging advanced AI technology and vast datasets, Cybord’s system provides accurate and reliable detection of these critical defects, contributing to improved quality control and adherence to industry standards in electronic manufacturing processes.
More Stories
Automotive Industries (AI) Newsletter April 2025
Marelli focuses on Software-Defined Vehicle evolution at Auto Shanghai 2025, introducing the new ProZone zone control unit
Will Cars Function Like Smartwatches in the Future?