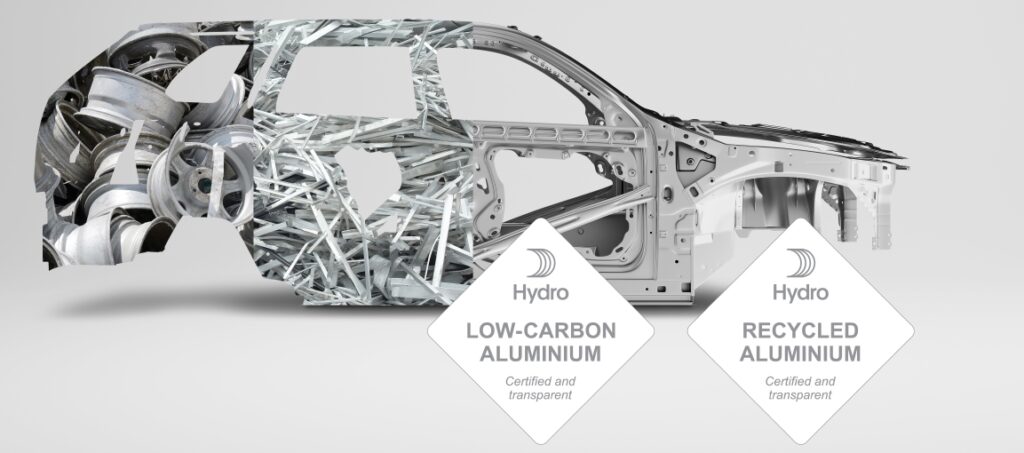
A vehicle body made from recycled aluminum.
The beauty of electric vehicles is that they have zero tailpipe emissions. But as with all other vehicles, their materials, manufacturing processes and end-of-life disposal continue to create a significant carbon footprint.
Reducing this footprint is a multi-disciplinary challenge that includes companies like Hydro Extrusions, a leading global supplier of automotive aluminum solutions.
Automotive Industries (AI) asked Piotr Chmielewski – Head of Automotive, Europe, at Hydro Extrusions, how aluminum can help reduce the carbon footprint of electric vehicles.
Chmielewski: Aluminum’s influence in lowering the carbon footprint of EVs is obvious, and this starts with reducing the overall weight of the car. Lowering the vehicle weight increases battery range and performance, which is crucial. Improved range also tackles one of the biggest concerns for potential buyers and users, which will most likely increase and accelerate the growth of electric cars.
For me, the more important element is sustainability through decarbonization. This can be achieved by keeping or even improving the carbon content and recyclability of EV parts and components.
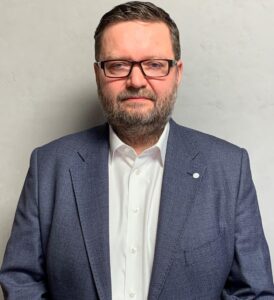
Here, aluminum is a perfect fit. It can be designed for multiple applications including crash management components and battery housing, with lightweighting benefits, to help customers lower the environmental footprint of their cars.
With carbon footprint, we have to consider all the phases – production, use, and end-of-life – to gain the maximum impact. There are pragmatic reasons for switching to aluminum. Some recent studies estimate that by 2030 the average car will have 40 kilograms more aluminum than today. If this gives you a weight saving of 10%, it means that you have reduced the vehicle’s weight by four kilograms.
This helps. Every step matters.
Further savings come from the production process. Hydro’s low-carbon aluminum products carry a carbon footprint of just below four tons of CO2-equivalents (CO2e) per ton of aluminum – or less, which is the lowest global number.
AI: How important is it to look further than emissions?
Chmielewski: It is really about the full value chain. For example, our casthouses can deliver specific automotive applications that include a significant percentage of recycled aluminum using low-carbon production technologies to reach our long-term targets of being net zero.
Over the long term, the value of aluminum material lies in its circularity. Recycling is not just about decarbonization or extending the range of electric cars, it is about sustainability.
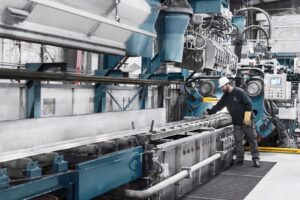
Some 75% of the aluminum that has been produced is still in use, and recycling aluminum requires only 5% of the energy used to produce primary aluminum, during which the metal retains all its performance properties.
In addition, Hydro has operations focused on the recycling of EV batteries, including a new facility in Norway. And as a pioneer in Europe, we use advanced sorting technology to enable us to use even more post-consumer scrap in our recycling operations on the continent.
AI: How do you tackle CO2 during production and not just during the vehicle use phase?
Chmielewski: We have the knowledge and the capabilities to produce metal with very low CO2 emissions, and this is developing day by day. With emphasis and focus on the full production process – from mining to end-of-life recycling – we are able to produce low carbon aluminum that supports our customers in reaching their sustainability ambitions and targets.
Recycling is really important to avoid duplicating the carbon cost of extraction and primary production and, in turn, to creating a more circular economy. Hydro has a low-carbon strategy for the full value chain. Wind and solar farms are being commissioned in numerous locations and by installing and utilizing renewable energy, we are decarbonizing our production sites and operations. For example, one of our new presses in Trzcianka, Poland, uses energy supplied by our own solar farm. This results in a very low CO2 footprint. We call this our “green press” because it has the lowest emissions from the production phase from our network of European sites.
AI: What about capacity?
Chmielewski: Hydro aims to add significant tonnage of new recycling capacity to our portfolio by 2027, primarily in Europe and North America, to meet the growing demand. This will provide even more capacity to supply the automotive industry with low-carbon recycled aluminum from post-consumer scrap.
Hydro Extrusions has inaugurated three new presses in Suzhou, China, Nenzing, Austria, and in Trzcianka, as I mentioned. This strengthens our portfolio of cutting-edge extrusion technology while increasing our capacity to support growing industries like automotive, with the focus on electric vehicles.
Our extrusion capacity in Europe, to support the growing electric car market, has been increased with a major investment in a new, high-strength press at our plant in Szekesfehervar, Hungary, which will start production by the end of this year. The new press is part of Hydro’s automotive network, which also includes an automotive-dedicated extrusion press investment in Tønder, Denmark. Together, the new press in Denmark and our existing P5 press in Hungary, will give Hydro unmatched capabilities to supply the automotive market anywhere in Europe, with the best available technology and a strong focus on carbon footprint.
On top of this, we are investing in a new casthouse at our main automotive plant in Szekesfehervar. This will improve our circularity strategy through increased capacity in post-consumer scrap recycling, and through supplying our extrusion presses from the same location.
In addition, we have dedicated groups working very hard on building automation roadmaps for our plants in order to meet the challenges of the labor market and future developments. This is another key factor, because having more robotics in our plants will make us more efficient in all operations.
AI: What is your automotive network’s unique selling point to high-volume car manufacturers?

Chmielewski: Through our network of plants and vertical integration, we cover all aspects of aluminum production, extrusion and casting, with a wide geographical footprint that enables us to handle peak and global platform projects.
Our access to low-carbon materials, with full traceability and transparency along the entire supply chain, is helping car manufacturers make significant reductions in their carbon footprint. This transparency is important because there are a lot of different ways of calculating emissions.
We have alloys with 75% post-consumer content, and we are heading toward 100% recycled raw materials. We also have strategic partnerships, mainly with European OEMs, which helps them to improve or to reach their decarbonization targets.
AI: What e-mobility projects and applications are you targeting with the new investments?
Chmielewski: There is no secret that the current e-mobility trends are changing the penetration of aluminum in car construction. A recent study by Ducker predicts that the use of aluminum in vehicles will nearly double by 2030. This means there will be more aluminum parts used in the car, such as battery trays, structural parts for crash management and body-in-white components.
So, we are targeting this future group of products without losing our focus on the components we presently supply and on other specific products where we are also quite strong.
AI: What is next for Hydro Extrusions?
Chmielewski: The predictions are that the automotive industry will have a demand of over 700,000 tons of extruded aluminum products by 2030. This is significant growth, and the capacity that we are building and securing now will not be sufficient in meeting this growth in demand. It will be quite demanding on all of the automotive aluminum players to be able to meet this demand.
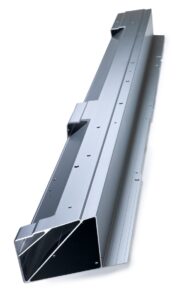
We should also bear in mind that by 2030, only around 65% of the cars produced will be electric.
The remaining 35% will be powered by combustion engines. Over the following five years, from 2030 to 2035, we will move to 100% of production being electric cars, which to me is a signal that the aluminum market will need more specialist players.
For the short term, we will bring all our new investments into production over the next two years.
We have already been successful in securing orders for production for the new plants. So, we will be working on ensuring there is a stable startup as they come into production.
For the medium term, we are considering more investments to support the automotive sector, which may include transforming some of our existing extrusion plants to be able to meet the needs of car manufacturers.
We will continue to work closely with the OEMs to strengthen our partnerships in order to optimize the design of the products in order to reduce weight and increase recyclability. We have the capacity as well as a strong sustainability offering, and we are working closer with our automotive customers. This will also help us to grow further.
But I believe it is our sustainability offering that is our real strength. I, along with many others, consider us to be the front-runner here and I am confident we will continue like that. These developments, and the investments I mentioned, are all part of Hydro’s roadmap, which aims to create multiple pathways that work together to help us reach near-zero products today, and net-zero products in the future.
More Stories
Sensor Fusion and the Next Generation of Autonomous Driving Systems
Unique Experiences in Miami: What to Do Off the Beaten Path
The Factors That Impact the Outcome of a Car Accident Claim