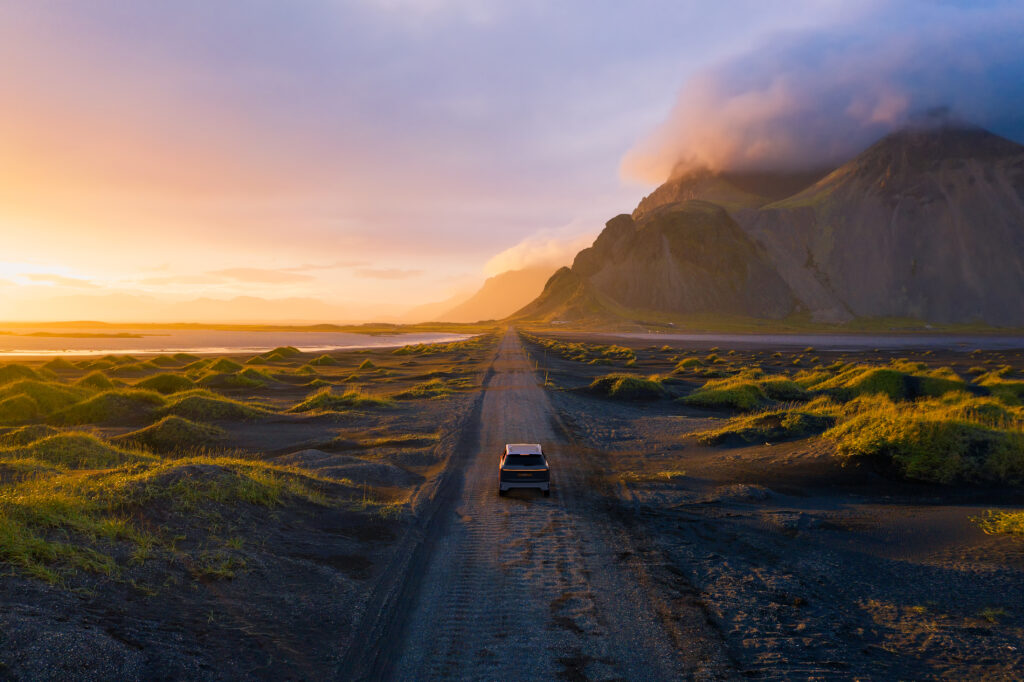
Gravel road at a golden Sunset with Vestrahorn mountain in the background and a car driving the road in Iceland
The automotive industry is in the midst of a transformative shift towards electrification.
As automakers drive for sustainable, efficient, and high-performance electric vehicles (EV), the role of advanced materials and innovative solutions has become more critical than ever.
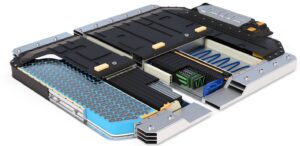
From lightweight materials, advanced battery materials and protective coatings to intelligent solutions tailored for electric and autonomous vehicles, the market for automotive solutions is rapidly evolving.
BASF, a leading innovator in the automotive industry, is poised to play a pivotal role in this transformative shift through its leading technologies and sustainable solutions designed to meet the unique demands of the electric vehicle market.
In close collaboration, BASF, automotive manufacturers, and other industry partners are committed to working on driving electrification forward – together.
Innovative batteries with BASF battery materials
On the way to offer more affordable and higher performance electric vehicles, innovations are needed in battery material development to enable extended real driving range, shorter charging times, smaller, safer and longer service life batteries for EVs.
One example is innovations like BASF’s cathode active materials that significantly influence the most important properties of a lithium-ion battery.
Chemical composition, particle engineering and a smart production process are decisive factors. When these factors achieve an ideal balance, electric cars can be charged faster and can travel farther on a single charge.
BASF is a leading global supplier of advanced cathode active materials for the lithium-ion battery market, supplying the world’s largest cell producers and OEMs with high performance cathode active materials.
With production sites in today’s key regions for EVs – Asia, Europe, and North America, BASF’s teams are best positioned to provide tailor-made solutions to its customers.
In addition, the company offers base metals sourcing and management as well as closed-loop battery recycling solutions to reduce batteries’ CO2 footprint and help ensure the supply of critical metals for new batteries.
BASF presently offers cathode active materials based on recycled metals as a closed-loop solution in Asia, North America, and Europe.
The company is ready to ramp-up its recycling capacity to meet the growing demand from battery manufacturers and OEMs to recycle battery production waste and end-of-life batteries in the future.
At present, the market for electric vehicles is fragmented into three major segments, differentiated by cost and performance: the entry-level segment for the lowest battery cost; the volume segment for a good balance of battery performance and cost; and the performance segment for maximum range and power of the battery.
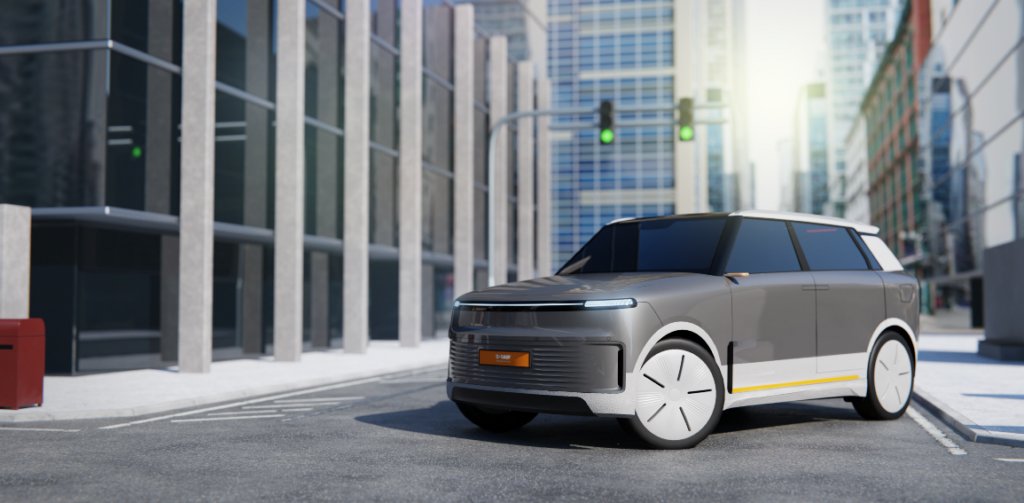
BASF’s focus is primarily on the volume and performance segments because this is where the higher performance of cathode active material technologies such as NCA (nickel-cobalt-aluminum mixed oxide) and NCM (nickel-cobalt-manganese mixed oxide) come into play.
One of BASF’s latest product developments in battery materials are manganese-rich cathode active materials. Research and development teams have succeeded in increasing the manganese content while at the same time significantly reducing the cobalt content. Cobalt is both expensive and limited in supply.
As a result, the company can offer its customers high-manganese and low-cobalt cathode active materials at a lower cost while maintaining the same level of performance.
Today’s e-Mobility innovations require high-performance material solutions
Cathode active materials are only one piece of the electric mobility (e-Mobility) puzzle. Many e-Mobility solutions can only be implemented successfully by using highly versatile engineering plastics, polyurethane systems and specialty elastomers.
Material performance is key: Individual components need to meet high-performance standards during normal driving and in the event of damage or accidents, which means that any material used needs to be carefully assessed by its flame retardancy, electric isolation, thermal conductivity and cooling compatibility.
BASF offers several polymer solutions for high voltage batteries used in the battery pack, battery module, and for thermal management – Ultramid®, Ultramid® Advanced, Ultradur®, Elastollan®, and Elastolit® family of products are only some examples that make high performance battery components a reality.
All BASF solutions for these applications can be found in the Battery Pack Visualizer tool.
Long-lasting protection with the right surface treatment
As electric vehicles continue to grow in popularity, it is imperative to address the unique challenges faced by their platform designs and battery systems. This includes the pre-treatment of surfaces as well as the actual coating process. BASF’s technology range comprises a tailored product portfolio of automotive pre-treatment and e-coat solutions ensuring longevity and performance.
Preventing corrosion helps to maintain the structural integrity of the car bodies and battery systems ensuring their reliability and extending their lifespan.
BASF´s Oxsilan® thin film technology provides a thin and uniform protective layer on metal surfaces, to enhance corrosion protection in combination with the CathoGuard® technology.
The innovative Oxsilan® technology therefore contributes to the battery system´s performance and durability.
On this foundation, the CathoGuard® portfolio provides solutions designed to protect multi-metal car bodies and components, making them suitable also for the covers of the battery construction. This compatibility ensures comprehensive corrosion protection across all battery components.
By preventing corrosion on the parts surrounding the battery construction, BASF’s coating solutions contribute to enhance the longevity of batteries.
Manufacturers can thus produce sustainable solutions meeting the demands of the growing e-Mobility market.
Enabling sustainable e-Mobility with BASF’s automotive solutions
Combining economic and ecological advantages, BASF’s solutions play a crucial role in enhancing the efficiency, durability, and sustainability of electric vehicles.
This is essential for making them a more appealing and sustainable choice for consumers and society as a whole. By reducing environmental impact and ensuring the long-term availability of critical materials,
BASF’s automotive solutions drive continuous advancements in the electric vehicle industry.
This aligns with BASF’s commitment to creating chemistry for a sustainable future and supports the transition towards a more environmentally friendly transportation sector.
For more information about BASF’s Automotive Solutions, please visit www.basf.com/automotive.
More Stories
Sensor Fusion and the Next Generation of Autonomous Driving Systems
Unique Experiences in Miami: What to Do Off the Beaten Path
The Factors That Impact the Outcome of a Car Accident Claim