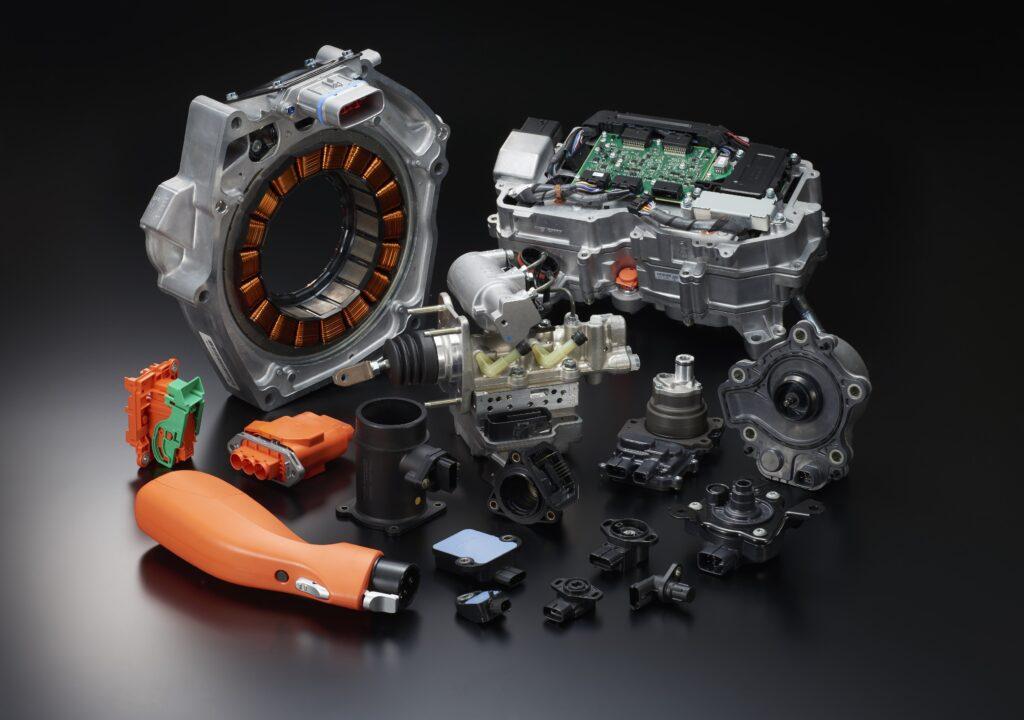
Welcome to this insightful interview with Yohei Iizuka, the managing director of Polyplastics Europe GmbH, shedding light on Polyplastics products and their critical role in engine and transmission applications within the automotive industry. This conversation delves into the material specifications, application suitability, advanced manufacturing techniques, material compatibility with lubricants and fluids, tolerance to high temperatures and thermal cycling, and Polyplastics’ commitment to sustainability and environmental responsibility.
Polyplastics’ materials, especially DURAFIDE PPS, DURANEX PBT special grades, DURACON POM Copolymer grades, play a pivotal role in engine and transmission applications. For internal combustion engine (ICE) vehicles, high temperature and chemical resistance are paramount, making PPS a key material for the powertrain. Conversely, battery electric vehicles (BEVs) necessitate flame resistance, high Comparative Tracking Index (CTI), and weight reduction, favoring DURANEX PBT and PLASTRON LFT materials.
Ensuring the materials meet specific requirements and standards involves close cooperation with design engineers from OEMs and tiers 1 and 2. Polyplastics gathers early insights into technical requirements and specifications for projected applications, facilitating tailored material development. Customers can access technical support through dedicated account managers, Technical Solution Centers (TSC), or the web portal, where they can enroll in the WEB@TSC system for 24/7 technical guidance.
While Polyplastics doesn’t directly manufacture components, they produce advanced polymer compounds, providing design and processing support to help customers create optimal parts for their applications. Extensive compatibility testing and chemical resistance tests are conducted to ensure the materials maintain structural integrity and performance in the presence of automotive lubricants and transmission fluids.
Polyplastics conducts rigorous testing to ensure the mechanical properties and structural integrity of their materials endure high-temperature conditions and thermal cycling typical in engine and transmission components. The company offers comprehensive support, including CAD, CAE, and processing advice, as well as access to their mold shop in the Tech Center in Fuji for mold testing and product familiarization.
Regarding sustainability, Polyplastics emphasizes recyclability and reduced environmental impact during the product lifecycle. They conduct testing on regrind usage and multiple processing, and their material brochures offer recommendations regarding the environmental impact of these practices, underlining their commitment to a greener and more sustainable automotive industry.
Material Specifications and Performance:
Automotive Industries: What are the key material specifications and performance attribute of Polyplastics products utilized in engine/transmission applications? (e.g., mechanical properties, thermal stability, chemical resistance)
Iizuka: For ICE driven vehicles, high temperature resistance in combination with chemical resistance is decisive. PPS is a key material for the powertrain in ICE vehicles. But the situation is different for BEV. Here flame resistance, high CTI, and weight reduction are important. Such favoring DURANEX PBT special grades and PLASTRON PA LFT material. Furthermore, the thermo-management for BEV is very complex. Due to lower temperatures than in ICE cooling systems, DURACON POM Copolymer grades will play an important role.
Application Suitability:
Automotive Industries: How does Polyplastics ensure that its materials meet the specific requirements and standards for engine and transmission applications in the automotive industry?
Iizuka: We cooperate closely with the design engineers, both OEM and tier 1 and tier 2. So we have early information about the technical requirements and specifications of the materials in projected applications. Our customers can reach out to us via the account manager or directly contact our TSC Technical Solution Centers or through our website www.polyplastics.com. Here one can enroll in our WEB@TSC system free of charge and get 24/7 technical advice.
Advanced Manufacturing Techniques:
Automotive Industries: Could you elaborate on the advanced manufacturing techniques that enable the production of Polyplastics components for engine and transmission applications, emphasizing precision and efficiency?
Iizuka: More precisely, we do not produce components or form parts. We manufacture advanced polymer compounds according to the needs of the design engineers. We render full design and processing support to enable our customer to manufacture the best-fitting parts for the applications.
Material Compatibility with Lubricants and Fluids:
Automotive Industries: How do Polyplastics materials maintain their structural integrity and performance in the presence of automotive lubricants and transmission fluids, considering potential chemical interactions?
Iizuka: We run extensive compatibility testing and chemical resistance tests with our materials. In cooperation with our partners, we get to know the chemical environment of parts made from our material and can propose the best solution.
Sustainability and Environmental Impact
Automotive Industries: How does Polyplastics address sustainability and environmental concerns in the development and usage of their materials for engine/transmission applications, including any efforts in recyclability and reduction of environmental impact during the product lifecycle?
Iizuka: Recyclability in the sense of using regrind and multiple processing is tested by grade in our Tech Center. Recommendations about the impact of the use of regrind or multiple molding are published in the material brochures.
More Stories
Industry-standard switching & simulation systems from Pickering Interfaces on show at Space-Comm Expo
Bangkok International Motor Show 2025 – The Talk of Sensuous Automotive
SEPA and Bidgely Release Report on the Power of AI for Transportation Electrification