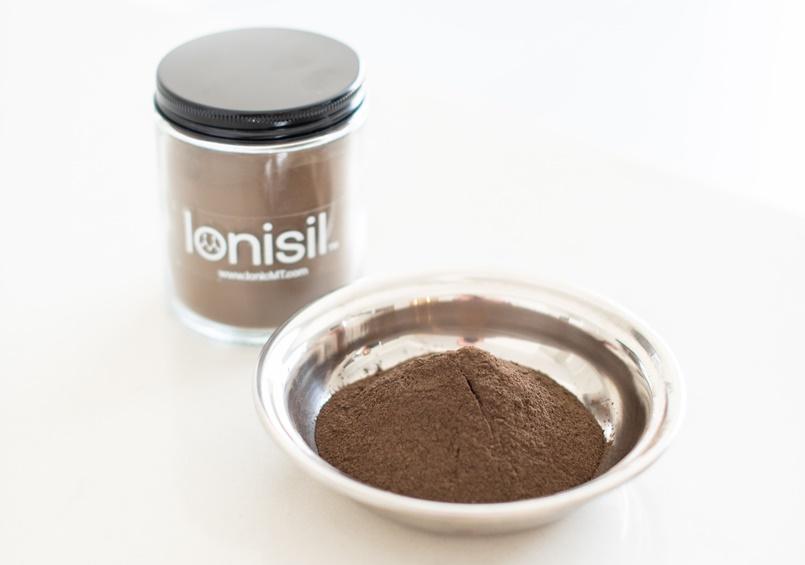
Ionisil™, a proprietary halloysite-derived nano-silicon.
Breakthroughs in battery technology are helping OEMs to overcome the twin challenges of range anxiety and long charging times.
Utah-based Ionic Mineral Technologies (Ionic MT) has developed a nano-silicon which, it says, can replace graphite in electric vehicle (EV) batteries. It can reduce charging time 8-fold and 40% increase in energy density. That means more driving and less charging time as well as a longer range for EVs.
The company’s mission is to be the world’s leading producer of drop-in nano-silicon anode powders for the next generation of advanced lithium-silicon batteries.
It has developed Ionisil ™, a proprietary halloysite-derived nano-silicon, which delivers considerable advantages to lithium-ion battery makers, according to the company. Halloysite is an aluminosilicate clay mineral. Its main constituents are oxygen (55.78%), silicon (21.76%), aluminum (20.90%), and hydrogen (1.56%).
Halloysite-derived nano-silicon can replace graphite (or be used in a composite), generating far greater performance by reducing the swelling, cracking and deterioration compared to traditional silicon cells, according to the company. Halloysite-derived nano-silicon is already commercially viable. The nano-silicon feedstock material derived from halloysite comes at a “small fraction of the cost of the traditional silane gas-derived nano-silicon feedstock material,” the company says.
Halloysite is plentiful in the United States, with millions of metric tons available at the Ionic MT site. The Ionic MT-owned mine has one of the world’s largest deposits of high-purity halloysite clay nanotubes, the ideal nano-silicon feedstock.
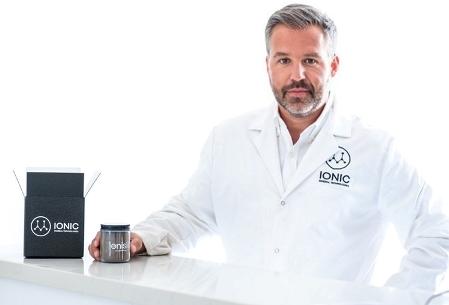
Ionic MT has commissioned its nano-silicon pilot plant facility to produce halloysite derived nano-silicon. It is currently under construction and is slated to come online in the second half of 2023. Ionic MT says in a media release that it believes its nano-silicon will be used to power a clean, electrified future, produced with the most sustainable process for manufacturing nano-silicon. The company’s process employs green chemistry and engineering principles leading to much lower energy usage and carbon emissions than competing nano-silicon processes.
Automotive Industries (AI) asked Andre Zeitoun, Founder and CEO of Ionic Mineral Technologies, what makes Ionisil so suitable for use in high performance batteries.
Zeitoun: What makes our material unique is a few things: because of our vertical integration and because of our ability to use a feedstock from the mineral halloysite, we have a very scalable process that can make the large volumes of material needed by the automotive industry, versus the synthetic silane approaches of some of our peers.
From a performance standpoint, we are making a 100% silicon product versus a silicon carbon composite. One of the benefits of silicon in general is that it is the only material that can be dropped into existing manufacturing processes. Silicon addresses the big supply issues that the industry has with lithium and graphite.
The cell maker can use the material the same way they use graphite. They don’t need to retool anything in the cell manufacturing process. Then it is easy for them to make adjustments, whether it’s a 5% or 50% substitution of graphite in the anode.
The reality is, you are going to start seeing more and more partial substitutions of graphite. The next generation of batteries need to contain more silicon to enable fast charging and longer range. Using our material in just a 15% substitution blend with graphite will double the capacity of the anode.
You will also be able to bring the battery up to 50% charge in less than 10 minutes. We also have about 20 to 40% more energy density in the battery, which would enable 20-40% further range.
What we see is gas stations becoming charging stations, because you can get in and out as quickly as it takes to fill a tank with gas.
AI: What properties make silicon so suitable?
Zeitoun: Silicon – and not only our silicon – is so interesting because it theoretically has 10 times higher capacity than graphite. In a graphite anode lithium is intercalated into the spaces between the layer structure, whereas a silicon anode combines with lithium through intermetallic alloying.
This gives silicon the potential to store 10 times more lithium than graphite for a 40% increase in the energy density of the cell. So, that is why silicon is so interesting, and why there has been so much development in it.
AI: Is this the battery technology breakthrough the industry has been working so hard to achieve?
Zeitoun: Well, I think we have huge potential to revolutionize the battery industry. It is not just our technology. Silicon can really revolutionize battery performance and design. I don’t think there’s any dispute about that, really, but where we come in is we have developed what we believe is the most efficient and scalable solution with the potential to produce enough to meet the needs of the market.
Because we are vertically integrated and have significant volumes of the feedstock, we will be the first to market. At 2,000 metric tons we will be the first mass producer of nano-silicon, at least in the United States. It will only take a year to
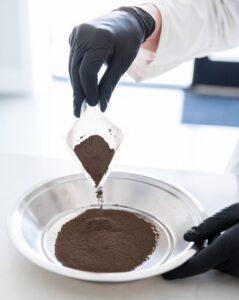
a year and a half for us to scale up from 2,000 tons to 30,000 tons.
We have the infrastructure in place to do that. We’re taking a stepped approach by making the amount of material that can actually make a difference to an EV manufacturer in the near term.
AI: What about sustainability – how are you managing the energy used to produce Ionisil?
Zeitoun: Our process is low energy. Because we are not synthesizing a nanotube, we have a process that enables us to manufacture at around half the temperature of other silicon. We are running at around 700 degrees Celsius.
We are currently in the process of doing an independent life cycle analysis. Then we will have more exact figures, but from our estimates, we are confident that we have the lowest carbon emission per ton of silicon material production.
AI: What is next for Ionic MT?
Zeitoun: By the end of this year, we will have moved into our new production facility and are working towards our first 2,000 metric tons of product, and we are in discussions with various end users. At the same time, we are trying to optimize and improve every single day. Hopefully, what’s next is seeing vehicles with our material in them fast charging at gas stations. That’s our goal, and we will get there one step at a time.
More Stories
IMPACT LAUNCHED EUROPE’S MOST ADVANCED BATTERY PRODUCTION
Accelerating Precision: The Role of Servo Motors and Drives in Modern Automotive Manufacturing
Getac on AI’s transformative impact on automotive production and aftersales