
Trinseo supports the requirements of an ever-evolving automotive and mobility marketplace with innovative rigid and soft-touch plastics for interior and exterior applications.
Replacing internal combustion power plants with electric or hydrogen alternatives is just one step in the decarbonization of the automotive industry.
Increasingly stringent CO2 targets forcing OEMs and Tier suppliers to look beyond the emissions of the vehicle but focus on the full value chain – from raw materials through to disposal at end-of-life. Recycling is essential if targets are to be met. Automotive manufacturers need to integrate the concepts of lifecycle and value chains into their decarbonization strategies.
Specialty material solutions provider Trinseo is supporting the motor industry decarbonization drive in a variety of ways, including developing plastic materials to replace metals, using recycled and -based feedstock, and developing solutions for closed loop recycling and circularity of manufacturing.
Automotive Industries (AI) asked Frank Schumann, Trinseo Global Marketing Manager & Manager Business Development Europe, how the company is approaching decarbonization of the auto industry.
Schumann: Firstly, we are supplying materials with recycled content. That is the first go-to option for the industry. But, we are closing the gaps in the supply of raw inputs with bio-based materials as a complementary offering. It is really not one or the other.
We are also working on the next generation of technological developments that will close the gaps in raw materials and recycling.
AI: What contributes to the total carbon footprint of a vehicle?
Schumann: Quite simply, with an electric car your tailpipe emission is exactly zero. That means you have to look at the production processes to further reduce the greenhouse gas emissions of the car. Therefore, the natural focus of the industry is on reducing the amount of CO2 it takes to produce a car. It needs to be quantified and then reduced.
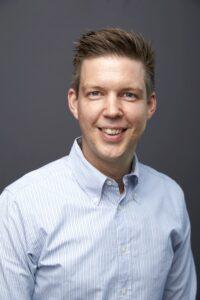
AI: How is Trinseo helping the automotive industry achieve this?
Schumann: Using recycled content is currently the primary decarbonization method. Nevertheless, lightweighting remains important, because every kilogram saved is a win, as it improves fuel economy or battery range, and we already introduced solutions for lightweighting.
And then last but not least, we are looking into how we can close the circularity loop. The focus is on what can be done with end-of-life cars. Are we able to recycle them back into automotive grade quality inputs?
AI: What are the practical obstacles?
Schumann: The biggest challenge is the availability of feedstock for recycling. There is a big concern that there will not be enough feedstock even if all the OEMs meet the recycling targets that they have announced. So that is really the biggest practical obstacle which we are trying to mitigate.
AI: How important is it to integrate the concepts of lifecycle and value chain into your strategy?
Schumann: The value chain is very much dictated by the standards given by OEMs. And the OEMs are trying to comply the standards set by government regulations. So, this is a kind of a top-down approach. Some OEMs are more advanced than others in meeting the new standards and are factoring in the ecological impact of their operations in addition to a material mechanical performance. Their decisions are also informed by the cost point of their options.
AI: Where do you see the next challenges for the automotive industry?
Schumann: This will very much depend on the next set of regulations which come into play, because they set the standards. We believe there will be a greater emphasis on the recycling of plastics throughout the automotive value chain. Solutions will need to be found to secure material streams from end-of-life vehicles. But, the focus will mainly be driven by regulation.
AI: And what do you think will be the biggest hurdles?
Schumann: The availability of volumes of material for recycling. It could be a mix of recycled materials and biomass. But, if you are to move away from fossil-based plastics, the volumes of recycled plastics and biomass materials will need to be much higher than they are today.
In addition, the use of end-of-life vehicle plastics will require a much more sophisticated understanding of what these plastics are in the car. We suppliers are not able to use completely mixed waste.
We need to separate. We need to have a high purity in order to fulfil our automotive requirements.
AI: Are there any qualitative and quantitative tools that could enable sustainability tracing across the chain?
Schumann: In first place, we are talking primarily about CO2 emissions, so that nails it down to something that we call ‘product carbon footprint’ for each of the plastic products that we sell. And we have begun implementing quantifying tools. We have started using At
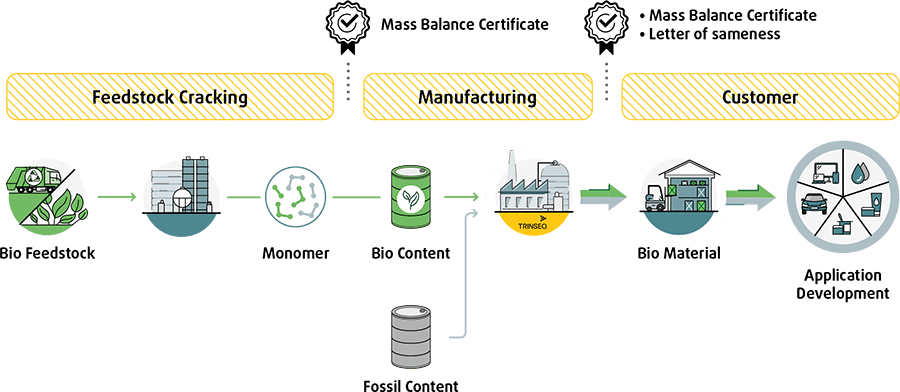
os’ solution, enabling us to provide customers with trend data, not only for sustainable materials, but for the entire portfolio of materials we provide to them.
So, they are able to start comparing them and understand the benefits of the recycling or sustainable options they have. The tool helps them to quantify the product carbon footprint throughout their portfolio of components.
We are also looking at utilizing different data and material handling systems such as blockchain technology in order to follow the plastic component from the production of the raw material through the 15-year lifespan of a vehicle and then the recycling of the materials.
Our objective is to provide the tools which will allow OEMs to make more informed decisions about the materials they select in order to reduce their carbon footprint through recycling. The tolls will provide them with greater insight into the materials they and their Tier suppliers are using.
AI: What is next for Trinseo?
Schumann: Progress never stops. Sustainability is much more than just a trend right now. It is the dominating factor influencing the design of vehicles and selection of materials for the drivetrains and components. As a company, our focus is on growing volumes of sustainable plastics. For us that means identifying opportunities for advanced recycling technologies beyond mechanical recycling. We are working on chemical recycling, and other solutions which will help OEMs and Tiers to meet the targets set by the regulators.
More Stories
Automotive Industries (AI) Newsletter April 2025
Marelli focuses on Software-Defined Vehicle evolution at Auto Shanghai 2025, introducing the new ProZone zone control unit
Will Cars Function Like Smartwatches in the Future?