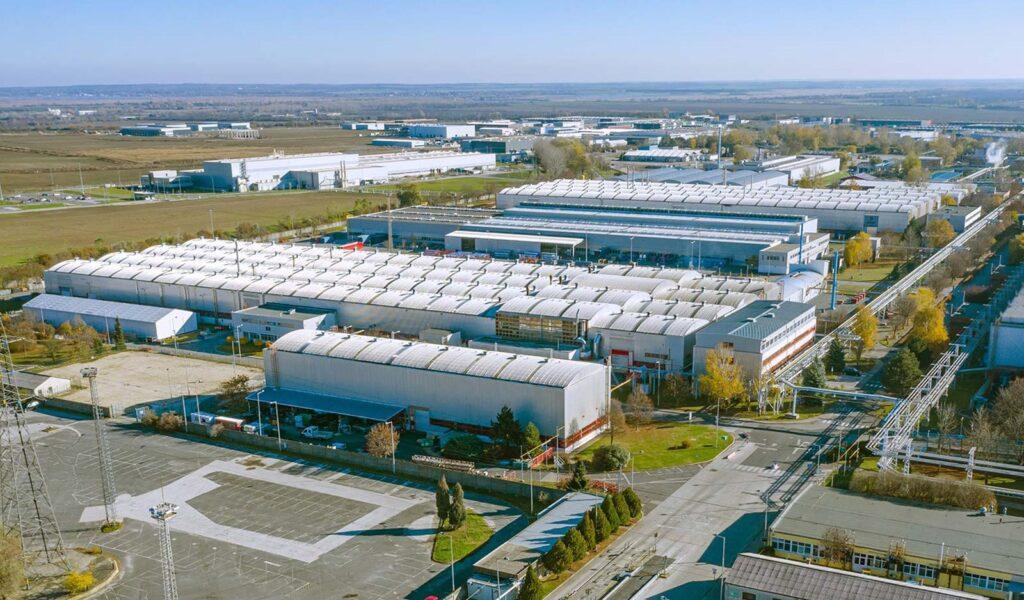
Consumer opinion is driving demand for aluminum in automotive applications.
It gained momentum early in the Covid-19 pandemic. A March 2020 study by Kearney found that 48% of consumers were more concerned about the environment due to Covid, while 55% reported that their pandemic experience had made them more likely to purchase eco-friendly products. These findings were supported by the Kantar “Who Cares, Who Does?” 2020 report, which found that 59% of global consumers considered themselves to be eco-active.
Kantar’s consumer trends tracker Global MONITOR shows that people blame business for society’s environmental challenges: 79% of people globally hold large corporates responsible.
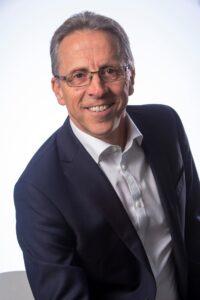
Automotive Industries (AI) spoke to Paul Warton, Executive Vice President and Head of Hydro Extrusions, and Piotr Chmielewski, VP Automotive for the Extrusion Europe business unit.
AI: Is this sentiment being translated into greater demand?
Chmielewski: Aluminum is gaining market share against other materials.
Hydro provides components such as crash management systems, roll-over bar protection systems, structural parts, and side sills. We also supply high and low voltage electrical cables for electric vehicles.
The demand is there despite high inflation, increased energy costs and conflict around the globe. Manufacturers have full order books. They can sell more than they can make at the moment. In addition, there’s many new models coming off the drawing boards which have a growing percentage of aluminum components.
The focus now is on sustainability, with the automotive sector driving the charge to reach carbon neutrality by 2050. There are OEMs which are targeting 2030 for bringing emissions down to zero.
This creates upstream and downstream challenges for the industry. We need financing to execute on the conversion technology required to do this.
AI: What is the role of aluminum extrusions in this?
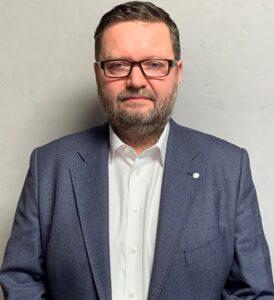
Warton: There is a continuous lightweighting trend now in combination with sustainability such as reducing CO2 emissions and increasing use of recycled materials. When it comes to lowering the overall CO2 emissions along the total value chain, I think Hydro is in a strong position to assist OEMs to meet their sustainability goals because we have control over the full value chain.
AI: What about electric cars?
Warton: There are two answers to the question. The first is about reducing weight and the second safety. Aluminum is being used to extend the range of electric vehicles by making them lighter. We are working very closely with customers on their new platforms in what we like to call partnerships. They see aluminum as the master material which is helping them to reduce weight, and us as the partner able to help them with design and other solutions.
OEMs are now looking beyond product performance, lightweighting and cost competitiveness. The focus has shifted to emissions during the vehicle’s use phase and end of life recycling. It is estimated that there is 1.2 million tons of aluminum scrap leaving Europe annually. This is not processed in Europe because it is contaminated, so the cost is too high and the necessary sorting technology is not in place. It is excluded from the value stream.
We are working on designs with the OEMs to ensure that at the end of life we have a component that is cheap to disassemble, to return and to recycle. Much more emphasis is being put on end-of-life recycling during the design stage.
With aluminum, only 5% of the energy is required to produce a recycled aluminum part compared to that needed for one from virgin material. This is significant, not only because of the cost of
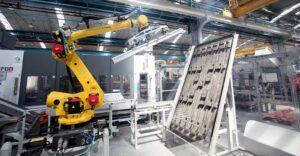
energy, but also the contribution to sustainability. The power can be supplied by renewables, which is the route to zero carbon. So, we to develop the competence to process the contaminated scrap.
A good example is Hydro’s recycling division, where we’re doing much more sophisticated shredding and are able to sort lower-grade scrap, and contaminated scrap. We are using this material to produce primary and secondary foundry alloys and value-added products like extrusions.
AI: Is aluminum safer than metal components?
Warton: Categorically, yes. Because the OEMs come to us with a performance specification of what that bumper system needs to do on the different crash scenarios. The amount of testing they do on crash management systems now is unbelievable. And they absolutely love the energy absorption capability of the aluminum crush cans, as well as the beams. They get superior safety performance while reducing weight.
AI: How does Hydro help automotive designers reach their carbon emissions targets?
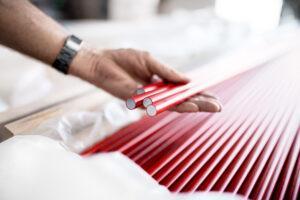
Chmielewski: We provide design solutions to meet specifications. Some customers are specifying a minimum scrap percentage. One of the biggest challenges with producing low-carbon aluminum is a shortage of scrap. Hydro is able to reduce the CO2 emissions produced throughout the aluminum production value chain through our own direct and indirect emission controls within our plants. We are therefore on track to reduce our own emissions by 10% by 2025 and 30% by 2030 from a 2018 baseline. We are committed to net-zero emissions by 2050 or earlier. Combine this with superior performance compared to other materials, and we have a strong package of sustainability, performance and cost competitiveness for the OEMs.
AI: What is the importance of transparency about content and carbon footprint?
Chmielewski: It’s all about traceability, transparency, and certification. We work with a number of bodies to certify our materials. Controlling the entire aluminum value chain, from mine to aluminum components, helped us obtain Aluminum Stewardship Initiative (ASI) certification. The ASI certification is given to companies that have a demonstrated commitment to social, environmental and ethical standards. Full traceability audited by external certification bodies and our
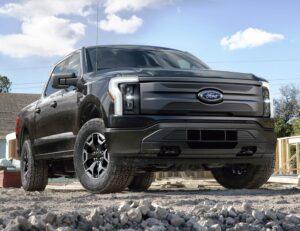
customers ensures we can guarantee the solutions we offer are low carbon.
AI: What’s next for Hydro Extrusions?
Warton: We have to invest in capacity and to reduce our carbon footprint. In the last 12 months we signed off 4 billion NOK (US$426 million) in capex, which is almost double our historic rate of capital expenditure. This will see expansion of manufacturing and recycling capacity on three continents. A fair proportion of that investment is for the automotive sector.
Hydro has demonstrated that we are committed to investing in automotive, with sustainability a top priority. What we take as read is being 100% on time, having an ingrained zero-defect mentality and being fast and responsive to very demanding customer base.
Our operations will also have to become more automated in order to provide more advanced solutions and products to the automotive industry. We are gaining momentum to reach a super high level of automation, which is the global standard in manufacturing. Through automation we will be able to align and standardize our operations between the United States, Europe and China.
More Stories
Automating ECU testing for automotive transfer cases using HIL
New LLC Switcher IC From Power Integrations Delivers 1650 W of Continuous Output Power
LTE IoT 10 Click Click board from MIKROE provides reliable IoT connectivity