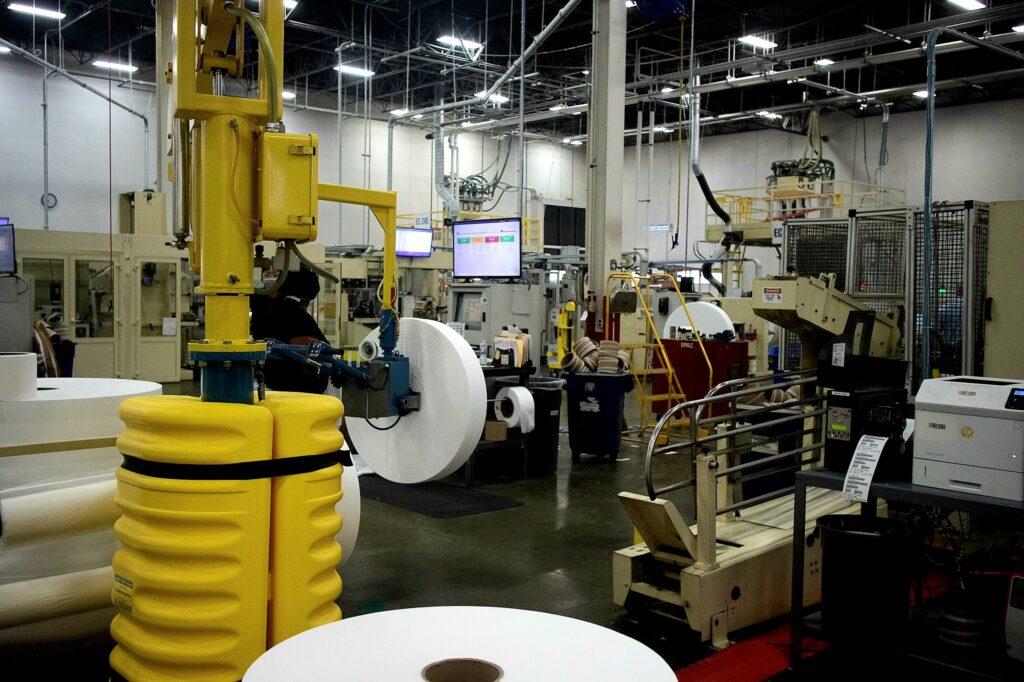
Throughout 2020, ecommerce continued to grow past unprecedented numbers as consumers ordered goods from the safety of their homes. Even now, retail sales are expected to increase 7% to 9% through the end of 2021 and beyond. During the holiday season supply chain disruptions are inevitable as labor shortages and capacity restraints limit fulfillment speed. For mid-sized manufacturers, real-time visibility and insights are crucial to compete in today’s environment, especially when it comes to overall customer satisfaction. Leading mid-sized manufacturers believe that investing in Industry 4.0 will build resiliency in a future full of unknown disruptions. Since the second quarter of 2020, business investment in equipment has grown at 26%, more than twice as fast as the overall economy.
Updated sensor technology can unleash previously unavailable factory floor data, challenging mid-sized manufacturers to find innovative ways to transform it into usable information. Analyzing different, individual silos of data can be tedious and overly time-consuming for operators and management. Industry 4.0 breaks down data silos by leveraging data from various sources across the factory into tools like a real-time data platform, analytics, and artificial intelligence. The integration of real-time data into one centralized platform is the future, and this future is worth the investment.
Data Management Challenges
Even with siloed data, mid-sized manufacturers have been utilizing machine data to the best of their abilities to improve operations. However, with a growing labor shortage and increased customer demand, manufacturers are being forced to reduce time consuming tasks to increase efficiency. All-in-one centralized platforms with real-time data will reduce the time needed for manual analysis between different data silos. To overcome the challenges associated with data integration, mid-sized manufacturers must automate tasks like:
• Manual Data Collection: Collecting data manually is time consuming, tedious and has the potential for human error. Real-time insights are nearly impossible to receive with manual data collection and operators could be performing other tasks to provide greater benefit to the factory floor. This would help streamline manufacturing workflow from initial inquiry to final delivery.
• Data Accessibility: Many mid-sized manufacturers use outdated methods, like Microsoft Excel or physical notebooks, to record factory floor data since that is how it has always been done. Not embracing new ideas can cripple operations and recording data in these limited spaces means that the data is only available to a small number of individuals. By installing sensors on existing machinery, real-time data can be pulled into an integrated platform that not only will help improve efficiencies, but also track Key Performance Indicators (KPI).
• Data Silos: Data should not be independently stored without accessibility across internal departments. Operators and staff need access to data from all parts of the factory to determine where bottlenecks are occurring, and guidance on how to correct them and prevent future reoccurrences.
How To Move Away from Data Silos
Individualized data storage significantly limits communication and operational efficiency on the factory floor. Incorporating smart factory solutions like sensors to increase visibility across departments is simple but knowing how to use the information captured can be daunting. especially with the urgency of smooth production. However, data integration is crucial to consolidate all relevant silos into a single, digestible and user-friendly dashboard for operators. Along with consolidation, manufacturers must structure the relevant data so it can be fed into tools for analysis and presentation to improve operations. With mid-sized manufacturers using outdated systems that operate independently, Industry 4.0 can bring operations to the next level while sinking data islands of automation to make a more cohesive operation. Even after just a few hours, data is already outdated, and manufacturers can get stuck in a constant loop of playing catch up.
Industry 4.0: Innovation at its Finest
With Industry 4.0 mid-sized manufacturers can utilize smart sensors to capture real-time data on existing machinery to create actionable data. Manufacturers should avoid industry solutions that do not place importance on increasing communication and data fluidity on the operations floor. By reducing siloed data on the production floor with Industry 4.0, manufacturers can see benefits such as:
• Increased Data Accuracy with Real-Time Data
• Reduced Lead Times and Bottlenecks
• Less Wasted Time with Manual Data Capture from Operators
• Improvement of Overall Equipment Effectiveness (OEE)
Reducing data silos creates a more collaborative work environment among operators. However, to encourage this collaboration manufacturers should formulate a comprehensive data integration plan that will give operators a clear path for how to react to certain data patterns. With an Industry 4.0 solution that brings data unification in a single dashboard, operators can easily see smart analytic trends from data around the manufacturing plant.
Historically, some manufacturers strategically placed color-changing stickers to indicate when machines were overheating, with the expectation that operators would turn off the machine. The data from smart sensors on machinery can be much more cost-effective by letting manufacturers notice trends that are causing machines to overheat. Real-time visibility not only lets manufacturers know if there are problems with equipment, but it is a proactive measure for the current supply chain where wasted time can greatly affect customer satisfaction.
Internal Preparations
Data integration may seem overwhelming but with modern tools that bring Artificial Intelligence and Machine Learning, manufacturers can easily reduce data silos to improve operations. With fewer data silos mid-sized manufacturers can greatly increase their factory floor agility in the face of unexpected disruptions. During implementation, all stakeholders should be involved, from factory floor workers to key operators. Success on the factory floor comes from all involved individuals and without data silos, information can flow freely. Industry 4.0 operations can provide immeasurable success while empowering employees with more data from the factory floor.
About the Author: As President of FactoryEye by Magic Software Enterprises, Terri Ghio is responsible for the development and implementation of FactoryEye’s overall corporate strategy, business development and strategic partnerships. Ghio has been an invaluable resource in expanding on Magic’s global success and building Magic’s Industry 4.0 solution for mid-sized manufacturers, FactoryEye.
More Stories
Accelerating The Development of Hydrogen Vehicles & Infrastructure – Europe’s Biggest Players Meeting at Premier Event
Automotive IQ Announces the 15th Annual Automotive Functional Safety Week 2025
Major Automotive Companies to Share Latest Developments in Steering, Braking, Chassis and Suspension Systems at Premier Industry Event