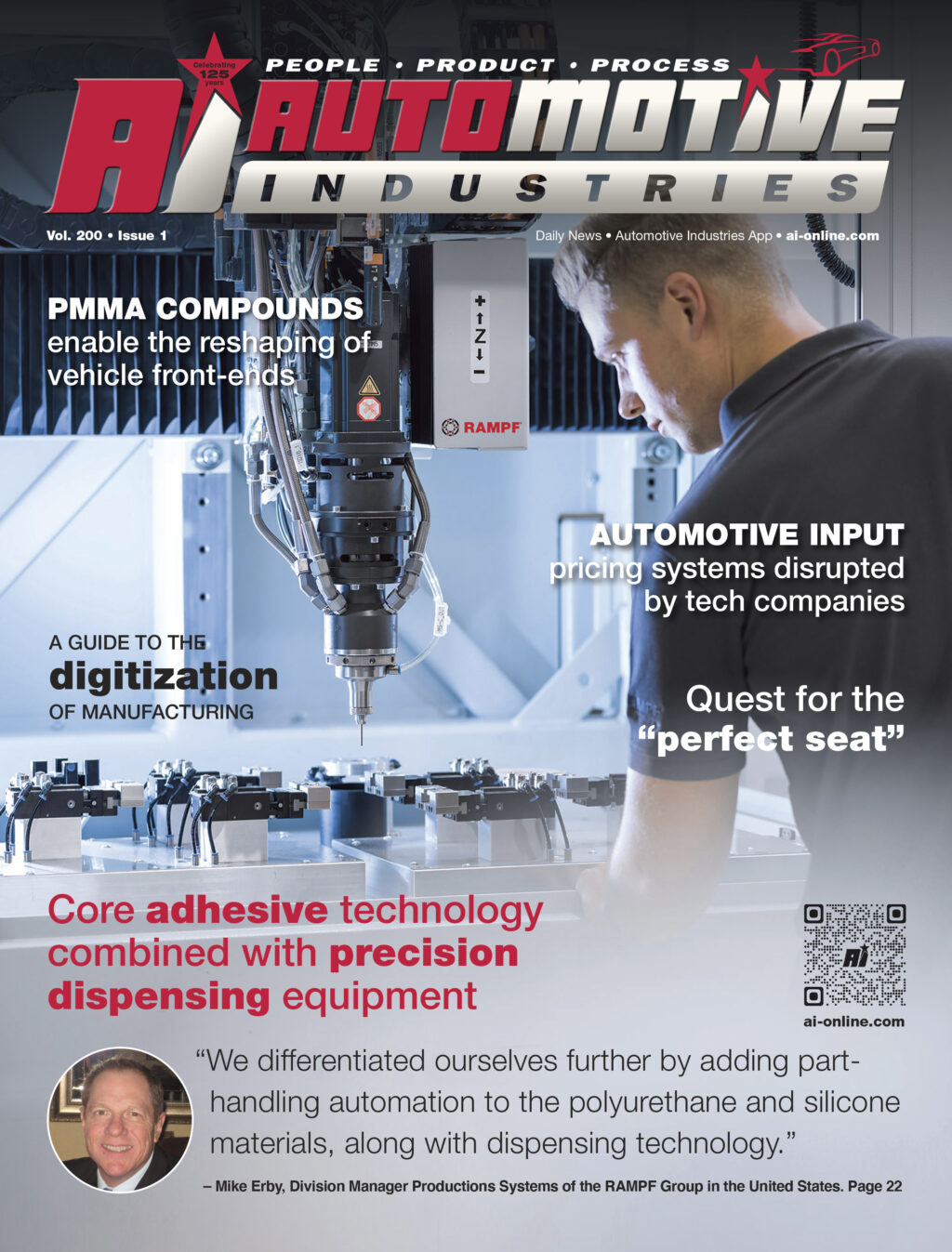
In the pursuit to reduce vehicle weight, OEMs created a mix of structural materials in vehicles. One- and two-component adhesives bond fascias, bumpers, spoilers, tailgates, side moldings, roof assemblies and other combinations of plastic, glass and metal components.
As a leading developer and manufacturer of polyurethane, epoxy, and silicone reactive resin systems, the RAMPF Group’s product portfolio includes liquid and thixotropic sealing systems, electrocasting resins with high thermal conductivity, elastomers, and adhesive systems. RAMPF combines core technology with precision dispensing equipment and automation solutions for complete sealing and bonding application systems for production lines.
Automotive Industries (AI) asked Mike Erby, Division Manager Productions Systems of the RAMPF Group in the United States, what led to the group deciding to expand into application systems.
Erby: It was a natural extension of our expertise in reactive resin technology. The original RAMPF lab in
Grafenberg, Germany, used dispensing machines for resin testing and part trials. RAMPF is unique in that we offer our materials and dispensing equipment from the same company. Combining two technologies made sense. We differentiated ourselves further by adding part-handling automation to the polyurethane and silicone materials, along with dispensing technology. Now, RAMPF routinely builds automated dispensing work cells with all three technologies combined to form a single solution.
AI: Can application equipment be used with compounds that you do not supply?
Erby: Yes, often Tier 1 or Tier 2 suppliers have their own preferred materials developed for their specific application and OEM. RAMPF works with customers to develop the necessary production application systems using technical material data such as specific gravity, density, filler content, types, etc.
AI: What are the design trends that have influenced the direction RAMPF is taking?
Erby: The process of light weighting creates new bonded assemblies. New materials, such as plastic fascia are bonded to structural components. In addition to plastics reinforced with carbon fiber and fiberglass, the assemblies of different substrates, such as glass to steel, plastic to steel and glass to plastic are combined. RAMPF systems deliver the right adhesive and bonding techniques, as well as curing methods that allow the parts to bond while maintaining the proper tolerances. The challenge is to have the right adhesives and processes to form the bonds. To do so, one has to speed up cycle times.
The adhesives have to cure in seconds rather than hours. Cure-on-demand technology (CoD) uses regulated infrared emitters that heat up the adhesive from the inside to the outside, making the bond strong enough for the components to be removed from the tool without affecting the quality of the bond. Sensors that record the surface temperature of the components supply the data for an exact process control of the radiation intensity.
AI: Are there any additional challenges with electric vehicles?
Erby: One main challenge with electric vehicles is shorter production runs. OEMs and Tiers require more flexible work cells capable of producing a variety of parts / model series, with rapid changeovers. RAMPF equipment has interchangeable tooling and programmable robots that speed up part-to-part changeover.
AI: What about electronic components?
Erby: All electronic components are being miniaturized. This means that the sealing of components must be incredibly precise. RAMPF offers systems that apply a two-component polymer in 0.2-gram dots. This means that each metering pump can accurately dispense 0.1 grams. This process maintains statistical quality requirements as part of the machine specification. At that size, one of the challenges is to place the dot at exactly the same place on every board at production speed and volume. The miniaturization and consolidation of electronic components also concentrates the heat within these systems. In other words, there is an urgent need to remove the heat so that components remain reliable and durable. RAMPF equipment can accurately place tiny dots of thermal interface materials with speed and precision on these electrical components. Design trends are constantly evolving. There are more and more electronic components in cars. Besides others, RAMPF specializes in building assembly work cells for automotive displays, which are becoming larger, more complex and interactive. There is a growing demand for sealing electronic components that protects from moisture and dust, as well as vibration.
AI: And electric vehicles?
Erby: One of the key focus areas is applying thermal interface materials in the battery compartment, as part of the thermal management system. Many of the sensors throughout an electric vehicle need to be sealed against dust, moisture and vibration. RAMPF develops the polymers and designs / builds the application equipment needed for this very precise work. This solution fits with our background in automotive electronics. Building dispensing and assembly work cells for power transmission modules, power steering modules, ABS modules, and many others. Furthermore, RAMPF can offer materials and equipment to seal the battery housings with polyurethane, silicone foams, or elastomers.
AI: What about helping Tiers to fast-track development?
Erby: RAMPF has become an important link in the supply chain. We work with OEMs in the early conception and design stages to obtain pre-approval for RAMPF materials and applications. When a Tier company reaches out to an OEM, they are often fully prepared to meet the customer’s needs because the process has already been approved and has been used before. This helps the Tiers to secure the business because they are working with pre-approved materials with a history. They save costs and time in finding the right materials and obtaining approval for their use. We are also able to build customized solutions for production. RAMPF can provide the materials, dispensing equipment, and automation in a single package. We bundle our expertise, the equipment and the materials to provide a complete solution. You do not find many companies that can offer all three. By collaborating with RAMPF, the Tier is working with a single company that is responsible for the entire job.
AI: What is the design process?
Erby: It starts with detailed specifications, which include cycle times, part CAD data, material specifications, and a long documented project checklist. From there, the process then moves into the laboratory with testing and trials. The knowledge gained in the lab is carried through into the building of the machines. At machine acceptance, we are processing the customer’s parts using their intended materials sometimes with the entire supply chain in attendance. Our team then installs and commissions the equipment on the production line.
AI: What other applications are there?
Erby: The manufacturing of automotive and off-highway filters is a growing area. RAMPF works with many global suppliers making automotive filters, including oil and air intake filters. The focus is dedicated to parts-per-hour and part quality. A poorly produced filter could lead to engine damage, so we include quality systems that recognize process problems and stop the process if one of several monitored systems are out of tolerance. The idea of a single mixing head, single production line has long since passed. High-speed cap lines use multiple mixing heads to extract more output from their existing investment by increasing the speed of production. There are also exciting developments in the application and use of polyurethane foams. Both our RAKU® PUR polyurethane and RAKU® SIL silicone systems combine efficient sealing with the highest quality and exceptionally easy handling. They adhere to a wide range of housings – stainless steel, aluminum, powder coatings, plastic, glass, etc. – and cover a temperature range from -40°C to +90°C and even up to +130°C for short periods. They are designed to provide a very short tack-free time, which facilitates fast assembling processes, low air loading and low viscosity. RAMPF will continue evolving with electric vehicles as technology continues to advance.
More Stories
CGD DEMONSTRATES SUPERIORITY OF ICeGaN IN MOTOR DRIVES, DATA CENTRES AND EVS AT PCIM 2025
Danisense exhibits at PCIM Expo 2025 in Nuremberg, Germany, May 6 – 8
Bridging the Gap Between Performance and Practicality