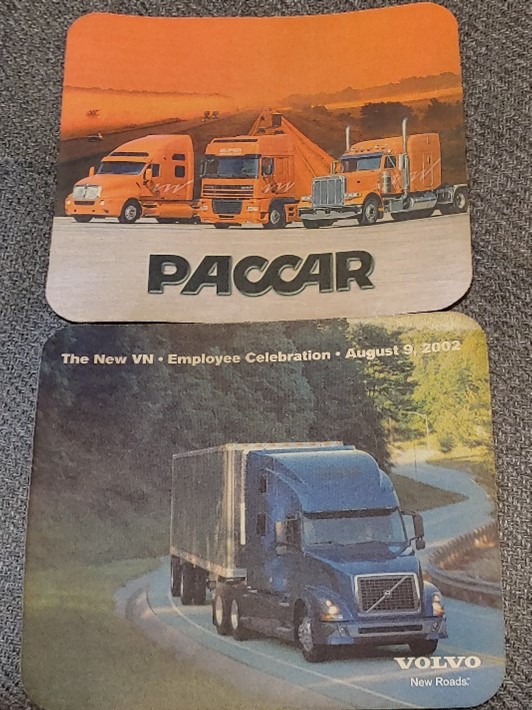
It is funny how being close to something, we miss the myriad of small things or the results of a series of small actions.
Actions we take to learn and grow competence; and accrete skills and knowledge (which is a geeky way of saying accumulate).
It is also funny how the longer you are in an industry, the smaller the world seems. I have recently had serendipitous connections and exchanges on product testing in the automotive industry, so it seemed like a good time to write a bit out product testing over time.
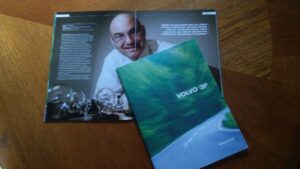
I have been in product development and manufacturing for vehicles for more than three decades, in a variety of capacities, including significant stints in test and verification.
An article in the January/February 2021 issue of SAE Automotive Engineering magazine, Allison Builds a Testing Powerhouse, prompted me to reflect on the milestones and present state of testing. Many OEMs (Original Equipment Manufacturers) have invested considerable time and dollars in developing their product testing capabilities.
As a product grows in complexity, so too will the way we should test.
It was not so long ago, at least I can recall it when most engines were largely mechanical and had little or no embedded (software) components.
Today it is not just the engine, but the entire vehicle which has embedded electronic systems distributed throughout that interact using a variety of serial data bus communication.
Experience
I have worked at two OEMs, both of which had specialized testing facilities. I enjoyed my time at both and watched the respective testing capabilities grow.
This includes specialized track development, engine test cells, complete vehicle thermal chambers, dynamometers, and other equipment. That other equipment was in response to the electrification and increase in software functions on the vehicle.
To go along with that specialized equipment, and more importantly, talent acquired and developed. Talent comes first, otherwise, how do we know what tools will be required and how to implement the tools.
One of the OEM facilities at which I worked was the PACCAR Technical Center (PTC), mentioned in the article. The facility, located in the Skagit Valley, comes alive with pops of color in the spring with the Skagit Valley Tulip Festival.
I would not want to speculate how many rolls of film and how much time I spent taking pictures of these fields and the wide variety of tulips, c
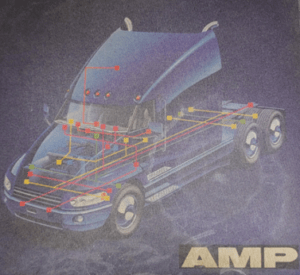
olors, and backgrounds.
The dynamics of the weather meant no two shots would look alike. I would take my dad’s 35mm Nikon FG, with wide-angle, telephoto, and macro-lenses into the field.
Not one bit a waste of time. I will one day recount how I ended up working there. For now, let’s explore the capabilities of these types of test facilities and how this must grow as we learn and vehicles become more complex.
Keep in mind this was the 90’s when I was at PTC. Heavy vehicles have an abundance of wire harnesses carrying substantial current.
Think about four batteries of roughly 800 CCA (cold cranking amps) for each battery (3200 CCA), that provide energy to the vehicle and must be controlled.
Multiplexing is distributing feature content among a range of electronic control units (ECUs). Long wire leads carry communications and buss power throughout the vehicle.
Multiplexing reduces some of this wire content (weight reduction and logistics in manufacturing) but does not eliminate it.
In the past, we tested the cab electrical system (using thermal imaging). We started with a plexiglass version of a generic vehicle that represented the
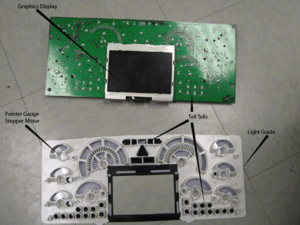
external parts of the vehicle. It looked nothing like a vehicle, but boxy and approximated a scaled version of the cab.
This ease of visibility makes it possible to use a thermal camera to view the wire harness placed within this cabin as it would be in the actual vehicle.
Then various failure modes are evoked, for example, heavy current-carrying wires are shorted, initiating a failure and the thermal camera captures the event. The expectation is that the system controls will prevent serious damage.
As this virtual cab has no plastic or cloth material, it is not prone to spontaneous events which we must recognize but shall not name. I will give a hint; it starts with F and rhymes with ire.
The thermal camera monitors the heat generated looking for hot spots that may lead to field problems. Areas noted that do not perform as expected, generate high heat, for further exploration such as design changes to remediate well before we launch the product.
This is but one of the tests demonstrated at the PTC open house during the Tulip Festival. Another one of my favorites was the airbag test. Nothing like watching that event, without being in a crash or otherwise physically impacted by the event.
At one time, the vehicle instrumentation was a collection of individual gauges and discrete illuminations often referred to as tell-tales. Tell-tales provide quick feedback on the system status (washer fluid low, traction control event etc.)
Each gauge in a separate can often mounted attached to a metal plate with precut circles for individual gauge mounting.
Very old, indeed, I caught the tail end of this at a heavy truck company. For example, a tachometer, the engine speed gauge, would be an individual pointer gauge, and driven by a cable which spins in proportion to the engine RPM. That cable spinning translated into a pointer position.
The product has changed to a printed circuit board with stepper motors, large displays and a wire harness connecting the various inputs from sensors and other ECUs. To make this happen, requires sensors that provide signals rather than mechanical mechanisms.
Instrument cluster testing which was once manual can now be automated, and it must be automated. In some cases, the range of vehicle variation can be quite extensive. This is especially true with the addition of the graphical display.
Parameters in the product software are part of the design that makes it possible to adapt the display systems without changing the hardware, lowering manufacturing costs and improving product quality. This is especially valid for the large format displays and the telematics and infotainment systems of modern vehicles.
All of these require continuing development of the organization’s testing capability in terms of talent and tools. To perform testing of the product is done with inexpensive cameras and computing power to automate the testing.
This allows the testing to extend beyond the time the tester exercising the product. This is a good thing, as these displays can contain considerable content, adapting to specific vehicle feature content.
Functional Orientation
You may not notice the changes while you are doing the work, but they do. As complexity or variation of the product and systems increase, so too will the testing.
Additionally, other constraints, for examples, consider time to market, and customer desired variations, that will create pressure for the organization to change the way we work to accomplish the objectives. There is much more to testing than reviewed here, however, we must stop somewhere, this is not a book.
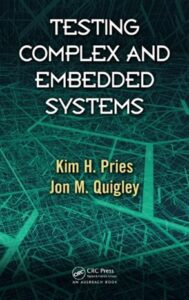
If you are interested in reading more on the topic of product testing, check out our book Testing of Complex and Embedded Systems.
We will need find ways to experiment and learn quicker in regard to the product and its use. We seek the ability to probe the product earlier and earlier in the development cycle.
We look to stress the product in ways that have not previously required. We test boundaries that were not testable before.
As the product grows, so too will the need to grow our testing competencies and capabilities. We can see the benefits on the shipped products to the customer. We can see the benefits in the examples of PTC and other OEMs.
Gathering competencies and creating an environment wherein the individuals can develop equipment and processes to adequately test the product has great benefit. This sets the foundation for continuous improvement via growth in test capabilities.
This in turn will have a positive impact on the quality of the developed product. This only becomes more necessary as, for a time, OEMs are straddling the line between internal combustion and batter or hybrid vehicles.
More Stories
Unique Vacation Experiences for the Car Enthusiast
Mecum Auctions Sponsors Monterey Motorsports Festival for Car Week
How to Set Up Your Garage with the Right Equipment for Auto Repairs