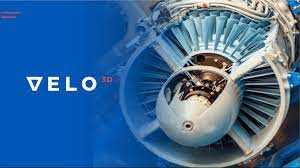
VELO3D Inc., a leader in advanced additive manufacturing (AM) for high-value metal parts, announced that Vertex Manufacturing, a Cincinnati-based business providing CNC machining and manufacturing services from development through production, has selected VELO3D to help meet growing demand for 3D-printed “impossible” metal parts.
Vertex was born out of the desire of AM pioneers Greg Morris, Steve Rengers and Tim Warden, previously of Morris Technologies, to leverage their advanced manufacturing and technology backgrounds to help companies solve some of their most difficult problems. Vertex is AS9100, ISO13485 and ITAR registered and certified.
“With unique technology providing the capability to create production parts that would be impractical or impossible using other methods, our new additive manufacturing solution from VELO3D means customers will have even more freedom to design and engineer some of the most complex geometries imaginable,” said Greg Morris, co-founder and CEO, Vertex Manufacturing. “This is the essence of why Steve, Tim and I started Vertex Manufacturing – to help customers leverage the most advanced manufacturing technologies and push the boundaries of what is possible.”
Where Morris Technologies primarily focused on prototyping use cases, Vertex was created with a mission to help customers who need advanced manufacturing solutions for both development and production programs. They offer a range of services including advanced multi-axis CNC machining, additive manufacturing, rapid castings and final inspection of manufactured parts.
“When I first founded VELO3D I was inspired by the Vertex team and tried to get them to work with us, but we were too early and had not proved our place in the market yet,” said Benny Buller, founder and CEO, VELO3D. “Their decision to work with us today speaks to the real and transformational capabilities VELO3D is bringing to the metal manufacturing industry.”
Vertex will take delivery of its first full-stack VELO3D Sapphire solution later this month, which will be set up to print metal parts in Inconel 718, a nickel-based superalloy known for its superb tensile strength when subjected to extreme pressure and heat. It will be installed alongside other advanced manufacturing systems such as a top-of-the-line Makino a61nx CNC machining center. Vertex said it plans to add additional VELO3D solutions in the future based on feedback from existing customers who value the quality, efficiency and productivity benefits.
“The intent is to have this first machine fully operational by the middle of July,” said Morris. “As we move forward, we want to leverage the knowledge and experience our team has in bringing products to market or taking them to production to bring a stronger focus on pursuing production programs, whether it’s traditional manufacturing, advanced metal AM, or a combination of both.”
In March, VELO3D announced plans to merge with JAWS Spitfire Acquisition Corporation (NYSE: SPFR) and become a public company. Earlier this year, VELO3D was named to Fast Company’s 2021 list of the world’s most innovative companies, among the top ranked in the manufacturing category for its profound impact on the 3D printing industry.
To learn more about how VELO3D empowers engineers and designers to imagine more and additively manufacture nearly anything, follow VELO3D on LinkedIn or visit velo3d.com
About Vertex
The pioneering spirit that drove Morris Technologies, Inc. to become the premier global supplier of additive metal printing services and capabilities is now fueling Vertex Manufacturing. Leveraging decades of experience with thousands of applications across the aerospace, medical, defense, oil & gas and consumer goods industries, Vertex is committed to delivering products and services that meet or exceed customers’ quality and schedule requirements, earning `trust and conducting all aspects of what we do, and how we do it, with the highest levels of integrity: https://www.vertexmfg.com
About VELO3D
VELO3D, one of Fast Company’s 2021 World’s Most Innovative Companies, empowers engineers and designers to imagine more and additively manufacture nearly anything with a fully-integrated patented solution of software, hardware, and process-control featuring FlowTM print preparation software, AssureTM quality assurance software and the Sapphire® family of laser powder bed 3D printers. VELO3D additive manufacturing solutions for 3D-printing high-value metal parts allow for previously impossible geometries, so businesses can make the mission-critical parts they need without compromise. Customers include some of the world’s most visionary companies, such as Aerojet Rocketdyne, Chromalloy, Honeywell, LAM Research and Raytheon Technologies.
More Stories
Baja SAE Carolina:
ROHM to Showcase Advanced Power Electronics at APEC 2025
ROHM Launches 650V GaN HEMT in a Compact, High-heat Dissipation TO-Leadless Package