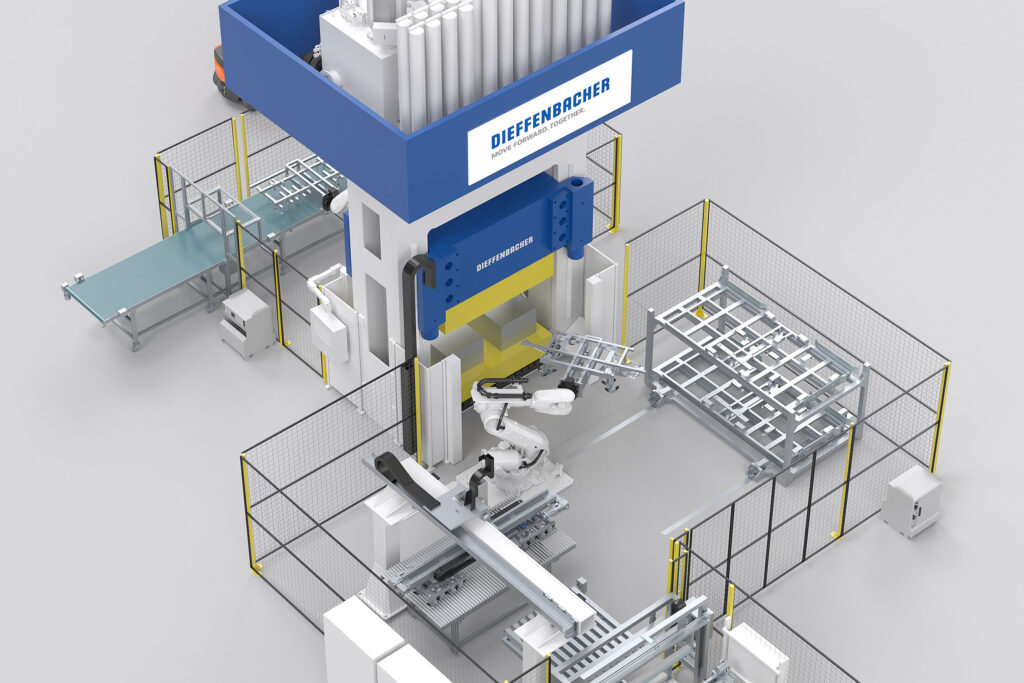
Parts suppliers for the automotive, logistics and construction industries
are increasingly turning to fully automated DIEFFENBACHER sheet molding
compound (SMC) lines to speed up production, reduce scrap costs and increase
output.
“Over the past three years, we’ve seen a huge uptick in the number of
companies inquiring about automating their SMC production lines,” said Marco
Hahn, Director Sales of DIEFFENBACHER’s Composites Business Unit. “This
reflects an increased desire to get away from manual processes and move
toward faster and more efficient automated processes.”
SMC processes are used by automotive parts suppliers to manufacture
composite components such as truck bumpers and car tailgates. For the
logistics and construction industries, SMC technology is used to manufacture
pallets, door modules, light wells, switch boxes and components for rail
vehicles. While the vast majority of SMC applications still rely on manual
processes, more companies are discovering that fully automated DIEFFENBACHER
SMC plants provide significant increases in productivity and plant
efficiency.
With manual operations or with ordinary cutting units, the time-consuming
change of SMC input material causes constant production interruptions. In
contrast, the DIEFFENBACHER quick-change system reduces changeover times to
a minimum by allowing the material to be changed parallel to ongoing
operation. Prepared outside the production cell, the quick-change device
with the new SMC batch is moved into the plant cutting system at the push of
a button and automatically inserted as soon as the previous batch has been
used.
“With conventional cutting systems, a change of SMC input material takes
about 10 minutes. The DIEFFENBACHER quick-change system saves you about six
to seven minutes each time you change the SMC batch,” explained Hahn. “If
you extrapolate this to a day, a week, a month or a year, you will save a
significant amount of time using automated DIEFFENBACHER technology.”
While the manual cutting and stacking process is error-prone and
time-consuming, DIEFFENBACHER SMC lines are equipped with automated cutting
peripherals that communicate automatically with a stacking portal, enabling
several complex lay-up profiles with different cutting patterns to be
produced simultaneously. Active-compensation cutting automatically corrects
deviations in stack weight. Weight tolerances in the semi-finished product
are reliably met. This ensures maximum reproducibility even with the
geometric complexity of the SMC layer structure.
Automation offers other benefits. Material residues and rejects from SMC
production pollute the environment, and their disposal as hazardous waste is
complicated and expensive. With flexible cutting geometries that make
optimum use of the input material and minimize waste, intelligent
DIEFFENBACHER SMC cutting technology protects the environment and reduces
disposal costs.
“Compared to manual processes, fully automated DIEFFENBACHER SMC plants
enable shorter cycle times and consistently high component quality. This
results in considerable increases in productivity and significantly improved
plant efficiency,” said Hahn.
More Stories
Accelerating The Development of Hydrogen Vehicles & Infrastructure – Europe’s Biggest Players Meeting at Premier Event
Automotive IQ Announces the 15th Annual Automotive Functional Safety Week 2025
Major Automotive Companies to Share Latest Developments in Steering, Braking, Chassis and Suspension Systems at Premier Industry Event