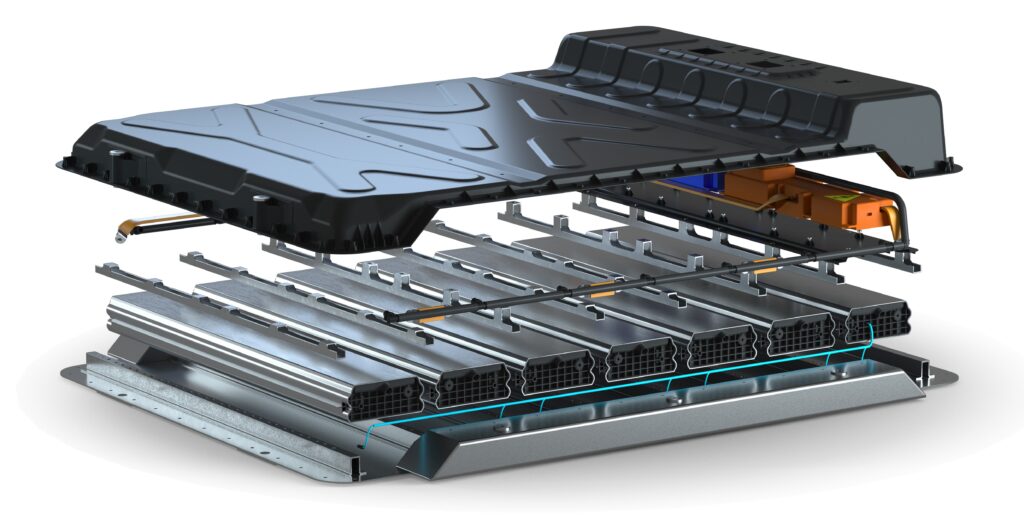
Although millions of electric cars and plug-in hybrids from many manufacturers are already on the road, there are still no generally recognized standards for the individual components in terms of service life or materials used. Moreover, the vehicles themselves are under rapid development. Currently, much attention is being paid to increasing the range of electric cars. This can be achieved by improving battery storage capacity and through efficient energy recovery. A second approach is to reduce the weight of the individual components, in order to reduce the energy needed to overcome driving resistance (tire rolling, inclination, and acceleration). The effect of weight reduction on the efficiency of the drive depends on the propulsion strategy of the electric vehicle. A consortium consisting of Lorenz Kunststofftechnik, Forward Engineering, Evonik, LION Smart, Vestaro, and Minth has developed a promising and effective solution to help improve efficiency through lightweight construction. In late 2019, work started on a brand-independent, low-cost battery housing solution in different sizes for electric vehicles. The result of the cooperation was a significant weight reduction of the battery by about 10 percent over other commonly used material combinations, without sacrificing any mechanical properties. In addition, the glass fiber-reinforced epoxy SMC – purpose-developed for the battery housing – meets all fire resistance requirements and is easy to work, even with complex geometries. The entire concept has been tested and shown to be suitable for series production and is safe even under extreme conditions.
Compared to the long developmental history of the internal combustion engine, e-mobility is still a very young technology. Nevertheless, many manufacturers around the world are launching a wide variety of vehicles onto the market. These vehicles differ greatly, not only in design and equipment, but also in construction and technology. This has led to a wide range of materials and component designs. But there are efforts to standardize individual assemblies of vehicles and develop a cross-market component standard. “Under the leadership of VESTARO GmbH, in 2019 we joined a cooperation with Forward Engineering, Evonik, and LION Smart, with the goal of developing a series-suitable battery concept for BEV models,” reports Peter Ooms, COO of Lorenz Kunststofftechnik GmbH. “Our main focus was the formulation for a glass fiber-reinforced epoxy SMC that meets all requirements for safety and workability and can also be returned to the material cycle.” In 2021, Minth GmbH, the European headquarters of the Chinese automotive supplier Minth Group, also joined the consortium.
Development of a new glass fiber-reinforced epoxy SMC
Components used in lightweight construction for hybrid and electric vehicles, such as battery housings, must not only be low in weight, but also exhibit high rigidity and strength. Carbon fiber-reinforced SMC materials can be used for this purpose, but they are very expensive and typically non-recyclable. Beyond that, there were few available materials with the necessary attributes, as they were either too heavy or had insufficient mechanical strength. “For the battery housing, we used Evonik’s VESTALITE®S epoxy hardener to develop a new SMC with a density between 1.5 and 1.7 g/cm³,” explains Ooms. “It has outstanding properties, like a bending strength of > 350 MPa, a flexural modulus of elasticity of > 18,500 MPa, and an impact resistance of > 150 kJ/m2.” By using an epoxy resin instead of the usual polyester resin, it was possible to eliminate other problems that normally arise in working with glass fiber-reinforced SMC materials. “With VESTALITE®S Epoxy Lorenz SMC, the molding material can be worked into complex geometries without adhering to the mold,” notes Ooms. The formulation has better mechanical properties than conventional SMC materials and features a very good fiber course in the molding process. Moreover, Lorenz has an established process for recycling glass fiber-reinforced SMC materials, which is an important consideration given the sustainability requirements in the automotive industry.
Substructure and battery module
For the supporting structure of the battery housing, the cooperation partners chose aluminum as a proven lightweight material. The general goal for the supporting structure was simple geometries and thus lower production costs. “The bottom plate is the basis of the entire battery construction and has cross-members that the battery module is mounted on. The carrier plate for the battery management system is also attached to the aluminum base,” reports Philipp Taschner, Project Engineer of VESTARO GmbH. Two aluminum deformation elements provide the necessary side impact protection through absorption. The module alignment of the battery cells enables separation of the electric poles, which provides higher safety in the event of a crash and enables easy cooling.
LION Smart’s supercell concept was used for the batteries. “The design of the battery cells with a low number of components is intended for fully automated, cost-efficient production,” explains Taschner. “In addition, the battery design is particularly safe, as the individual cells are enclosed in a non-flammable dielectric coolant.” This not only provides higher safety, it also ensures a constantly low average temperature within the battery, which reduces cell aging. The modular series connection design of the battery also allows flexibility in the number of modules, with a very low overall height of 90 mm.
Validation of the battery concept
“To verify the safety of the concept and its viability under conditions of actual use, the Computer Aided Engineering (CAE) department at Forward Engineering performed extensive structural and safety simulations,” reports Taschner. The tests included a simulation of overall torsion and bending rigidity, lateral pole impact of up to 350 kN and short pressure resistance in thermal runaway, all of which were passed without problems. The limited mechanical performance of the base structure resulting from its intentionally simple geometry was effectively compensated by the optimized GF SMC, thanks to the design freedoms provided by the material. “The insulating properties of the epoxy SMC housing came to the fore in the thermal 2D simulation of the battery pack,” notes Ooms. “Our material can withstand 10 minutes at 800 °C without burning through, and its insulating properties protect surrounding components and materials from temperatures over 300 °C.” In the past, glass fiber-reinforced SMC materials have been difficult to work with, so this point was likewise thoroughly tested. Lorenz made multiple complex hardware demonstrators to verify the series suitability of the material and the production process. “Using the diamine-based epoxy hardener VESTALITE®S, we were able to create a simple and fast-curing SMC material with the required mechanical properties,” explains Ooms. “In our tests, curing times of three minutes were achieved without workpieces adhering to the mold.” Moreover, the SMC with VESTALITE®S has no styrene emissions and only low VOC emissions. The cooperation partners have made several configurations of their battery concept. “Currently we offer three energy configurations, which are competitive with or superior to current battery models on the market in terms of energy density, safety, and costs,” says Taschner in summary. “With all-in weights of 412.1 kg at 65 kWh, 527.3 kg at 85 kWh and 789.2 kg for the configuration with 800 V at 120 kWh, and the modularity and flexibility of the overall concept, we consider ourselves in a very good position to compete with other suppliers.”
Further information: batterycase@vestaro.com
Lorenz Kunststofftechnik GmbH was founded in 1966 by Siegfried Lorenz and remains family-owned. It has been in the second generation, under the management of Thomas Lorenz, since 1996. Initially the company specialized in the manufacture of various glass fiber products before expanding its capabilities to include the production of SMCs and BMCs. Today Lorenz is active in semifinished goods manufacture, research and development, customer- and component-specific material development, and thermoset recycling. It supplies semifinished components to customers in the automotive, electric, construction, sanitary, chemical, home appliance and railway vehicle industries. At its headquarters in Wallenhorst, near Osnabrück, the company maintains production facilities, a laboratory, and a workshop. Research and development are a priority for the company, and it collaborates with numerous universities in the area.
Evonik is a world leader in special chemistry. The company is active in more than 100 countries around the world and generated sales of € 13.1 billion and an operating profit (adjusted EBITDA) of € 2.15 billion in 2019. Evonik goes far beyond chemistry to create innovative, profitable, and sustainable solutions for customers. More than 32,000 employees work together for a common purpose: We want to improve life – today and tomorrow.
The Crosslinkers division offers a wide range of products and capabilities in coatings, adhesives, construction, high-performance elastomers, and composites. In addition to isophorone-based products, the portfolio includes a complete range of amine crosslinkers for applications at ambient temperature as well as thermosetting systems. Due to their mechanical strength, long life, chemical resistance, and outstanding adhesiveness, these products are used primarily in industrial applications.
The Minth GmbH in Unterschleißheim, Germany, is the European headquarters of Minth Group, which was founded in 1992 in China. Since its founding, the company has developed into one of the top 100 automotive suppliers. The main products are battery cases for EV and hybrid vehicles, as well as exterior trim parts, chassis and body structural parts and electronic components for motor vehicles. In addition to classic metal based materials, primarily lightweight materials such as aluminum and plastics are used. In order to meet even the highest demands in this field, the Minth Group has developed a broad portfolio, from manufacturing and processing to complex assembly and premium surface finishes. The company consistently focuses on sustainability and continuously develops innovations that flow directly into our manufacturing processes and the products of our customers. By joining the Vestaro consortium, Minth is aiming to make a substantial contribution to the improvement of high-voltage battery storage systems and make these systems more environmentally friendly, more efficient and more affordable.
More Stories
TomTom’s Orbis Maps with 3D Lane geometry set new standards for mapping precision
Accelerating The Development of Hydrogen Vehicles & Infrastructure – Europe’s Biggest Players Meeting at Premier Event
Automotive IQ Announces the 15th Annual Automotive Functional Safety Week 2025