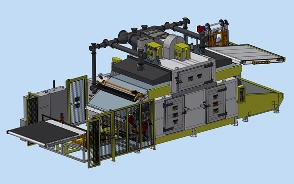
Example of a heating system.
Article summary
When manufacturers of automotive textiles consider adding or upgrading thermal processing methods and equipment for their facility, they tend to stick with what they know works. But just because something “works” doesn’t make it ideal. This article summarizes the common automotive textile thermal processing methods and describes the products and applications best suited for each. It includes a case study about how a North American textile manufacturer overcame their resistance to change and integrated a system that reduced waste and increased quality and reliability in manufacturing.
When manufacturers of automotive textiles consider adding or upgrading thermal processing methods and equipment for their facility, they tend to stick with what they know works.
It’s easy to see why. Intense competition, low margins and the declining price structure of automotive OEM contracts box suppliers into making “safe” process and equipment decisions that emphasize predictability and risk management.
But what if the longstanding doctrines that guide successive generations of plant and corporate engineers are based on a flawed understanding of thermal processing methods? Decision makers follow the lead of those who came before them. “This is the way to do it,” they say. Why? “Because it’s worked for us.”
We all know that just because something works doesn’t make it ideal. But we also know that it’s risky to investigate potential process or equipment changes that deviate from “the way we’ve always done it.”
A key role we play as an industrial oven provider to automotive textile manufacturers is to share our thermal processing knowledge to burn off the fog of tradition and help engineers see their options more clearly.
With that in mind, the common heating methods for automotive textile products are discussed below. Included in the summary of each method are examples of appropriate applications.
Then, we share a case study on how a North American automotive textile manufacturer overcame resistance to change and adopted a better method for pre-heating sound attenuating materials.
Infrared (IR) thermal processing
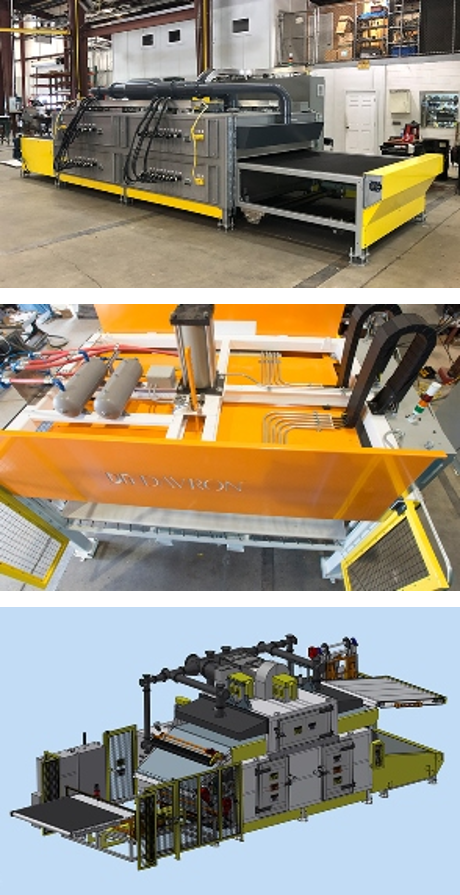
Infrared (IR) heating occurs when electromagnetic radiation is directed at a workpiece. The name comes from the infrared portion of the electromagnetic spectrum, with wavelengths from 700 nm to 1 mm.
Short-wave, high-intensity IR heat is best applied to a part surface over a short period of time. Drying ink or other liquids on part surfaces or flash curing after powder coating are among the common applications of IR thermal processing.
IR is typically not suitable if a workpiece must be heated consistently through its entire cross section. Thick, dense parts or parts made of materials with low heat transfer coefficients do not respond well to this method.
Infrared thermal processing is common in automotive textile manufacturing, but it’s not always the ideal method for these products.
This is because IR energy heats surfaces quickly but does not penetrate very far inward. Consequently, manufacturers using IR heat to prepare automotive carpeting struggle to reach the specified core temperature without roasting the surface beyond the point of destruction.
However, IR is well-suited for adhesive-backed plastic fiber carpeting. By focusing the energy only toward the surface where the adhesive was applied (the B-side), the adhesive is activated and the carpet fibers become much more malleable. The short-wave energy never penetrates through the part, preserving the A-side finish.
Radiant heat thermal processing
Let’s clear up some nomenclature:
In physics, radiant heat refers to electromagnetic radiation that emits from something hot.
Under that strict definition, infrared as described above is a specific type of radiant energy characterized by its electromagnetic wavelength.
So, radiant heating in industrial thermal processing refers broadly to electromagnetic radiation and is not confined to specific bandwidths or wavelengths.
Besides infrared heaters and lamps, the most common source of radiant heat is piping filled with steam, hot water or hot oil.
Very thick parts that require much longer soak times are good candidates for radiant heating.
It also works well for thermal processing of many kinds of plastics, including polycarbonates.
While radiant heating is generally rare in automotive textile manufacturing, some manufacturers have adopted systems that combine radiant and IR heat to process carpets.
Concentrated IR energy melts glue on the B-side while milder radiant energy warms the A-side.
Convective thermal processing
Anyone who bakes at home is familiar with convective heating, in which heat is transferred via the movement of molecules in a fluid.
In the case of industrial thermal processing (as with home baking), the fluid is the air inside the oven.
In convection, differences in temperature among molecules cause them to move in relation to one another. This thermodynamic motion imparts heat to a workpiece.
Forced convection is a variant of this method in which fans direct heated air toward a workpiece. The way the air is directed improves the speed and uniformity of heating, providing an advantage over natural convection that’s made it popular among manufacturers.
Electric heating elements and gas-fired burners are the most common sources of heat for convection ovens. Gas ovens tend to heat faster, are more adjustable and less expensive to operate for industrial scale production.
Electric ovens are better suited for inert atmosphere ovens or for processes that are sensitive to the byproducts of gas-fired burners.
Convective heating is quite versatile, stable and forgiving. Deciding whether to use it is less a matter of the characteristics of the method itself and more a matter of whether the method is viable within the broader parameters of the manufacturing process.
Thicker, denser, permeable materials or those with lower heat transfer coefficients are generally ideal for convection heating.
Forced-air convection heating is not an ideal method for adhesive-backed carpets or materials with powder adhesives applied prior to thermal processing. This is because adhesive-backed carpets start out as impermeable materials but then become permeable as the adhesive melts.
Unless all the adhesive melts in the same instant, “holes” will form and all the heat inside the chamber will pour through them rather than permeate the piece evenly. This can cause severe damage. In the case of products with powder adhesives, forced air inside the chamber ends up blowing the powder off the surface of the material before it melts.
Contact thermal processing
Contact thermal processing is more straightforward: the transfer of heat from something that’s hot to something that’s not via direct contact.
Separate, controllable zones of electric heating elements inside aluminum platens are by far the most common setup.
Aluminum’s relatively high conductivity makes it the ideal metal for contact heating. (Copper, gold and silver all have higher thermal conductivity than aluminum. But copper is around seven times more expensive than aluminum. Gold and silver are even more monstrously costly.)
Electric contact heating is usually best because the heating elements can be oriented in programmable zones throughout a platen and dialed up or down in intensity depending on process specifications. Pumping heated oil through metal platens also works, but it’s not as easy to control the heat. Oil systems also come with a leakage risk.
Contact heat should almost never be specified for materials that include adhesives. This is because the adhesive material will stick to the platens when it melts, making a gluey mess that operators must scrape off. This risk is minimized in some cases if platens are protected by Teflon coatings, or if protective films are applied to the product prior to heating.
We’ve observed that in most cases where manufacturers use contact heating, they could replace it with convection or IR and do the job in half the time. What’s more, the utility costs associated with electric contact heating are far higher than the cost to operate gas-fired convection systems.
Case study: Alternative heating method improves heavy layer thermal processing
Often, the engineers responsible for meeting production benchmarks tend to stick with what’s familiar because making a change represents a bet too risky to place.
But in some cases, a triggering event demonstrates the need to improve a process. And if that need is acute enough to overcome resistance to change, it motivates engineers to explore new possibilities.
That was the case in 2017, when an existing customer sent our team the process specs for a new heating system. Their initial instructions were clear, but our engineers believed they could develop a better alternative.
The customer’s request
Our customer was a major North American supplier of automotive textiles who was awarded a contract to manufacture carpet systems upon an OEM’s announcement of a new vehicle model.
The supplier determined they needed a new oven to pre-heat what are known as “heavy layers” made of a mixture of petroleum products and barium sulfate. These thin sheets are attached to the undersides of carpets to dampen engine, transmission and road noise.
After conducting internal testing, the customer approached Davron with a request to develop a single-zone infrared (IR) oven to pre-heat the heavy layers prior to further processing. The customer also specified that the system’s cycle time not exceed 30 seconds.
However, recall that IR heating is not an ideal method for such an application. The effectiveness of high-intensity, short-wave IR energy is directly tied to (and limited by) the heat transfer characteristics of the material it heats. Due to their makeup, heavy layers transfer heat poorly.
Instead, Davron engineers proposed a single-zone convection system that would deliver forced air from above. Convection heating is less intense than IR but is more suitable to heating products with low heat transfer coefficients.
The customer agreed to our proposed changes and the system went into production.
Problems emerge after first-generation system integration
Not long after installing the single-zone forced air system, the customer reported some puzzling problems.
First, the product didn’t always transfer correctly from stage to stage as designed.
Instead, it sometimes stuck to the conveyor and became lodged in the machine. The gummy wads of product were unusable.
Second, the product would sometimes emerge from the oven totally destroyed instead of merely gently pre-heated.
Our investigation of the issues revealed a simple root cause that had cascaded into a serious problem that impacted production:
- The heavy layer blanks were stored outdoors
- During winter, the blanks would be brought into the facility and processed while still cold
- Operators noticed that the cold blanks didn’t heat properly under the normal recipe, so they cranked up the heat
- Around this same time, the OEM changed their heavy layer specification, doubling the thickness from 1/16” to 1/8”
The combination of thicker layers, cold storage and higher heat caused the product transfer and destruction issues.
Once aware of why these problems occurred, our engineers got to work solving them.
Second-generation system features novel design updates
A few crucial system design updates corrected our customer’s problems and significantly enhanced their production quality and efficiency.
First, we chose to add a second heating zone and double the overall heating time.
Product would enter the first zone and heat for 30 seconds. Then, it transferred into the second zone for 30 more seconds of heat. In this design, pre-heated product still emerged every 30 seconds and the customer’s specified cycle time was preserved.
In doubling the heating time, the oven could run at a lower set point. A lower temperature combined with the design changes described above meant that heat was delivered to the core of the products while eliminating the risk that the surface would get too hot.
Second, we decided to apply heat via forced air from both the top and bottom of the product. Our testing of the second-generation system showed that doubling the heating time and heating from both top and bottom delivered heat to the core of the heavy layers more effectively given the low heat transfer coefficient. It resulted in much more consistent heating regardless of the conditions in which the product was stored.
Because the heating time and heating from two directions instead of one represented a significant increase in required energy, we recommended switching from electric heating to less costly natural gas.
As a final precaution, we installed sensors that measure the temperature of the parts before and after heating. These data are stored and accessible for troubleshooting.
Assess your products and processes
You’d find plenty of folk wisdom on the factory floor. “If it ain’t broke, don’t fix it.”
But manufacturers shouldn’t settle for “ain’t broke.”
And just because bucking tradition introduces new risks, that doesn’t mean they’re any worse than the risks that lurk within the status quo.
Assess your products, assess your processes, and if you need to, consult with a thermal processing expert to identify the right mix of methodology and equipment that reduces risk, boosts reliability and gives your facility an edge.
More Stories
Acoustic sensor systems and Fraunhofer measurement technology for in practical testing ͏
OSI Systems Receives $10 Million Order for Cargo and Vehicle Inspection Systems
Mitsubishi Electric Automotive America Launches Guardian Generation 3 Trial with Seeing Machines in North America