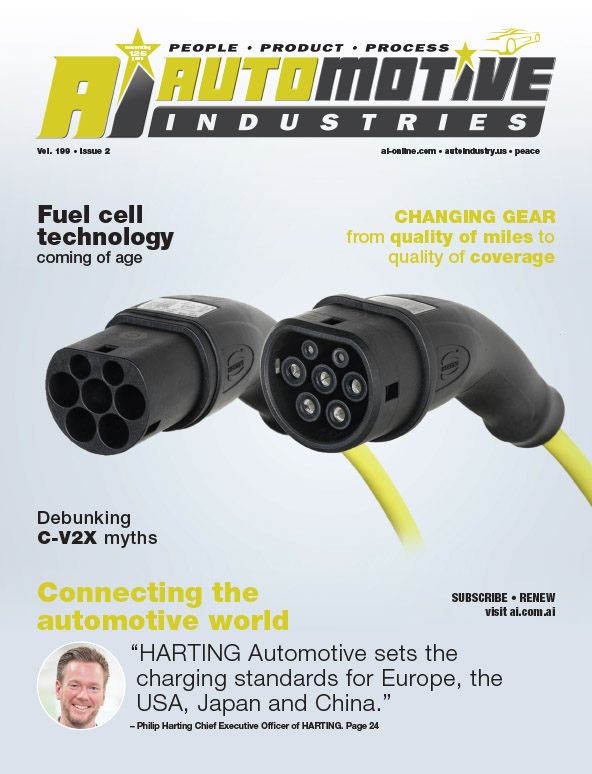
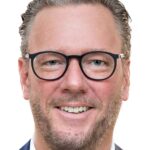
Fast, secure and reliable connectivity within factories and vehicles, as well as across international borders, is needed for Industry 4.0 to live up to its promises, and for artificial intelligence to automate increasingly complex systems.
For the 75-year-old Harting Technology Group, the industrial connectivity requires three “lifelines” – data, signal and power. The company manufactures electromagnetic actuators for automotive and industrial series producti
on, charging technology and cables for electrical vehicles, as well as hardware and software for customers and applications in the automation, robotics and transportation sectors.
Automotive Industries (AI) asked Chief Executive Officer Philip Harting to share some of the challenges the family-owned company has faced over its history.
Harting: Constant innovation has been HARTING’s success formula ever since the company was founded. Our focus has always been on the demands and requirements of markets, customers and users. After the initial founding years’ production of appliances for domestic and outdoor use, such as waffle irons and irons, energy-saving lamps, cigarette lighters and electric fences, the company concentrated on automotive electrics. Subsequently, phonographic devices such as record players, tape recorders and jukeboxes were added to the line-up, as well as medical equipment.
With the development of the Han® connector, patented in 1956, HARTING evolved into a market leader in industrial connectors. The portfolio now includes industrial connection technology for the three lifelines of data,
signal and power, making HARTING a driver of digital transformation and Industry 4.0.
AI: How has this improved automotive manufacturing?
Harting: Our subsidiary HARTING Automotive was founded in the mid-1990s. We have built up the business incrementally, producing customer-specific cable harnesses and electromagnetic components for the automotive supply and automotive industry, as well as for industrial markets.
For some 25 years HARTING Automotive been a leading innovator in magnetic systems for actuators in automotive engineering as well as mechatronics and connection technology.
We have established ourselves as a connection technology specialist in the growth sector of electromobility.
We are also a preferential, sought-after partner for highly efficient, customized charging solutions. For example, we are a first-tier supplier of charging cables for the Volkswagen Group.
Our subsidiary provides charging solutions for Volkswagen’s modular e-drive system (MEB), the Audi e-tron and the Porsche Taycan. In recognition of our contribution, we received the Volkswagen Group Award 2020 in the e-mobility category. With this coveted award the Volkswagen group honors the exceptional performance and innovative strength of HARTING Automotive.
AI: What technical development in the HARTING Automotive are you particularly proud of?
Harting: HARTING Automotive sets the charging standards for Europe, the USA, Japan and China. The transmission of energy and information plays a central role in electromobility, just as it does in mechanical engineering. Consequently, it is only logical that HARTING is also involved in this field and enjoying increasing success.
We have now developed a technology that enables an electric car to be charged in record time – and up to 1000 volts. The technology allows electric vehicles to be charged as quickly as today’s refueling, achieving an 80% range in 15 minutes – so that is a genuine quantum leap.
Remember: If you want to transmit a lot of energy in such a short time, the cable cross-section must be wider. But this makes the charging cable too thick and almost impossible to handle.
The alternative is to cool the cable, which is the course we took together with our customer. Thanks to the cooling, the cable remains flexible, while still transmitting 350 kilowatts of power with 800 volts of charging current. HARTING Automotive also supplies the entire cooling circuit.
AI: How is HARTING meeting the challenges of constant change and innovation?
Harting: Out of our 5300 employees worldwide, we count around 700 engineers and scientists active in our company. There is a strong focus on digitization. The company’s products and service offerings are supporting the digital transformation of the business world, commerce and society, especially in the markets of transportation, e-mobility, power generation and -distribution, mechanical and plant engineering, event and medical technology.
In our own company we digitalize wherever it is expedient and possible. In order to generate greater customer benefits, HARTING is pushing ahead with the formation of networks and the establishment of partnerships with relevant specialists, suppliers and research and science institutions. Thanks to these synergies HARTING is able to offer complete hardware and software solutions for an extremely wide range of users and requirements. In
strategic terms, the network of development, production and sales companies is also being further expanded. Closeness to customer is of decisive importance for HARTING.
Our manufacturing activities are distributed across 14 locations worldwide.
AI: Coinciding with the 75th anniversary of the company’s inception, you won the German Innovation Award for the second year running. What does this mean for your customers?
Harting: As my grandfather Wilhelm Harting, who founded the company in 1945 shortly after the war, always said: “Quality is when the customer comes back and not the product”. Quality is one side of the coin, while innovation is the other. Our eng
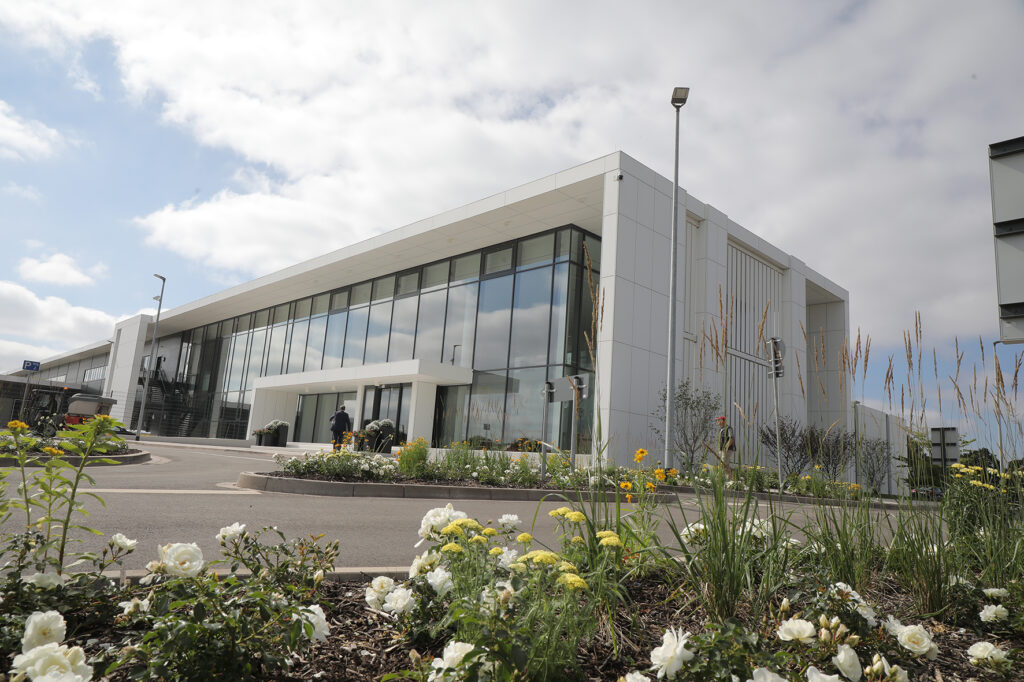
ineers, developers and technicians always have their fingers on the pulse of times in order to develop new innovative solutions and products delivering the greatest customer benefits.
Implementing our IoT solutions at a very early stage in our own production processes allows us to rapidly ascertain exactly where customer benefits are generated. This provides us with additional aspects for technical implementation and is one way of reducing the technical challenges of installation implementation for our customers.
In this context, we focus on understanding the fundamental technological change as well as customer requirements. The advance of artificial intelligence and the development of 5G networks will usher in further changes and opportunities. Consequently, we are actively involved in standardization committees in order to turn technical challenges into future standards.
In pursuing this course, our employees are the decisive factor, the key to making the digital future a success. Human beings will shape and design Industry 4.0 and the course it will take. Knowledge and ongoing further education are gaining in importance, and learning to think digitally and working with digital tools and means is a key task and obligation for all employees.
At the moment we can see that the electric mobility market is highly dynamic and in a stage of significant growth. In countries like Germany this is driven by policy makers, given that subsidies are granted for the purchase of electric cars. Another approach is that of the European Union, which is stipulating ever lower limits for carbon dioxide and nitrogen oxide vehicle emissions. Consequently, European manufacturers are forced to
electrify a certain share of their fleet portfolio.
In addition, environmental awareness has risen significantly in recent years, and therefore the acceptance of electric vehicles has also gained considerable ground. And what is more: the technical changes in battery technology translate as higher storage capacity. In other words, we are perceiving increasing attractiveness in the extended range area and are offering our optimal fast-charging solutions.
We look to the future with optimism, given that HARTING will participate in this market growth and further expand its business.
More Stories
Industry-standard switching & simulation systems from Pickering Interfaces on show at Space-Comm Expo
Bangkok International Motor Show 2025 – The Talk of Sensuous Automotive
SEPA and Bidgely Release Report on the Power of AI for Transportation Electrification