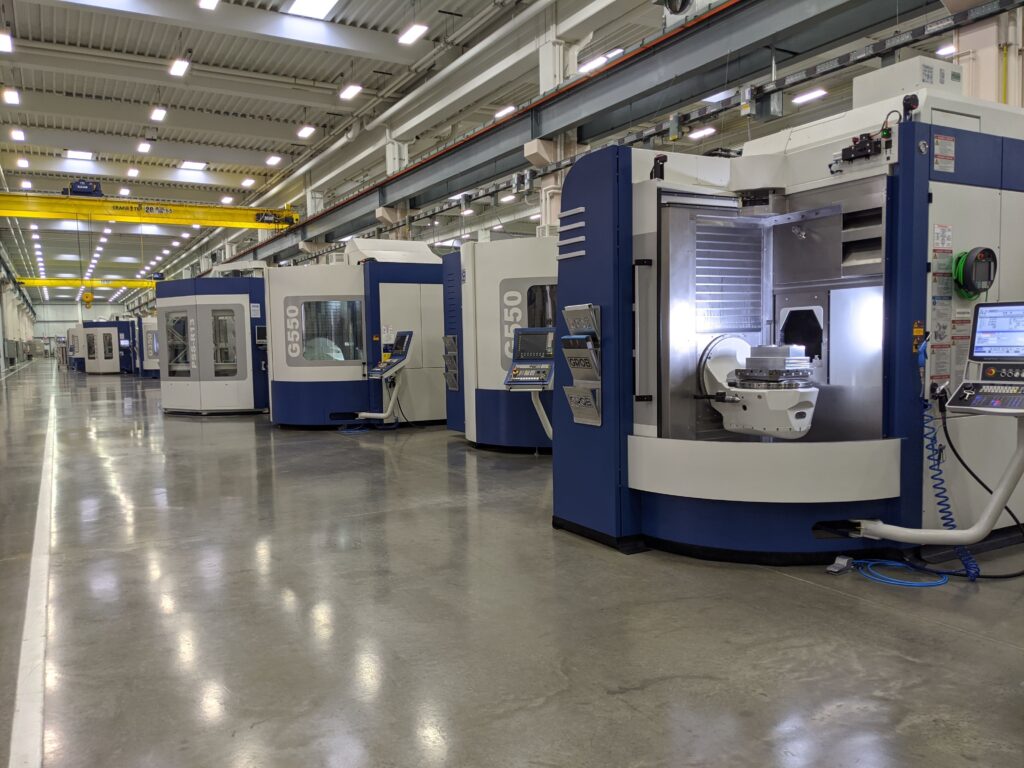
From automotive and aerospace industries to job shops and small-scale production facilities, trends in manufacturing are shaping the production of machining tools and manufacturing systems. The case of major machine tool builder GROB exemplifies how adaptation and innovation can help companies developing manufacturing technology to keep pace as industries and their needs change.
Shifting needs in machining and manufacturing
E-mobility in the automotive industry
The automotive industry is moving, slowly but steadily, away from traditional fuels and combustion engines to an emphasis on e-mobility technology. E-mobility, the broader category that includes hybrid and fully electric vehicles, has grown from a niche corner of the market to the clear future of automotive technology in only the past several years. Production of these vehicles has remained slow, however, machining and manufacturing efficiency techniques in use across the automotive industry largely have not yet been adapted for electric vehicles. Just as the industry transitioned from transfer lines and dedicated production solutions to flexible CNC machines and other adaptable machining technology in the late 1990s and early 2000s, we can now expect to see a shift towards automation and adaptable solutions for large-scale electric vehicle production in the next decade and beyond.
Automation
Automation is not only a critically important trend in the automotive industry. Even in job shops and other smaller-scale production facilities, automation technologies are beginning to be implemented in order to enable companies to produce more, faster, and with fewer people in the shop. In job shops producing high-mix, low-volume parts, automation delivers a rapid return on investment and increased profitability, as fewer highly skilled people are capable of producing more in shorter spans of time. Machine tool builders and other manufacturing technology developers must be able to deliver automation solutions, whether integrated into their systems or in add-on, compatible units.
Materials
Especially in the aerospace and military technology sectors, development of new materials is driving innovation in machining and manufacturing practices. Whether used for engines or frames, these materials are placing a greater demand on machine tool builders to configure new machines that are capable of handling harder, more abrasive, and otherwise more demanding materials.
Industry 4.0
Finally, the push towards Industry 4.0 standards across different markets is driving demand for process data. This means that machine tool builders and other companies developing manufacturing technology must be able to deliver process data in a concise and easily-achievable manner, for customers to integrate into their manufacturing process management technologies.
Foundation for an adaptive response
So, in this time of rapid adaptation and change being necessary to keep pace with trends across a wide range of industries, how can machine tool builders and others developing manufacturing technology expect to succeed? GROB, a family-owned company with production plants in the United States (Bluffton, Ohio), Germany, Brazil, China, and Italy, is an excellent case study of a global manufacturing technology leader that is keeping up with and even shaping trends. Derek Schroeder, Universal Machines Sales Supervisor at GROB offered these four highlights of how the company has managed to stay competitive and keep pace with the ever-changing demands on machine tool builders working in the automotive, aerospace, military, and small-scale production markets.
- Vertical Integration: GROB is not just concerned with production or assembly, but with machining, checking, assembly, and more. The company is capable of supplying its customers with integrated solutions, and does so while building every component of its own machines in-house. This has been a gradual process that has enabled the company to better serve its customers around the world. The Bluffton, Ohio facility, for example, started off in 1990 as a small sales and runoff facility with 30 employees. Now with more than 550 employees, the Bluffton facility manufactures the entire GROB product line in-house. The capacity to invest in vertical integration over the past several decades was made possible by the company’s family-owned status; the company’s profits are continuously re-invested into expansions that serve customers and allow it to keep pace with industry trends.
- Apprenticeship model: GROB’s growth, exemplified in that of its Ohio facility, is not exclusively thanks to its vertical integration. The company also has implemented an apprenticeship program that introduces new workers to every aspect of the company and grew in the Bluffton facility from 6 to 40 apprentices per year over just two decades. To date, roughly 40% of the Bluffton workforce has been through GROB’s apprenticeship program. Even those employees who do not complete apprenticeships still become familiar with each and every department. As a result, GROB’s customers can get sales, service, and support from people with expertise about the company’s full range of products.
- Engineered solutions: Although GROB has a number of products that are foundational to its success, it is also capable of supplying individualized, engineered solutions to customers that are precisely tailored to their end-use. This focus on retaining and growing with customers ensures that even as trends within the industry shift, GROB can meet its customers’ needs at every stage.
- Transfer of knowledge across industries: Finally, since GROB manufactures machining technology that is used throughout many different industries, the trends that shape industries at the cutting edge can begin to benefit other industries that may be lagging behind. For example, manufacturing products that can machine cutting-edge aerospace materials now will benefit automotive customers in the future once these materials become more mainstream. Likewise, solutions for automation or data management developed for one industry can be applied to others as manufacturing practices evolve.
Conclusion: Keeping pace with and shaping industry trends
GROB is a prime example of how adaptation in business practices is required in order to keep up with and even shape trends across industries. GROB is implementing techniques and products to meet all of the needs described above with regards to e-mobility, automation, new materials, and Industry 4.0 standards. They are even bringing expertise from some industries and markets into others, such as through implementing automation technology long used in automotive manufacturing into their universal machining products. The company also put this spirit of adaptation and innovation to work through their response to COVID-19; GROB supported major U.S. automotive manufacturers who shifted production to ventilator manufacturing by supplying components to adapt existing automotive manufacturing and machining tools into ventilator manufacturing lines. Through an overall ethic of adaptation and innovation, embodied in its vertical integration, apprenticeship program, engineered solutions, and transfer of knowledge across industries, GROB demonstrates how machine tool builders can move with and shape the industries they supply.
More Stories
BRANO and DOMO join forces to replace aluminum with TECHNYL® polyamide
Selecting the Ideal Linear Phased Array Transducer for Your NDT Requirements
From Laser to Waterjet: The Cutting-Edge Techniques Driving Efficiency in Auto Production