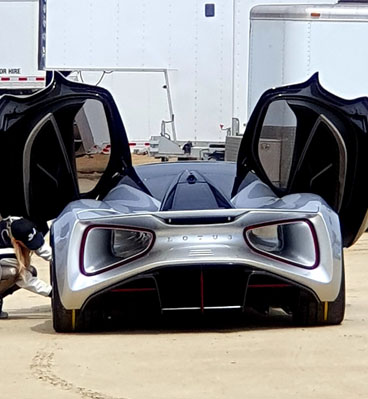
Britain is on track to be a leader in electric vehicle battery development and production, thanks to government funding and support.
The positioning of the country as a center for battery technology and production has contributed to the announcement of one of the largest industrial investments in the United Kingdom – a £2.6bn (US$ 3.5 bn) Britishvolt gigafactory to be built at Blyth in the north-east of the country. Nissan has subsequently announced plans to build a £1 billion ($1.38 billion) “gigafactory” in Sunderland. The Japanese automaker said it was launching the project — dubbed Nissan EV36Zero — along with Envision AESC, a battery technology company, and Sunderland City Council.
Six other gigafactories are reported to be in various stages of planning.
Automotive Industries (AI) asked Tony Harper, Challenge Director of the Faraday Battery Challenge, what the objective of the contest is.
Harper: The Faraday Battery Challenge, delivered by the Government arm, UK Research and Innovation, is a fund of £246 million which will be invested to support the development of new battery technologies.
It will fund research, innovation and scale-up facilities for batteries for the electrification of future vehicles and other applications that support an electrified economy. This should lower carbon emissions and help to tackle air pollution while creating new opportunities and industries. By focusing on the automotive sector initially, the challenge will allow the UK to realize its commitment to move to full electrification and zero emission vehicles. It will also make the most of the growing batteries market – estimated to be worth £5 billion in the UK and £50 billion across Europe by 2025. Innovate UK and the Engineering and Physical Sciences Research Council will deliver the challenge on behalf of UK Research and Innovation.
AI: Is the UK vehicle battery industry a global leader in battery development?
Harper: Clearly, we are behind a number of countries in terms of industrial capacity at present, something that many people including myself are working hard to change. In terms of battery technology development, however, we are very strong. In battery chemistries that are getting close to market, I would cite sodium ion, lithium sulfur and high silicon content anodes as particular strengths in terms of cells. I would also cite strength in battery module and pack development particularly for high performance applications.
AI: As the former Jaguar Land Rover Director of Engineering Research, what experience can you bring to the global challenge of battery development?
Harper: Being the Research Director in a company like JLR is an absolute privilege, but also gives you a very interesting perspective. From a technology point of view, you spend a lot of time being too radical for the conservatives and too conservative for the radicals!
It means that you can see both the possibilities that come with new technology as well as the constraints of the very substantial industrial and quality systems that technology of this kind has to be delivered through. That experience, along with other great talent we have in our extended team gives us a great chance of delivering on the UK’s potential. I have also been developing Ultra-Low and Zero Research vehicles since 2008, which helps.
AI: How do you see the UK Faraday Battery Challenge award of £246M fund supporting car battery innovation?
Harper: The total announced investment is now almost £318m. The Faraday Battery Challenge has been running now for three years. The philosophy is relatively simple. In order for the UK to capture the value from the transition to electric vehicles, we need to deploy at scale those technologies that are ready; develop those that are not; and research solutions to problems that we cannot yet solve. So to date, in terms of supporting car battery innovation, the Faraday Battery Challenge has delivered the UK battery Industrialisation Centre, which is essentially gigafactory capability in an open-access manufacturing development facility. There are 64 business-led collaborative R&D projects all developing solutions to the issues of mass adoption (cost, energy density, rapid charging etc.). Scientific support now involves over 450 researches in the UK’s top universities. They are working on nine large-scale projects cracking the tough problems that will unlock the breakthrough potential for the future.
AI: Is the infrastructure of more than seven giga battery plants pivotal to the establishment of a battery value chain in the UK?
Harper: Certainly, the first 2-3 are. A battery represents a little under 1/3 the total value of an electric vehicle. If the cells were imported and only the modules and packs assembled in the UK, about 20% of the value of the battery would be captured locally in terms of jobs, value-add, etc. If the cells are made here, that increases to 45%; and if the upstream chemicals are processes here then the value to the UK is 80%+ estimated to be worth up to £9 bn by 2035. There are investment “chicken and egg points” all along this chain. Gigafactories are critical to unlocking this.
AI: Can you tell us about the UK Battery Industrialisation Centre (UKBIC). The first of its kind in the World?
Harper: The need for UKBIC arises from another “chicken and egg”. Companies developing new battery technologies in the UK are typically doing so in labs that are capable of creating prototype cells of representative chemistry and format, but not at industrial rate using representative processes.
This is an issue in the case of batteries since you can have two seemingly chemically identical batteries (one lab-made, one factory produced) that will have very different performance characteristics. This means that customers will not place orders for batteries on the basis of lab-made cells and companies cannot invest the very significant sums in a factory without an order.
UKBIC unlocks this and also provides the critical manufacturing expertise required. The equipment is the same state of the art equipment you would find in the latest gigafactories but the facility is configured for manufacturing development and validation rather than optimized for end-to-end production. Other regions of the world have come to the same conclusion, but the UK is the first by some margin to bring this capability on stream.
AI: How key is the UKBIC’ strategic importance to achieving the govt. ambition of 1.5 million electric vehicle batteries by 2040?
Harper: In a word, “very”. Not only in the mode described above, but also if you are an existing UK volume producer or an inward investor looking to set up substantial capacity in the UK. There will be a desire to localize the inbound processed chemicals and upgrade technology over time. Being able to develop, optimize and stabilize manufacturing processes whilst a gigafactory is being built or whilst your existing factory is busy making exciting product is a critical enabler for the growth we need.
More Stories
Bangkok International Motor Show 2025 – The Talk of Sensuous Automotive
Dry silicon composite by Blue Current is the next generation of battery technology
Battery Coating and the Impact on Charging Infrastructure for Electric Vehicles