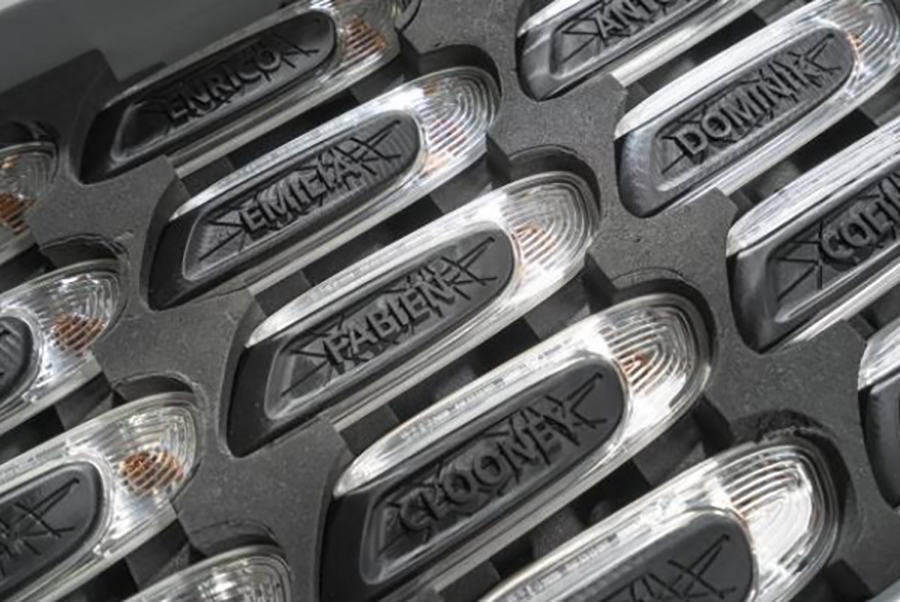
The automotive industry is widely considered to be one of the pioneers of additive manufacturing (AM). Way back in 2018, BMW was already producing over 200,000 3D printed car parts a year (a leap of 40% compared to the previous year). In tooling, AM is even more prevalent. For example, Michelin 3D prints (in metal) over one million siping tools a year for use in its tire manufacturing line. The industry’s adoption of AM is not surprising, as the technology provides the solution to OEMs’ biggest challenges: keeping a lid on production line downtime, increasing customization possibilities, reducing waste and carbon footprint, and, of course, cutting costs both in the production line and in the supply chain.
The automotive 3D printing market is currently estimated at $1.4Bn and is forecasted to grow to $9Bn by 2025[1]. A significant part of this market is attributable to tooling – the jigs, gauges and fixtures that are so critical to keeping today’s increasingly complex manufacturing and assembly lines moving.
Automotive Tooling
The global tooling market is estimated at $200Bn[2], over half of which is attributable to the automotive industry.
The cost of tooling to OEMs alone (i.e. not including tooling used by their suppliers) is estimated to be $550 per car. Some of these tools are already additively manufactured but there is much more to come. The ability to 3D print jigs and fixtures onsite (or locally) and on-demand can reduce tooling costs considerably as well as cut lead times, often from days or even weeks to hours. In addition to minimizing production line downtime this way, AM also allows manufacturers to respond quickly to part failures by either redesigning or re-printing the part, as required. The reduced lead time gives the flexibility to accept and respond quickly to any changes needed to the production or assembly line. For example, Ford’s partnership with Trinckle is reported to have cut the time it takes to design a new jig from 4-6 hours to just 10 minutes. This, together with onsite 3D printing, means that in any failure or redesign event, Ford can get its production lines up and running in a matter of minutes, instead of hours or even days.
Repeatability and Protecting Digital Assets
Repeatability is a hallmark of manufacturing and assembly lines, especially in the automotive industry. Aside from envy-inducing, highly-customized super cars like the Bugatti Chiron, most cars are mass produced. This means that every car of a particular make and model must be identical, and so too must be the tooling that enables their production. Therefore, it is essential they are made in a way that is both consistent and repeatable.
However, while repeatability sounds like a no-brainer, it is a challenge for AM, where parts are produced in small batches (or even batches of one), potentially in different factories or even in different countries. This makes it difficult to ensure that parts are always produced to the same specifications. Any variance in the 3D printer settings or other parts of the workflow can result in a faulty part or weak tooling that breaks and stops the assembly line. With a digital inventory of AM-produced parts, jigs, or fixtures, repeatability is therefore key – whether a file is printed once or a thousand times, in one location or dozens. This relies on securing AM blueprints and ensuring that parts or tooling are produced in exactly the same way with exactly the same settings regardless of where or when the digital turns into physical.
Keeping production moving
At present, LEO Lane estimates that AM accounts for around $2Bn of the tooling market across all industries. To increase this penetration, as well as AM use for end parts, manufacturers will have to maintain repeatability and consistency – and the good news is that there are Software-as-a-Service solutions that enable them to do exactly that! With so many reasons to expand the use of AM, there is no doubt that the innovative automotive industry will continue to find more ways to use secured AM technology to improve the production of both end parts and tooling, without sacrificing quality or repeatability.
[2] https://www.alliedmarketresearch.com/press-release/tooling-molds-market.html
***
Lee-Bath Nelson is Co-Founder and VP Business at LEO Lane, an Israel-based business that empowers industrial manufacturers to securely and consistently manage repeatable additive manufacturing, anywhere anytime, using the company’s cloud-based SaaS solution.
More Stories
DuPont materials science advances next generation of EV batteries at The Battery Show
How a Truck Driver Can Avoid Mistakes That Lead to Truck Accidents
Car Crash Types Explained: From Rear-End to Head-On Collisions