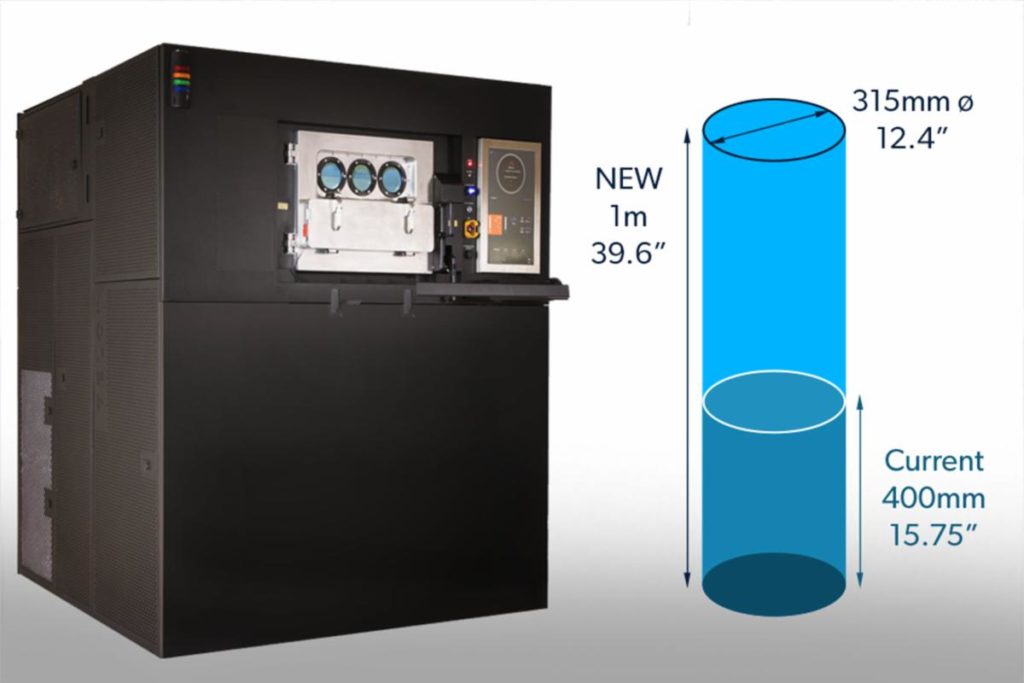
Digital manufacturing innovator VELO3D have pulled out ahead in the race to achieve the tallest build-chamber size with their upcoming one-meter-height metal-powder laser 3D printer. While larger-format “open air” AM equipment exists, VELO’s will be the biggest closed-chamber printer designed to work with the advanced specialty metals–used in aerospace, oil & gas and other precision industries–that must be laser-fused in a tightly controlled, gas-regulated environment to achieve the highest-quality production parts.
VELO3D announced its plans to launch a next-generation Sapphire industrial 3D metal printer with a vertical axis of 1 meter. The system will ship in Q4 2020, with precision-tool and component manufacturer Knust-Godwin securing the first order to produce parts for an oil and gas application.
“Our vision at VELO3D is to enable end users to build whatever they want without the constraints of yesterday’s standards,” states Benny Buller, Founder and CEO of VELO3D. “One of those constraints is the build envelope. A meter-tall system enables industrial applications that couldn’t be built before, especially for oilfield service tools and flight hardware. Best of all, it will still utilize our highly patented SupportFree process, in-situ calibration, and process control for quality assurance.”
The immediate part opportunity that Knust-Godwin will address with the meter-tall Sapphire printer is a part for oilfield drilling that is currently manufactured by more than five subtractive processes. Additive manufacturing enables consolidation of such traditional processes, improving part quality and part performance.
“There tends to be a trade-off between large-format additive machines and part quality; VELO3D is attractive to us because of their semiconductor heritage and engineering disciplines around process control and metrology,” states Mike Corliss, VP of Technology at Knust-Godwin. “We have confidence that we’ll be able to build mission-critical industrial parts without compromises made to part quality.”
The technical features of the meter-tall Sapphire printer include a 315mm-diameter build plate, dual 1kW lasers, in-situ optical calibration, and many of the same characteristics of the existing Sapphire machine. It will be the world’s tallest production metal-powder laser additive manufacturing system, exceeding the build height of both the SLM 800 and the GE Additive X Line 2000R.
About Knust-Godwin
Knust-Godwin has been providing high-quality, precision production machining services for over a combined 100 years to companies throughout the world. It specializes in CNC turning and CNC milling with significant experience in the oil and gas, geophysical/seismic, semiconductor, and medical industries. Knust-Godwin is more than just a machine shop; it is part of the manufacturing solution. From a concept, to engineering, to prototype, to production runs, it provides a place to go for all machining needs. Its commitment to quality produces high-precision part components as well as complicated turn-key assemblies. www.kgsbo.com
About VELO3D
VELO3D empowers companies to manufacture anything. Bringing together an integrated solution of software, hardware, and process-control innovation, Velo3D introduced the first SupportFree capability for 3D metal printing. This enables unlimited design innovation by reducing the need for support structures in metal additive manufacturing. The company’s Sapphire® system is built with a semiconductor mindset on quality assurance, ensuring repeatability and dependability throughout serial manufacturing. Headquartered in Silicon Valley, Velo3D helps companies deliver immediate business impact by making the impossible, possible. To learn more, please visit www.VELO3D.com
More Stories
TomTom’s Orbis Maps with 3D Lane geometry set new standards for mapping precision
Accelerating The Development of Hydrogen Vehicles & Infrastructure – Europe’s Biggest Players Meeting at Premier Event
Automotive IQ Announces the 15th Annual Automotive Functional Safety Week 2025