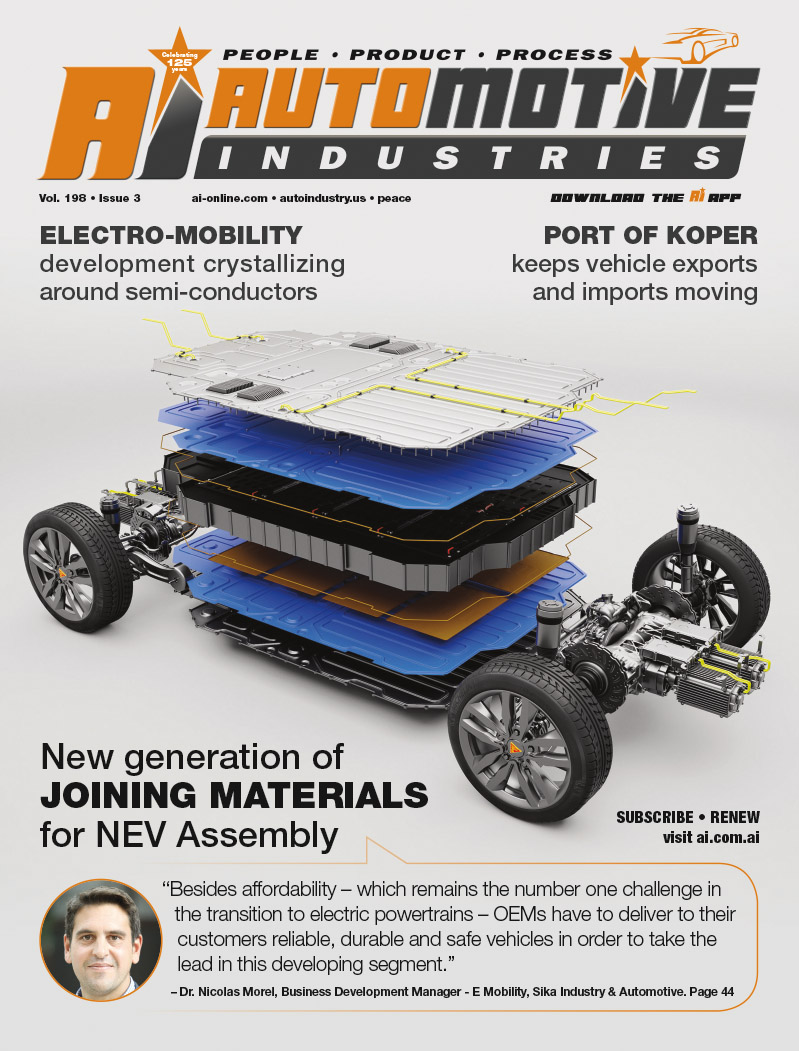
Whatever form of powertrain next generation vehicles use, there remain common requirements – which are that vehicles should be lighter, stronger, safer, quieter and greener.
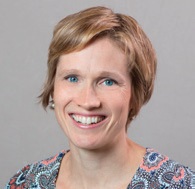
Head of Innovation – Sika
Global Automotive
These needs lead to innovative combinations of materials and the substitution of metal components by composites, plastics and other materials. Sika Automotive says up to 150kg, or 10%, of vehicle weight can be reduced using its range of products.
Sika Automotive is a leading innovator and supplier of automotive bonding, sealing, damping and reinforcing solutions for the vehicle body structure as well as interior and exterior components. It is also at the forefront of developments in 3D polymer printing. According to Jeannette Clifford, Head of Innovation – Sika Automotive Global, the company uses 3D printing during component development and for the building of molds. Using in-house technology, Sika can print a mold and inject prototype parts within 48 hours from the completion of the design.
In 2019, Sika received an Automotive Engineering Expo Innovation Star Award for its new SikaPower® SmartFlow body shop adhesive technology. This injectable adhesive allows new solutions, for example, the bonding of profiles into castings. Such push-in body structure connectors, as found in electric vehicles or lightweight designs, can now be reliably bonded. The same adhesive can be used to bond structural parts over the entire surface. Cavities do not need to be sealed before injecting the adhesive, as the material seals the cavity itself.
Automotive Industries (AI) asked Clifford where Sika’s lead in 3D concrete printing is being transferred to automotive manufacturing.
Clifford: We are already supplying 3D printed solutions where it makes economic sense, especially during the design and development phase. And we can design parts specifically for additive manufacturing, which allows us to increase the manufacturing speed and benefit from the design freedom offered by the technology. It enables new concepts where one part fulfills functions previously covered by multiple parts. We have reactive materials –proprietary adhesives and foamable materials – that we can print, which leads to new applications as well. Sika has built up the “Digital Lab,” a competence center bundling the additive manufacturing know-how for industrial and construction applications, thus bringing concrete printing knowledge together with similar efforts for our automotive materials and combining it with visualization via virtual and mixed reality.
AI: What are the advantages to OEMs of being able to bond a wide range of materials, including printed parts?
Clifford: Having a broad range of bonding solutions at hand allows OEMs to design their vehicles for the best performance and to choose the most suitable materials, including 3D printed parts, be it plastic or metallic.
Sika is in the unique position of being able to offer solutions for bonding, damping, sealing and reinforcing. This includes mixed material bonding, for which we supply adhesives that compensate for the different thermal expansion of the substrates. For example, SikaPower® MBX is used to bond carbon fiber reinforced plastic (CFRP) reinforcements to steel or the aluminum outer skin to the inner steel structure, making the car bodies lighter and stiffer than previous generations. Or in the BMW i3 electric vehicle, Sikaflex® Ultra-High Modulus bonds the CFRP passenger compartment to the aluminum chassis.
AI: Where are the cost savings?
Clifford: Besides giving customers versatility in choosing the most suitable materials and processes, the major part of our portfolio can be applied using standard robotic equipment and is very flexible in its use. Our dry solutions come in the shape of tapes, pads, or engineered injection molded parts, some of which are suitable for full automation. For example, SikaDamp® Autopad, a sealing element for targeted noise damping, was specially designed for automated application. But our products are also suitable for smaller series runs or more manual production sites. We take advantage of 3D printing methods for cost-optimized solutions for each customer approach. Function integration is another area for cost savings. For example, Sika offers parts which act as sealers and reinforcing elements at the same time. Such solutions are developed by our CAE and CAD specialists according to meet customer needs and can save costs. One way of saving costs is through the use of highly reactive or accelerated products that deliver short cycle times. Our strong local presence around the world guarantees short lead times for products and allows a straightforward exchange with the various customer teams for focused development and fast, smooth implementation.
AI: Will bonding ever completely replace welding in the manufacturing process?
Clifford: The joining concepts in a modern car are quite complex and adhesives already play a substantial role with often 120m of adhesive bond lines per car.
The benefits of adhesives are widely recognized: They help to increase car body stiffness, they increase longevity by reducing fatigue effects, and increase the crash safety of a car. And, they are proven to be a cost and energy-efficient solution. Today adhesive bonding needs to be combined with thermal and mechanical joining techniques (e.g., spot welds, rivets) in order to fix the car body structure until the adhesive is cured in the e-coat oven. In general, OEMs have an interest in reducing the complexity and costs of their joining processes. Therefore, we expect that adhesive bonding as a sole joining technique will gain importance, especially for cars produced on new manufacturing lines.
AI: What about structural reinforcing materials?
Clifford: Our products are an integral part of the vehicle stiffness and safety concept. In the body shop we use heatcuring SikaPower® products. Here we have a new award-winning adhesive called SikaPower® Smart Flow can be injected into areas without sealing them off completely. It is particularly suitable for the bonding of profiles to castings in aluminum-intensive designs, such as “space-frame” construction.
For local reinforcement of the car bodies, we have the SikaReinforcer® product range. These injection molded parts contain a foam component that expands during the e-coat oven process and bonds the parts to the car body. Our CAE engineers design and simulate the parts to optimize the NVH and crash requirements.
For smaller cavities or selective panel stiffening, structural tapes or pads can also be used. In the assembly shop, it is mainly our Sikaflex® line which is used to reinforce the body structure, e.g., by bonding the windscreen to the frame and making it a functional part for the body stiffening. In the 2-component range, we received the Swiss Innovation Award 2019 for the new SikaForce® Powerflex technology. This structural adhesive features a combination of strength and permanent elasticity. The high elongation material opens up new design possibilities for composite materials. For more production freedom, it works as a “curing-by-design” material, enabling immediate curing after a desired flexible open time, reducing production time.
AI: Please tell us more about comfort-related solutions.
Clifford: Passengers enjoy a quiet ride, and this can be achieved by sealing common noise transmission paths in vehicle body cavities with SikaBaffle®. These foams expand in the e-coat oven. Our portfolio contains molded or extruded parts, tapes and bulk solutions. Recently, we expanded our SikaBaffle® product range with the introduction of a low bake material, SikaBaffle®-455 LB, which works at oven temperatures as low as 140°C or with shorter dwell times at higher temperatures. This allows energy savings in the production process and the use of baffle materials in areas where the material temperatures remain low. Audible noises are also generated by vibrating body panels. Strategically-placed dampers can reduce those vibrations significantly. The SikaDamp® Ultralite technology is the lightest high-performance damping system on the market and won the Altair Enlighten Award 2018. Its low density allows one to save up to 5 kg of weight on a mid-sized car.
AI: What about end of life? How “green” is the Sika range?
Clifford: Sika has been a member of the World Business Council for Sustainable Development since 2010 and uses its methodology for sustainable portfolio management. There must be no permanent damage to the environment throughout the product life-cycle, from raw material extraction to product disposal. We are driven by the principal “sustainability meets performance,” which means that, besides adding value for our customers, all new developments must be more sustainable than existing solutions. Our products enable greener vehicle concepts, but we work on greener Sika products as well. For example, 10 years ago we were the first to introduce water-based pre-treatments for direct glazing applications – our Sika® HydroPrep-100. And we work hard at reducing our production footprint, particularly CO2 emissions, energy and water consumption, as well as waste generation. Our sustainability efforts are driven by top management and accordingly enjoy a high priority.
More Stories
Industry-standard switching & simulation systems from Pickering Interfaces on show at Space-Comm Expo
Bangkok International Motor Show 2025 – The Talk of Sensuous Automotive
SEPA and Bidgely Release Report on the Power of AI for Transportation Electrification