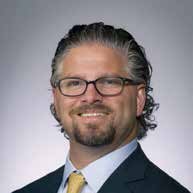
Manufacturing processes for conventional, electric and autonomous vehicles using composite materials have been accelerated by the development of a next-generation silicone solution that is capable of room temperature curing at faster speeds while maintaining the performance advantages expected from silicone adhesives.
According to Bruce Hilman, Global Segment Leader for Transportation Assembly at Dow Performance Silicones, DOWSIL™ EA-4700 CV Adhesive bonds both plastics and metals, with low levels of volatile condensable materials. It will assist with achieving more efficient throughput to produce battery packs and ADAS sensor modules such as RADAR, LiDAR and cameras. According to a company release, this advanced new assembly solution bonds at room temperature to traditional metals and plastics used in electronics assembly.
DOWSIL™ EA-4700 CV Adhesive also offers low levels of volatile condensable materials to support its use near sensitive electronic components. “Electric vehicle and autonomous vehicle development are accelerating across the industry, and engineers globally are seeking innovative solutions to meet safety and reliability requirements while achieving more efficient throughput to produce battery packs and ADAS sensor modules such as RADAR, LiDAR and cameras,” says Hilman. “DOWSIL™ EA-4700 CV Adhesive provides durable adhesion and environmental sealing of substrates used in automotive electronic modules, including aluminum, PBT and PPS. Importantly, this silicone adhesive’s ability to provide faster curing at room temperature enables increased throughput for efficient mass production with less use of energy,” he says. According to Dow, the company’s SILASTIC™ technologies can help meet the growing demand for high-performance, sustainable rubber materials required for the manufacture of consumer goods, electrical, industrial, automotive and other demanding applications where performance, reliability, safety and aesthetics are essential. “Collaborating with our customers to solve their most pressing challenges is our number one priority,” says Charles Zimmer, Global Director for Engineered Materials and Advanced Elastomers. First introduced in 1945, SILASTIC™ brand silicone rubber has become a trusted name throughout the rubber and plastics industry. Customers have the flexibility to choose from a wide range of existing SILASTIC™ solutions or work alongside the Dow team to customize SILASTIC™ compounds to meet their specific needs in areas such as viscosity, adhesion, fluid or heat aging, hardness, color or preform.
“At Dow, we continue to identify ways to address key global market requirements and accelerate innovation and sustainability throughout the rubber and plastics industry,” says Zimmer. “The downstream technology investments recently completed at our plant in Barry, United Kingdom exemplified how Dow seeks better ways to serve our customers through increased SILASTICTM production capacity, while also enabling more consistent, reliable, and productive production lines.” The company says that these fluorosilicone technologies expand the toolbox of automotive designers by providing additional options for material selection and performance. As under-thehood temperatures continue to increase, fluorosilicone elastomers are being asked to deliver performance in temperatures not previously required or encountered for such applications.
This new high temperature FSR technology can now meet many of these evolving temperature requirements. An improved compression set resistance fluorosilicone technology now enables better sealing and durability for applications requiring fuel and automotive fluid resistance. The lower compression set of a material can result in higher sealing force retention over the life of the application, ultimately resulting in better durability. Craig Gross, Senior AETS Specialist, Silicone Elastomers said in an earlier interview with
AI: “Previously limited in use to applications up to 200°C, we developed FSR technology to deliver good retention of physical properties when exposed to temperatures of 220°C with excursions up to 240°C. The second technology recently developed improves the compression set resistance of fluorosilicone elastomers and achieved singledigit compression set values when tested for 22 hours at 177°C. Both of these new technologies can be incorporated across a wide durometer range.”
Automotive Industries (AI) asked Zimmer to expand on the use of SILASTIC™ to reduce the carbon footprint of vehicle manufacturing. Zimmer: Silicones can play a critical role in increasing the sustainability of components and helping manufacturers comply with en- vironmental regulations.
These materials are also helping to support mainstream adoption of electric vehicles and autonomous vehicles, which reduce or avoid fossil fuel consumption and carbon emissions. In addition: • Silicones, including UV-cure grades, are frequently solventless, making them the material of choice where emerging regulations impose complex and costly special handling and processing requirements. Innovative material suppliers also offer more-sustainable solvent-based options to meet customer needs.
- Advanced silicone materials that cure at lower temperatures or with UV light can help reduce energy use and accelerate throughput high-throughput electronics modules.
- Silicones’ reliability over time and under aging helps extend product life and avoid premature obsolescence.
- Silicone materials help extend the life of batteries in electric and hybrid vehicles, which can play a role in consumer adoption. By improving thermal management, reliability and cost-effectiveness of these batteries, silicones help to support growth of the e-mobility market.
- Silicone based materials are also light weight since density of polydimethylsiloxane polymers is close to 1.0 g/ml.
AI: What is your prediction for the growth of the use new materials in the future of automotive manufacturing? Zimmer: In transportation, the growth of electric vehicles and the proliferation of automotive driver assistance sensors require solutions to meet safety and reliability requirements while achieving efficient throughput in mass production. Silicone-based materials help designers and engineers meeting performance and regulatory requirements in the most demanding applications.
Thanks to their versatility and performance-enhancing capabilities, silicones can be found in virtually every area of automotive system assemblies, from powertrains and engine sealants to electronic control modules, novel lighting systems and safety features. For example, silicone materials for EMI shielding can play a key role in ensuring reliable performance over the product lifetime of critical applications like radar, cameras and electronic control units (ECUs).
More Stories
Automotive Industries (AI) Newsletter April 2025
GlobalLogic Pioneering Software-Defined Vehicles, AI Innovation, and Sustainable Solutions for the Future of Automotive Mobility
Cybord TCI – The Future of Manufacturing Integrity