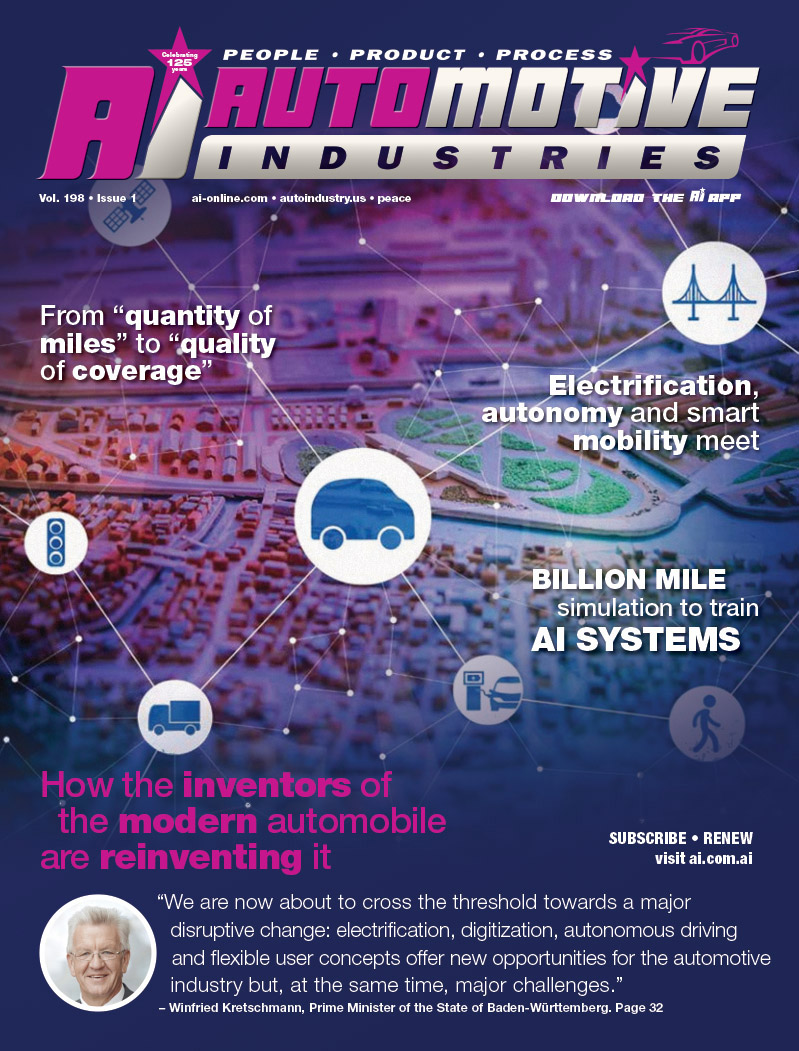
Polypropylene (PP) compounds are currently the fastest-growing polymer material in the automotive industry.
Their inherent advantages – including low density and recyclability – make them the material of choice for automakers aiming to produce vehicles that are lighter, and more energy efficient, and therefore more sustainable. “In a future in which electrification, autonomous vehicles, and mobility as a service may prevail, PP compounds are enablers for change,” says Nicholas Kolesch, Borealis Head of Marketing, Automotive.
Borealis provides services and products to customers in collaboration with Borouge, a joint venture with the Abu Dhabi National Oil Company (ADNOC). The companies are upping production to meet the growing demand. Capacity of the Borouge Shanghai compound manufacturing plant, which went on stream in 2010 with an annual capacity of 50,000 tons, is being increased to 125,000 tons a year. Borealis has also opened a new PP plant in Taylorsville, United States.
The facility adds an initial 66 million pounds of capacity to strengthen Borealis’ and Borouge’s supply capability for thermoplastic olefin (TPO) and shortglass fiber (SGF) compounds. Borealis has teams of experienced technical experts in all regions to work with OEMs to define material specifications. Starting with the vehicle development and pre-launch phase they work with OEMs and designated Tiers on part tooling, ensuring optimal performance in the critical intersection of material, tool and processing. The company has innovation and application centers in Linz, Austria, Itatiba, Brazil, Taylorsville, USA and Shanghai, China.
Automotive Industries asked Kolesch to share Borealis and Borouge’s product development strategy.
Kolesch: We are in one of the most dynamic periods in the automotive history. While our primary focus remains on vehicle weight reduction to support lower energy consumption, our innovation efforts are also responding to creating the material solutions needed for electrified and autonomous vehicles. We are also developing products with recycled content in automotive applications. AI: How do products like Fibremod™ help in the lightweighting of vehicles?
Kolesch: Our Fibremod family of glass and carbon fiber-reinforced compounds can be used as substitutes for parts traditionally made with engineering plastics and metals. Polypropylene is one of the lowest density plastics available, and with the right fiber reinforcement the needed stiffness, strength and impact resistance can be achieved. By foaming our Fibremod glass fiber compounds, even further density reduction is realized. Each gram of weight saving counts: When you save 100 kg of vehicle mass, the fuel consumption is reduced by approximately by 0.4 l / 100 km, or by 10 grams of emitted CO2 per kilometer. Therefore, decreasing the vehicle weight by 1 kg means 0.1 g/km of CO2 emissions less, or a penalty saving of 9.50 EUR (based on EU legislation mandating emission reduction targets for new cars in 2020 of 95g/km).
AI: What makes Fibremod™ Carbon such an innovative material?
Kolesch: Fibremod Carbon marries an extremely low-density fiber with the lowest density polymer. We have products with carbon fiber content from 6% to 40% – and we can customize a compound with optimal carbon fiber loading. The products are made cost-effective through the utilization of second-use carbon fiber. We are also investigating the use of recycled carbon fiber. Fibremod Carbon body panels utilize Borealis Borstar base resins to achieve needed impact resistance. This application opened up a new challenge: achieving a class-A painted surface. Working with our customers and paint suppliers we have realized this goal in a number of concept studies. The ultra-low CLTE of Fibremod Carbon also supports the achievement of zero gap for panels fitted next to metal parts.
AI: What are the new Fibremod Carbon grades?
Kolesch: Borealis has two low-density additions to the Fibremod Carbon portfolio: Fibremod™ CG210SY, containing 20% carbon fiber; and Fibremod™ CD211SY, a hybrid concept made with 10% talc and 10% carbon fiber. Advantages include:
- Improved surface appearance and better dimensional stability
- Unsurpassed stiffness and durability
- Good paint adhesion and high flowability The grades are intended for use in structural parts and body panel applications, including fenders and tailgate skins, structural interior applications with complex geometry, and for class-A painted surfaces. Additional grades with enhanced surface aesthetics are currently under development for use in painted and unpainted parts.
AI: What about applications in electric and hybrid vehicles?
Kolesch: The Borealis portfolio of Daplen and Fibremod solutions offer much more than weight reduction. Fibremod compounds can be used in structural applications, including frontend modules, tailgates, novel seat structures, and the “front trunk”. Interior appearance, surface effects and haptics will also change as the vehicle interior takes on new functions. Here the Borealis Daplen™ portfolio of TPO compounds enables the development of class-A surfaces and translucent effects, while providing superior incar air quality. Versatile materials like Daplen™ EE058AI reduce the manufacturing complexity of interior components.
A good example is the new Skoda Scala where Daplen™ EE058AI is found in the door panels, glove compartment, center console and instrument panel. Another example is the Chinese NIO ES8 SUV. Borealis Fibremod™ CB201SY is used to produce the ES8 electric SUV centre console carrier of the vehicle. Fibremod™ CB201SY offered a 10% weight saving when compared to PP LGF40. The part also offers a very useful and unique design feature in the form of a storage space in the centre console. This grade is one of five different Borealis and Borouge products found in many applications on the NIO ES8. Plastics also play a key role in the powertrain of electric vehicles. We are working on a number of solutions for e-vehicle batteries and associated applications, including flame-retardant properties.
Borealis Fibremod solutions are being explored for use in parts of the battery itself, such as cell trays and housings. In addition, polyolefin materials are used to produce microporous permeable membranes that separate anodes and cathodes in lithium ion batteries. Polypropylene films are also a critical component in capacitors that transform the direct current from the battery into alternating current for the motor. EVs and traditional internal combustion engine vehicles can contain up to a kilometer of wires and cables of different types. Halogenfree polypropylene wiring solutions are a safe and high strength alternative across the operating temperature range of an EV.
AI: What other products are being developed to help reduce EV vehicle mass?
Kolesch: Borealis Daploy™ products are used in numerous automotive applications including roof liners, moisture barriers in door modules and lightweight air ducts, where they replace rigid PE materials. PP products combine both high melt strength and extensibility in the melt phase. They open up the possibility of bringing the numerous well-known property benefits of PP into the world of low-density polymeric foams. These benefits include lower weight, a wide mechanical property range, high heat stability, good chemical resistance, and easy recyclability.
AI: How does your company’s PP portfolio help promote the circular economy?
Kolesch: As the first major polyolefins producer to sign the New Plastics Economy Global Commitment, Borealis fully supports the vision of a circular economy for plastics. Under the EverMinds™ umbrella Borealis is extending its Borcycle™ range of recycled polyolefins (rPO). The move enriches the company’s existing virgin polyolefin portfolio with circular solutions for a broad range of applications. Borealis is helping to increase the share of recycled plastics in vehicles by developing polyolefin-based solutions composed of both virgin and post-consumer recyclate (PCR) content. In 2014, Borealis was one of the first virgin polyolefin suppliers to launch a range of dedicated polypropylene (PP) compound solutions including PCR for use in automotive applications under its Daplen™ brand. The offering includes three proven high-quality compounds that have been rebranded as Borcycle™ ME2220SY, Borcycle™ MD2550SY and Borcycle™ MD3230SY. Specific customer benefits:
- Equivalent performance to products containing only virgin polypropylene
- Readily available to a consistent high quality, allowing for high-volume production
- Supports OEMs in achieving their sustainability goals through use of post-consumer recyclate.
There is also full support from the Borealis technical service, and modelling and simulation teams to bring these virgin PP grade substitutes into serial production.
More Stories
GlobalLogic Pioneering Software-Defined Vehicles, AI Innovation, and Sustainable Solutions for the Future of Automotive Mobility
Cybord TCI – The Future of Manufacturing Integrity
Meet Rita Case – recipient of 2024 NAMAD Lifetime Achievement Award