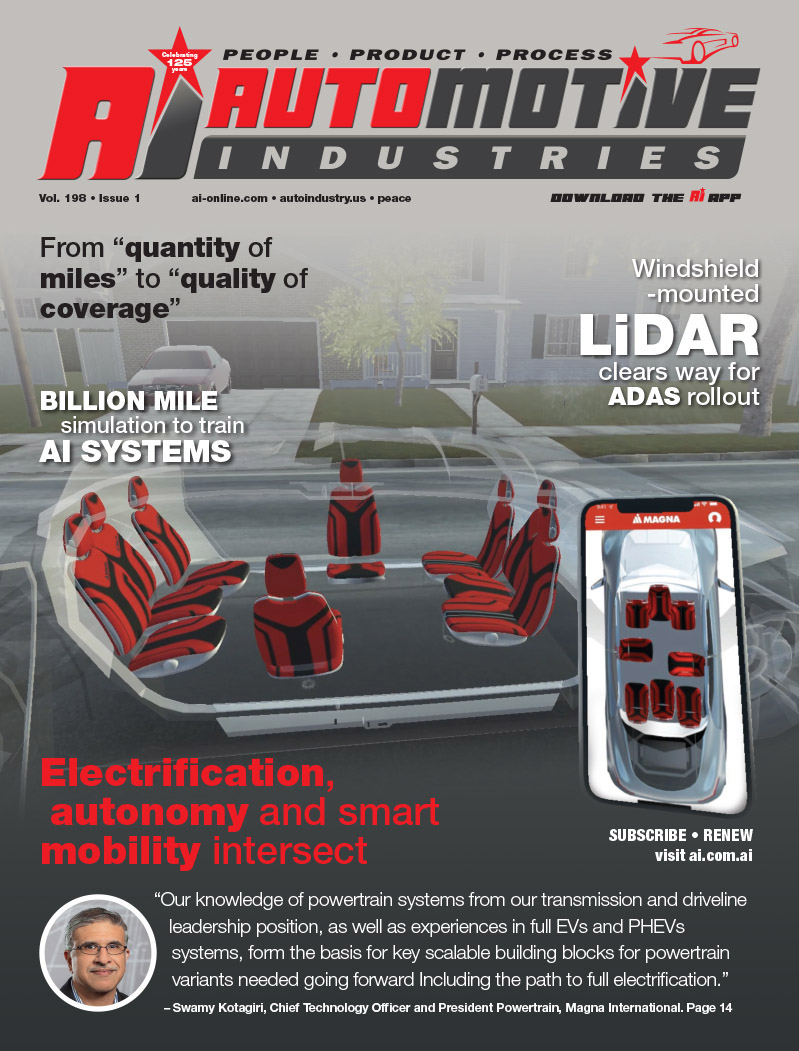
Even if global market penetration by pure electric vehicles exceeds 25% by 2025, there will still be a huge demand for conventional hydrocarbon-fueled engines. Existing Tier suppliers into the auto industry have to balance the need for ever more efficient internal combustion engines and that for new e-mobility technology.
Automotive Industries (AI) asked Horst Binnig, CEO, Rheinmetall Automotive, how the company is preparing for the increasing electrification of the power transmission.
Binnig: At present we are primarily a combustion engine business. Where analysts and investors previously focused on the next quarter results, or the year-end results, now they are looking at a time when there will be no combustion engines. What we tell them is that this is more than a decade away. We’ve done really deep dives and complete scenario analysis of the trends.
The result of our analysis is that at most 20 to 25 % of the new vehicles sold will be electric vehicles by 2025. The main driver of this will be China, where legislation is driving the business model. The government wants pure electric vehicle penetration to be at least 12% by 2020. That will make a dramatic difference to the global ratio of electric vehicles to those driven by combustion engines.
But, if you assume that 25% of vehicles in 2025 will be pure EVs, then equally 75% will have conventional engines. So, we are focusing on both. We retain the production of combustion engine components such as pistons and engine blocks, but 40% of our product portfolio already consists of products fitted with a sensor or actuator. We are keeping in step with the industry’s journey through hybridization / electrification of the car with all the auxiliary elements up to a pure EV.
AI: What systems are you developing for electro mobility?
Binnig: For us e-mobility creates a big field of opportunity for the future due to our complete product range. Our systems go from hybrid to range extender to electric vehicle. We are developing a new kind of modular battery pack as well as a 90kW electric powertrain, which is a highly complex product. Both systems are currently being integrated into a test bed based on a subcompact vehicle.
For most people the prime concern about an electric vehicle is range anxiety. That is why we are offering a complete range extender. In addition to that we already have orders from big customers in China for the aluminum housing of an electric motor. The casting weight for the e-engine housing is the same as that for a four-cylinder combustion engine. And then you have to cool down or heat up the engine and of course the battery. If it is -10C and if the battery is cold you might have problem with the range. You must have thermal management.
AI: Are you focusing your efforts on both electric drive and energy storage/battery pack?
Binnig: We have some core competences. While we don’t know much about connectivity, we can manage thermal circuits connecting the battery or engine. This is close to our current core competences. We already have orders for our battery trays, which are a combination of aluminum and protective parts. We have the knowhow from our defense business and are integrating the complete thermal management. On the engine side we are trying to build up our e-engine knowhow. That’s what we did with the 90kW engine. In addition we are focusing on our core competences on the drive side and thermal management.
AI: What is your goal?
Binnig: If you look at the scenario up to 2020 and even 2050 most of the cars will be with internal combustion engine. Pure gas and diesel will be only 10%, but all those hybrids will still have a combustion engine on board. Our goal is to supply all parts of the business. If we look at our vision for 2025, the components needed for efficiency and for reducing fuel usage and CO2emissions are essentially part of our present product portfolio. For electrification, we have products for hybridization and e-mobility. The new technologies we are working on are engines for e-bikes, 3D printing and other technologies that we believe will account for a third of our production and sales.
AI: Which class vehicle are you targeting?
Binnig: It is the A and B Class, the smaller cars and the micro cars. If you look into the future, if we assume that we will have zero emission, then we have to think about Amazon deliveries and the missing link beyond e-bikes or pedelecs. I think we would be stretching ourselves too far to move into providing complete axles or drive trains – which would also bring us into competition against the OEMs and other Tier companies where it is their core competence. We are targeting the smaller cars in the e-mobility sector, but the whole market for our thermal management and batteries. Our technology is not limited to the smaller cars. Drive – small, thermal management – everything.
AI: What can you offer to the new OEMs for which electric drive is not a priority?
Binnig: We can develop the complete drive train for them including battery management, the battery itself and the motor. All we can’t do is the CPU.
AI: Will electric mobility change our driving habits?
Binnig: E-mobility is not just a way to go from A to B. People have to recognize that it’s fun to drive an e-car, and of course they can do so without polluting the environment. And if you combine it with autonomous driving and car sharing than we will have much more excitement in the next five years that we had in the past 100 years.
AI: How important is it to have a lifetime volume partnership with OEMs?
Binnig: We have both lifetime contracts and single source contracts with OEMs. In the future e-mobility, particularly in the drivetrain, will be a kind of commodity. This opens up the opportunity for the OEMs to a number of suppliers for the same products without awarding a lifetime contract. They will tell you “as long as you are competitive you have the order”.
AI: What is next for Rheinmetall Automotive?
Binnig: We have strong growth prospects in both the defense and automotive sectors. Our biggest challenge is to get the right people on board. It makes no sense to have the orders but not to have the engineers. For us is important to get on board people who think differently. Engineers who don’t think diesel and gasoline, but think about connectivity.
The main driver behind changing the name of the company to The Rheinmetall Group was to attract them. We will grow our business, we will expand our combustion engine business and we are stepping into the opportunity the OEMs are giving to us because they are focusing their activities on e-mobility. We strongly believe in the combustion engine being a strong business for years to come. In addition we are allocating a large part of our resources to the emerging e-mobility sector.
More Stories
Mosaic Click board from MIKROE delivers global coverage multi-band and multi-constellation tracking ability
Current transducer from Danisense selected for DC charging station testing device demonstrator at TU Graz
New Click board from MIKROE helps develop and train ML models for vibration analysis