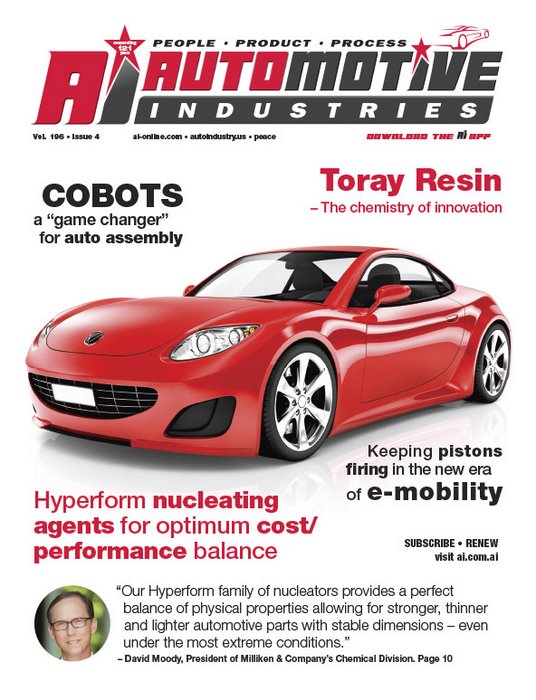
Lighter and stiffer polyolefin components are helping OEM designers to reduce weight and emissions while improving productivity and the level of quality experienced by the customer.
One of the leaders in the development and manufacture of the nucleating agents behind the new generation of polypropylene components is the South Carolina headquartered Milliken & Company.
Milliken Chemical, a division of Milliken & Company, has a number of technologies specially formulated for the automotive industry. Its Hyperform® family of nucleating agents allows auto manufacturers and compounders to produce consistently high-quality products within a variety of polyolefin applications. Global Product Line Manager, Bhavesh Gandhi says “Our Hyperform® family of products not only allow compounders to formulate their product to meet stringent specifications set by automotive OEMs, but also allows Tier I suppliers to optimize their processing conditions to achieve maximum productivity benefits resulting into optimal cost / performance balance.”
Hyperform HPN-20E allows manufacturers to meet required part specifications while improving manufacturing speed, thanks to the additive’s unique shrinkage characteristics, physical property balance, and crystallization effects. Final products feature a superior stiffness and impact balance, as well as optimum coefficient of linear thermal expansion (CLTE) performance.
Automotive Industries (AI) asked David Moody, President of Milliken & Company’s Chemical Division, how market demand for Hyperform is growing.
Moody: Adoption of the technology has been tremendous. US, Japanese, Korean and European OEMs have adopted this technology for their existing as well as future car models. The Hyperform family of products allows OEMs the flexibility in part design needed to meet technical requirements to achieve best quality parts with low tolerances. Hyperform nucleators provide a perfect balance of physical properties allowing for stronger, thinner and lighter parts with stable dimensions even under the most extreme conditions.
AI: What are some of the features of the different variants of Hyperform that make them unique?
Moody: Let us talk first about Hyperform HPN-20E. It induces lower and more isotropic shrinkage in polypropylene. That means parts shrink minimally and remain flat. In both extreme hot and cold conditions Hyperform nucleated parts change their dimension minimally, meeting the high tolerances required of exterior parts. Hyperform HPN-20E also provides a better balance of stiffness and impact strength enabling automotive compounders to formulate their product with much more flexibility.
On the other hand, Hyperform HPN-68L has industry-leading crystallization kinetics, which enables manufacturers to improve productivity while maintaining dimensional stability. One of the unique features of Hperform HPN-68L is pigment leveling. Using HPN-68L customers can achieve the same final part dimension irrespective of the pigment color used.
AI: What are the advantages of your newly-introduced DeltaMax™ polypropylene performance modifiers?
Moody: Our DeltaMax Performance Modifiers allow Tier 1 automotive suppliers to increase both the melt flow and impact strength of the ICP resin or PP compound without sacrificing other physical properties of the plastic such as stiffness and scratch resistance. These improvements expand the performance boundaries of polypropylene and satisfy emerging safety and consumer trends related to improved impact resistance, light-weighting, and soft-touch interiors. Additionally, the performance improvements are significant enough to allow the use of post-consumer and post-industrial recycled polypropylene materials which helps the industry improve its sustainability profile – a characteristic that is part of our core at Milliken.
AI: Are there any other new Milliken technologies for the automotive industry?
Moody: Yes, Milliken has recently developed Hyperform EXP-715. This novel technology addresses the increasing demand for improved stiffness/impact balance in polypropylene resins used in rigid automotive and appliance applications. Specifically, Hyperform EXP-715 allows for the highest stiffness in polypropylene, superior thermal stability through improved heat deflection temperature and faster nucleation performance. These attributes result in material savings via downgauging of plastic parts, more sustainable end products, enhanced physical and thermal properties of polypropylene.
Milliken also manufactures additives for polyurethane foam applications in the automotive industry. The Milliguard UVX200 HF UV absorber for polyurethanes received the 2016 InnoVision Award for excellence in Technology Integration. The Milliguard® AOX-1 novel polymer-bound antioxidant for polyurethane (PU) addresses more-stringent environmental, health and safety requirements, while delivering outstanding thermal stabilization performance at low loadings.
AI: How has the Milliguard range of products helped automotive manufacturers meet environmental standards?
Moody: Milliguard additives for polyurethane foam are used to prevent degradation breakdown of the polyurethane which releases volatile chemicals. Additionally, our additives – unlike competitive technology – do not contribute to emissions because they are designed to become part of the polyurethane component by chemically binding to the structure. Vehicle indoor air quality standards today are targeting both an improvement in total VOC as well as reduction in specific chemicals. The Milliguard family of additives is helping to reduce these specific targeted volatile chemical emissions from polyurethane without adding to the total VOC content of the foam.
AI: Walk us through the research and innovation that went into the development of the latest Milliguard AOX-1 antioxidant.
Moody: A market need existed for better antioxidant technology for polyurethanes that would not contribute to chemical emissions, and would work efficiently while not contributing some of the negative effects of legacy antioxidant technology used in polyurethane. Milliken utilized its core competency in polymer chemistry to help design Milliguard AOX-1 to meet the requirement.
AI: Tell us a little about your non-chemical automotive business – such as your Autovation products.
Moody: Our Autovation business is well positioned to solve challenging automotive acoustic requirements at lighter weights than our competition. We offer our customers nearly all nonwoven products for the automotive market and utilize our rapid prototyping and breadth of in-house testing to ensure performance and quality. We are also able to customize products to meet the most challenging requirements in the industry.
AI: What patent-pending technologies are in the pipeline there?
Moody: We are building on the inherent advantages of nonwoven products by creating product and process IP to eliminate the inherent disadvantages of nonwovens. We have numerous patent pending technologies focused in the automotive nonwoven space for interior and exterior components. For example, our TravelToughTM technology takes advantage of the acoustic performance for exterior components (wheel well or underbody shield) while also reducing the moisture uptake by a factor of six and preventing ice from attaching to the surface – which can cause damage to components and the breaking system. We also recently launched our MaxQuietTM technology, which enables significantly improved acoustics at lighter weights.
AI: How much of your automotive business do you see coming from the non-chemical products in the future?
Moody: For the chemical and non-chemical segments we continue to invest in capabilities specific to the needs of the automotive sector. For our non-chemical automotive business, our supply chain, capacity planning, forecasting tools, ISO & TS certifications, and investment plans all coupled with our world class safety and manufacturing performance will continue to help us drive success in the automotive segment. We are committed to the industry and have strong company-wide synergies we can leverage.
More Stories
Sonatus – The industry is shifting gears to software
Cybord warns of dangers of the stability illusion
HERE building trust in ADAS systems