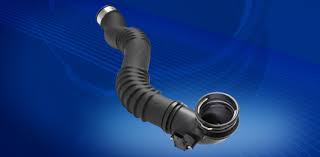
Vehicle manufacturers and Tier suppliers are transforming the essence of the industry from being manufacturers and distributors of vehicles to suppliers of mobility solutions.
“Within two to three decades mobility will be defined by sustainability, connectivity and automated driving. Innovations will be more important than ever going forward – especially since premium vehicles with strong emotional appeal depend on them,” said the recently retired Klaus Draeger, member of the Board of Management of BMW AG, who at the time was responsible for Purchasing and Supplier Network, at the 2016 BMW Supplier Innovation Awards.
Among the innovative suppliers honored was Röchling Automotive, which received the BMW Supplier Innovation award 2016 for the development of the Active Grille Shutter of the BMW 7 Series. In its accolade to Röchling, BMW says the “Active Grille Shutter makes air grilles visible for the first time, allowing the customer to witness aerodynamics directly. Integrating the flaps into the BMW kidney grille creates a striking optical effect. Electric controls actively regulate the air stream.
The improvement over previous systems is impressive: Air resistance is optimized, CO2 emissions reduced and the engine warms up faster from a cold start”. Röchling Automotive also developed a second active grille shutter below the kidney grille, as well as the major part of the undershielding for the BMW 7 Series to accomplish the required aerodynamic targets.
Röchling Automotive, with more than 4,700 employees globally, has positioned itself as such a partner of OEMs for integrated system solutions in the areas of aerodynamics, powertrain and new mobility. “With 39 locations on four continents, we are positioned globally. Our engineers, located in four engineering centers globally, are working with almost all vehicle manufacturers solving the challenges of the automotive industry to reduce emissions, weight and fuel consumption” says the company. Over the past year it has also received awards from Ford, General Motors, FCA and Nissan Motors.
JV with Japanese company Starlite
Röchling Automotive has signed a joint venture agreement with the Japanese company Starlite, an Osaka-based manufacturer of automotive parts and industrial products. The sales and development joint venture came into force on September 1, 2016, and will be subsequently converted into a production joint venture, according to the two companies.
“Starlite has been our partner in Japan since 2008. We have a history of a very positive, fruitful, and trusting cooperation,” says Gerhard Neidinger, Executive Board member of Röchling Automotive and Head of the Asia region. The partnership with Röchling Automotive has led to the company supplying many leading Japanese automobile manufacturers with active grille shutters, windshield cowls, degas bottles, and SCR tanks.
“Whether it be Mazda, Nissan, Honda, Subaru, Mitsubishi or Toyota – the previous sales cooperation with Starlite helped Röchling Automotive provide quick and reliable support to Japanese car manufacturers locally. In the future, plastics products for the Japanese automotive industry will also be jointly developed and manufactured,” said Neidinger.
Commenting on the agreement Takamitsu Saigo, Chief Executive Officer of the Starlite Group, said “in the automotive area, our company relies on innovations that contribute to reduced emissions, weight and fuel consumption. With Röchling Automotive and its technologically superior plastics applications, we have found the perfect partner here”. Starlite is represented at 12 locations in Japan and at six locations outside of the country. Röchling Automotive has grown rapidly in Asia in recent years, primarily in China. It has five manufacturing sites in Asia. The company is the market leader for active air flaps, and is one of the leading intake manifold manufacturers in China. “The founding of our first Japanese joint venture underscores the significance that the Asian market has for us,” says Erwin Doll, President & CEO of Röchling Automotive
Technology focus
Röchling Automotive is focusing on innovation in three rapidly-growing areas: aerodynamics, powertrain and new mobility. Jürgen Peters, President, Röchling Automotive NA LLC, expects group sales to soon exceed $1 billion (USD), with a large part of the growth taking place in the North American region. To meet the growing demand for its products in North America, Röchling Automotive is expanding its manufacturing capacity in Silao, Mexico, as well as expanding its office space in Duncan, South Carolina and at its Technical Center in Troy, Michigan.
Aerodynamics
The BMW Visible Active Grille Shutters are one of the company’s latest innovations to go into series production. Röchling Automotive develops various kinematics for Active Grille Shutters ranging from vertical flaps (like on the BMW 7 Series AGS), to horizontal flaps integrated into the design grille. They are almost completely invisible when open.
New solutions for reducing drag by the underbody of a vehicle range from low cost solutions such as Seeberlite Mono to advanced solutions with premium acoustics and self – extinguishing or even non-burning properties. Wind tunnel tests show that the reduction of turbulence under a vehicle also helps improve road-holding and therefore safety.
Powertrain
Röchling Automotive is rapidly expanding its market share in the field of SCR tanks and filling systems worldwide. The system supplier creates robust solutions for diesel vehicles. Odorless filling systems have been developed for the European and Chinese markets. Innovations by Röchling include a metering module which ensures that the solution is automatically thawed and warmed at low temperatures. Distracting sloshing noises are minimized by the design of the injection-molded tanks.
In the field of charge-air ducts required for the quickly increasing number of turbocharged engines the company has introduced a new grade of polyamide material that can withstand sustained temperatures of more 230°C .
New Mobility
In the field of new mobility, Röchling Automotive is in series production of battery housings, as well as cell frames for lithium-ion type batteries.
Weight can be reduced by replacing traditional materials used for body parts with a range of compounds of Röchling’s Stratura reinforced material. Röchling Automotive’s integrated sandwich floor (ISF) utilizes its functional multi-layered construction to integrate the single layers of traditional carpeting, acoustic material, metal car body, and underbody panels. The result is a solution that not only provides significant weight reduction, but also delivers improved acoustic and thermal comfort.
Injection molding
Röchling Automotive is the first to combine the use of an injection molding compounding (IMC) with integrated MuCell technology to lower the weight of components
More Stories
Marelli to Showcase Latest “Speed-to-Market” Innovations at Auto Shanghai 2025
Unique Vacation Experiences for the Car Enthusiast
Mecum Auctions Sponsors Monterey Motorsports Festival for Car Week