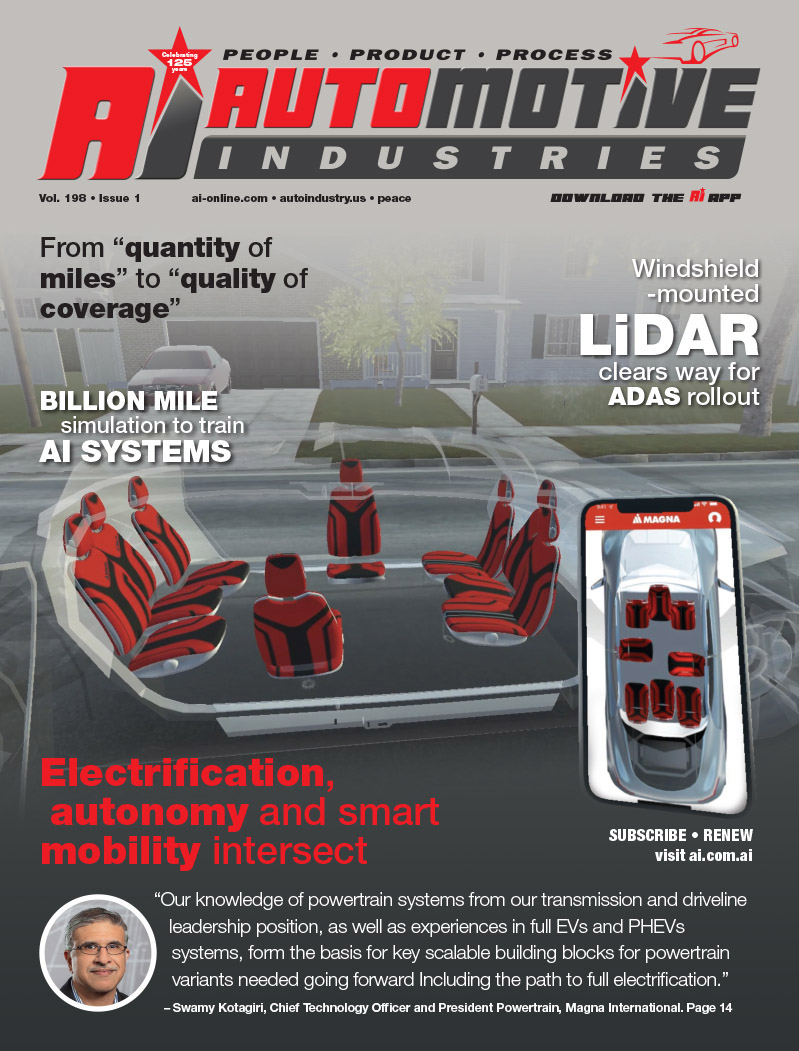
With the demand for automotive aluminum accelerating in the U.S., Linde LLC is focusing its global expertise in oxyfuel technology on improving both the casthouse processing and heat treating of aluminum and aluminum alloy products.
At the Aluminum Show 2015 in Detroit, November 11 and 12 (booth #1237), Linde will introduce advanced Linde Low-Temperature Oxyfuel (LTOF) technology for remelting aluminum, and highlight research into the Linde Direct Flame Impingement (DFI) process which uses oxyfuel to assist in the heat treating of aluminum sheet.
Secondary aluminum processors serving the automotive industry can quickly improve productivity with Linde LTOF technology, which can be installed or retrofitted to virtually any aluminum remelt operation to improve fuel efficiency, boost melting rates, and reduce the generation of nitrous oxides (NOx) associated with air-fuel combustion.
“We developed Low-Temperature Oxyfuel technology to meet the challenge of maintaining or increasing remelting rates with high levels of solid charge materials, typical of secondary aluminum operations in the U.S.”
-Tony Palermo, Program Manager, Metallurgy, Linde LLC
For continuous annealing and solution heat treatment of aluminum sheet, Linde REBOX(®) DFI technology, now in commercial development, retrofits to the annealing section of the line and could significantly boost throughput rates for the annealing furnace. Linde presented results of DFI heating conducted at its European test laboratory at TMS 2015 in March.
Aluminum Sheet Annealing
While aluminum currently enjoys about a 73 percent share, by weight, of the casting market in 2015 vehicles, aluminum sheet for auto and truck bodies represents the highest growth area for aluminum in the auto industry.( ) An aluminum autobody can reduce vehicle weight about 30 percent, and improve fuel economy about 20 percent.
Linde has been developing REBOX DFI technology for continuous annealing of aluminum sheet for several years. Because of aluminum’s low melting point and the restricted range for various types of heat treatments, temperature control is critical to sheet property and surface quality.
With Linde DFI technology, oxyfuel flames directly heat the metal strip. The process can achieve heat transfer rates up to 10 times higher than those for conventional fuel-fired furnaces. The Linde REBOX DFI technology has been boosting productivity of continuous steel hot-dip galvanizing and stainless steel annealing lines for nearly 10 years and millions of tons, with capacity increases in excess of 25 percent.
According to a survey by Ducker Worldwide, the overall demand for aluminum for NAFTA-produced vehicles is projected to increase by 56 percent leading up to the 54.5 corporate average fuel efficiency (CAFE) U.S. standard for 2025. Aluminum is about one-third lighter than steel, and reducing the weight of a vehicle by 10 percent means about a 7 percent improvement in fuel economy for the life of the average vehicle.
Boosting Secondary Aluminum
Characterized by lower flame temperatures, Linde LTOF technology enables more uniform heating than other combustion techniques, as well as the increased radiative heat transfer efficiency typical of oxyfuel combustion. Uniform heating also reduces incidences of localized overheating, which has been associated with yield loss.
“Recycled aluminum feedstock will be increasingly critical to meet demand, so this is a win-win-win for auto companies, aluminum companies, and the environment,” Palermo said.
In Europe, aluminum scrap is sometimes added to an adjacent primary melting operation in the casthouse. Linde has documented a 60 percent increase in aluminum remelting capacity and a 50 percent reduction in fuel consumption at such a 130,000 metric ton per year facility in Norway using Linde LTOF technology. Most aluminum remelting plants in the U.S operate remelt furnaces with, or close to, 100 percent solids in the charge. Use of LTOF technology is low capital method to increase throughput for casthouses processing solid charge feedstocks.
About Linde in North America
Linde LLC and Linde Engineering North America Inc. are members of The Linde Group. In the 2014 financial year, The Linde Group generated revenue of USD 17.9 bn (EUR 17.047 bn), making it the largest gases and engineering company in the world with approximately 65,500 employees working in more than 100 countries worldwide. The strategy of The Linde Group is geared towards long-term profitable growth and focuses on the expansion of its international business with forward-looking products and services. Linde acts responsibly towards its shareholders, business partners, employees, society and the environment – in every one of its business areas, regions and locations across the globe. The company is committed to technologies and products that unite the goals of customer value and sustainable development.
Linde provides industry-leading portfolio solutions for the ferrous and non-ferrous metallurgy industries, ranging from gases and equipment to process consulting and services. For more information, contact Linde (www.lindeus.com), 800-755-9277.
For more information, visit www.lindeus.com
More Stories
Accelerating The Development of Hydrogen Vehicles & Infrastructure – Europe’s Biggest Players Meeting at Premier Event
Automotive IQ Announces the 15th Annual Automotive Functional Safety Week 2025
Major Automotive Companies to Share Latest Developments in Steering, Braking, Chassis and Suspension Systems at Premier Industry Event