
Continental is harnessing the power of information technology and the cloud in order to help OEMs improve service levels and productivity at dealer franchise level.
Workshop technicians daily face the challenge of analyzing complex systems and performing the required repairs. The crucial success factor is the optimum communication between the technician and the vehicle. This is where Continental’s new software and hardware diagnostic solutions step in. Continental’s integrated portfolio of diagnostic tools combines technical expertise with intuitive, easy-to-use solutions focusing
on the needs of workshop technicians in the franchised aftermarket. The combination of diagnostic tools, technical instructions and manuals is designed to help increase workshop efficiency. It offers OEMs an innovative full-range solution for successful workshop service activities.
Workshop-oriented diagnostic solutions
Under the name “Continental Techcenter,” the product range for franchise dealers offers a portfolio of six modules that can be configured by OEMs to meet specific needs:
- Techcenter Essential combines Techcenter’s core diagnostic modules and provides users with simple, intuitive interfaces to allow them accessing all the fundamental diagnostic data
- Techcenter Genius is the intelligent fault-finding module. It links vehicle data to symptoms as well as to diagnostic and environmental data in order to determine possible causes of
error. One outstanding feature is the software algorithm that is able to take account of regional empirical and environmental data in its calculations and learn from this. Workshop technicians in the global network of franchised dealerships are able to view this error diagnostics – harmonized to take account of regional circumstances and prioritized in order of probability – and can immediately start looking for the cause of the problem at the most likely points.
- Techcenter Programmer is a module for the programming and configuration of control modules in the OEM’s service bay. Its functions include, for example, reflashing or configuring electronic control modules.
- Techcenter Service gives workshop technicians access to simple, step-by-step instructions as well as to integrated diagnostic communications during the conduct of complex maintenance tasks
- Techcenter Data provides technicians with all the information required for vehicle diagnostics without them having to consult separate information sources such as printed instructions. Assembly instructions and short films can be used to assist in the resolution of problems.
- Techcenter Product Manager provides functions for the administration of the diagnostic software. Here it is possible to define which diagnostic modules are available at which workstation and when.
When correctly used, the solutions of the Techcenter support automotive manufacturers during diagnostic, repair and process planning operations. This cuts the costs to OEMs and, by increasing process reliability, benefits customers. It should also be possible to integrate remote diagnostics, scheduling and supply chain management within a single system. The combination of software and hardware solutions also shortens process times. For example, fault codes and live data can be viewed together in real time. Furthermore, the new diagnostic system can generate a maintenance plan with precise timing specifications (95% accuracy) for the repair work immediately after reading the diagnostic data. As a result, the workshop finds out quickly how long a service will take and is able to give its customers reliable time estimates and optimize the use of workshop resources. Parts catalogues are also integrated in the system and further enhance workshop productivity.
The future: Cloud-based vehicle diagnostics
The diagnostics technology of the future will allow workshops to be in constant contact with the vehicles they service, to identify changes to controllers at an early stage, to perform remote diagnostic operations and to learn from their mistakes. One example here is a secure Continental Cloud system that permits the ongoing integration of new diagnostic and error data from participating OEM workshops in an online database. This crowdsourcing system, to which the OEMs and their authorized workshops around the globe have exclusive access, constitutes a wealth of data and experience.
Real-time repair aids
Augmented Reality (AR) is another innovation that will soon become an everyday reality for franchised dealers. Continental’s AR solution is a fully featured online information system which seamlessly integrates diagnostic and technical information in an intuitive, task-focused user experience. In this way, AR means that problems can be solved faster and more accurately in the workshop. As soon as the system identifies a vehicle, it is possible to read out the error memory. Using the Genius module, workshop staff can start troubleshooting and view the maintenance and repair requirements – on, for example, a tablet. The solution includes circuit diagrams, system descriptions and repair guidelines for all vehicle models. Videos illustrating the removal or installation of components step-by-step provide optimum support.
In the future, it will be possible to deliver these functions through data glasses so that technicians can move around unhindered and work more efficiently.
Continental’s core diagnostic portfolio is accompanied by both standardized and customized hardware solutions (e.g. vehicle communication interfaces, VCI) as well as by special service tools and owner Information:
- Special service tools permit accurate, simplified and faster vehicle repairs. Continental develops, manufactures and distributes the mechanical and electronic tools to meet the OEM’s individual requirements. The tools include cables and harnesses to permit fast, thorough diagnostics or the conduct of software updates.
- Owner Information is supplied to drivers in conventional form (e.g. manuals) and, in the future, will also be made available via new media. These will take advantage of formats such as QR codes. Animated explanations displayed on the central display of the vehicle’s instrument panel are also planned.
Dr. Michael Jörg Ruf is head of the Commercial Vehicles & Aftermarket Business Unit at Continental.
As a leading supplier to the automotive industry, Continental understands what car manufacturers and their partners in the service workshops need and offers a wide range of suitable solutions. Developed with the practical perspective of the workshop technician in mind, they are functional, state-of-the-art and intuitive in their use. The entire value added chain is represented via a globally active business unit using a system that takes account of the unique and specific characteristics of the various regional markets. With its new portfolio of diagnostic solutions, Continental has strengthened its position as a high-performance partner for the OEMs’ service activities.
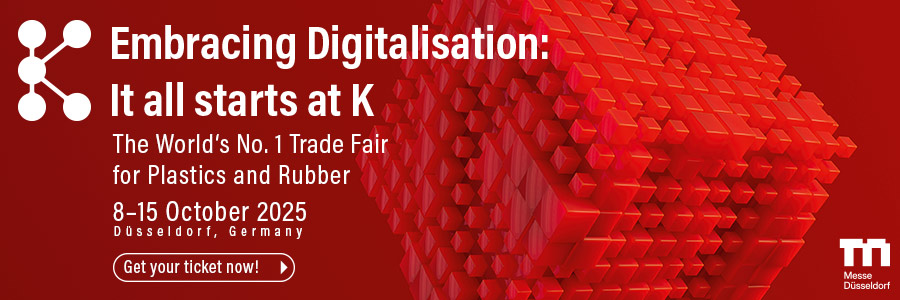
More Stories
Bangkok International Motor Show 2025 – The Talk of Sensuous Automotive
GlobalLogic Pioneering Software-Defined Vehicles, AI Innovation, and Sustainable Solutions for the Future of Automotive Mobility
Cybord TCI – The Future of Manufacturing Integrity