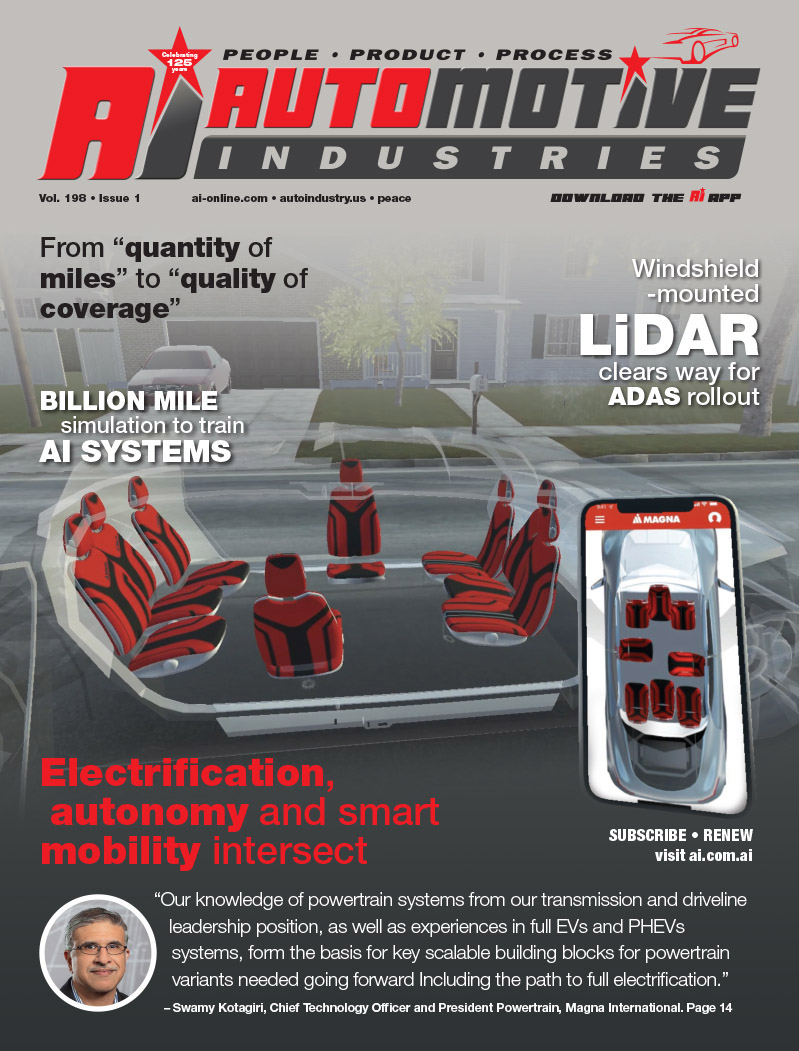
German-based vibration systems designer and manufacturer Anvis Group is on an expansion drive fuelled by the synergies created through the takeover of the company by Japanese company Tokai Rubber Industries (TRI).
In October 2014 TRI changed its name to Sumito Riko. Anvis Chief Executive Olaf Hahn says the change in name of the parent group signals the next step towards growth. The combination of words is made up of the globally known and trusted brand of the principal shareholder Sumitomo Electric Industries, and the Japanese word for physics, chemistry and technology ‘Riko’, which reflects the core areas of its service portfolio. The company focuses its efforts on automotive, ICT, infrastructure, living environment, medicine/care and health as well as environment and energy.
When TRI took over the Anvis Group in 2014, it wanted to leverage Anvis’ manufacturing footprint in Europe, NAFTA, Russia and China and its strong relationships with European OEMs. The Anvis Group is now recognized as a global market leader in vibration control components and anti-vibration systems in the automotive sector.
The Group’s Romanian arm recently opened a new production plant at Industrial Park South, in Satu Mare city in Romania. Anvis ROM S.R.L. currently produces 20 million pieces a year. Through the investment Anvis is expanding the local production capacities of anti-vibration products for the automotive industry. “The increased capacity meets the growing needs of our customers in the region,” says Hahn. Anvis ROM supplies clients such as the Renault Group, Audi, VW, Porsche and Daimler, all of which are shifting production to countries in Eastern Europe. The production area of plant has been almost doubled from 4,200 to 8,100 square meters.
“With the new plant, we are consequently continuing the growth path the company has started with the takeover by Sumitomo Riko last year. In addition to accommodating the changing market conditions, the plant has been constructed according to the newest process and environmental standards, so that the Anvis Group is also contributing to sustainability. Above all, the company is involved in social projects and collaborates with the Technical University of Cluj-Napoca,” he says. With more than 200 employees Anvis ranks among the main employers in Satu Mare. Another 100 jobs will be sustained by the expansion.
Anvis says it is creating the right conditions for growth through a forward-looking investment strategy. In the same street as the headquarters in Steinau, for example, a new building complex for development and testing is being constructed. “We are already in the process of hiring 25 new employees in order to handle the improved order situation,” says Hahn. Following the plant expansion in Mexico, and the new plant in Romania, production capacities are to be increased at Anvis’ sites in the Czech Republic and China.
Automotive Industries (AI) asked Hahn what the strategy was behind its global expansion.
Hahn: Carmakers’ localization strategies also influence global suppliers’ strategies since OEM production sites are served by regional suppliers. For Anvis, this means that production sites are being set up in all car manufacturing hubs around the world.
AI: How has the Sumitomo Riko (former known as TRI) takeover impacted Anvis?
Hahn: When it was taken over by Sumitomo Riko Anvis became a strong global player, assuming an important strategic role within the entire group. At the same time, Anvis is directly benefiting from the extensive R&D capacity and the sizeable manufacturing footprint outside of Europe.
AI: How has TRI managed to leverage Anvis’ network in across the globe?
Hahn: Since all OEMs in all the car manufacturing hubs around the world have development and manufacturing capacity the companies complement each other perfectly. As a strong global partner in the automobile industry we have introduced a strategic product portfolio for all leading OEMs.
AI: And how has your company benefited after the TRI takeover? What are some of the synergies between the two companies?
Hahn: As part of an international group we also have the potential to strategically shape the international market in the long term. Other synergies can be found in the use of extensive research, production technology and quality management. In return, Sumitomo benefits by gaining access to the European OEM market. Our tool, material and production technology is also very interesting to Sumitomo Riko.
AI: Tell us a little about the 2015 Sumitomo Riko Group Vision – is the group on track to meeting the targets of this vision paper?
Hahn: The Sumitomo Riko Group’s 2015 vision is to ensure constant global growth in order to achieve its targets by 2020. For the automobile sector, this means primarily expanding the customer portfolio to include non-Japanese carmakers, which has already been achieved with Sumitomo Riko’s takeover of Anvis. The targets include safeguarding and building on the market leader position. The Sumitomo Riko Group must continue to demonstrate its skills and capacity for innovation with its future drivetrain technology. As a result, research into the anti-vibration solutions of tomorrow is the key focus. We are and will continue to be the leader for current and future technology.
AI: What are some of the Anvis’ technologies that make your anti vibration systems leaders in their class?
Hahn: The success of an anti-vibration solution in the vehicle will depend first and foremost on the extensive analysis of the underlying problem in the overall vehicle. This forms the foundations of an efficient and cost-effective component design. Within the group we can draw on series-tested technology which reduces the weight of the parts and can, for example, control vibrations in line with driving speed. The focus of our research is also future drive concepts, which cause brand new vibration problems in the vehicle.
AI: How closely does your company work with automotive OEMs, and how has this helped in product development? Please give us some examples.
Hahn: Anvis is a primary developer, which means that we are involved right from the beginning in the development of a vehicle and continue to work on it right up until the series goes into production. As such, Anvis receives the basic requirements and installation space data for the development of an anti-vibration component such as an engine mount system. The individual components are designed on this basis. The engine mount system is then tested using simulations to ensure that it works properly before prototypes are built and tested in the vehicle. After approval of the technical concept by the customer we are responsible for industrialization within our worldwide production footprint and the serial production until the end of the vehicle platform´s lifecycle. We continuously provide new technological approaches for our whole product portfolio in terms of optimizing functions and weight in close consultation with the customer.
More Stories
Selecting the Ideal Linear Phased Array Transducer for Your NDT Requirements
K 2025: The Power of Plastics! Green – Smart – Responsible
Bangkok International Motor Show 2025 – The Talk of Sensuous Automotive