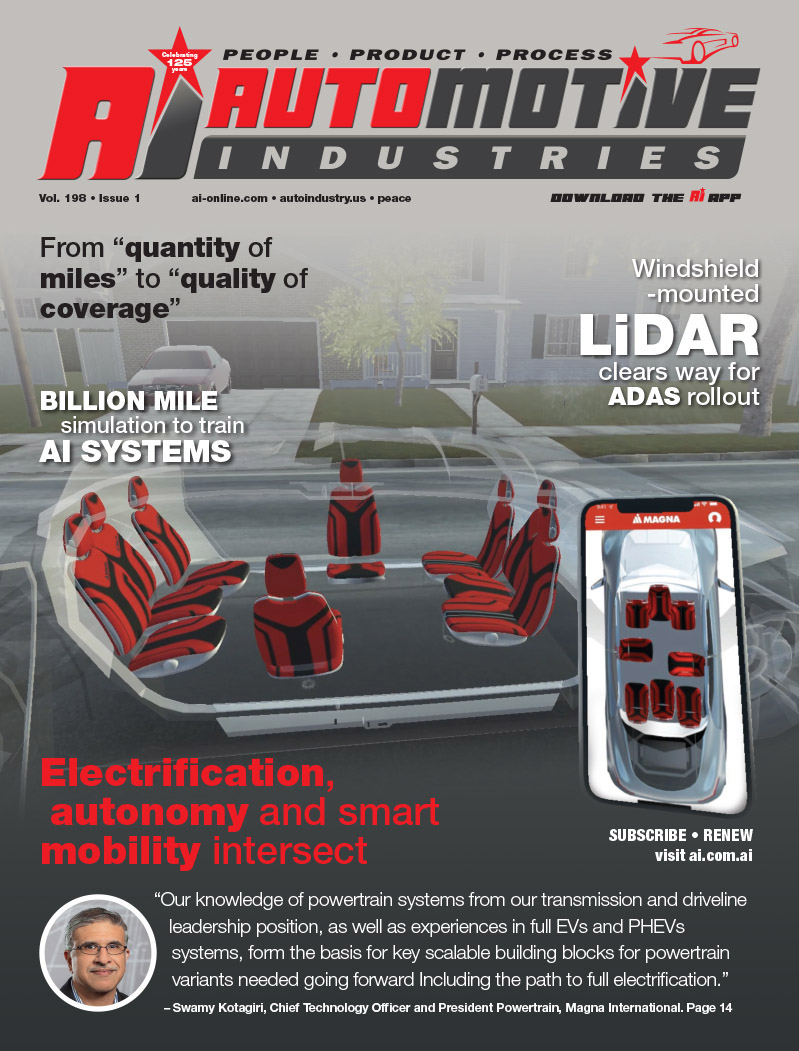
Catalyst companies are ready to supply the advanced emissions control systems needed to meet the new tighter vehicle emissions regulations that governments around the world are enacting in order to reduce pollution by combustion engines.
Automotive Industries (AI) asked Marc Ehrhardt, Senior Vice President of BASF Mobile Emissions Catalysts what the impact of the tightening emission regulations will be on the market.
Ehrhardt: Tightening emission regulations, along with new engine technologies and fluctuating precious metals prices create emissions control challenges. We have invested heavily to develop ground-breaking catalyst technology and to put in place the production capacity to enable automotive OEMs to successfully meet these tighter regulations and ensure clean air for a sustainable future.
AI: What are the challenges in achieving Euro 6 & 6c, and California LEV III / US Tier 3?
Ehrhardt: Euro 6 legislation requires a significant decrease of nitrogen oxides (NOx) emissions to less than 80 mg/km when evaluated under the New European Driving Cycle (NEDC). With the implementation of Euro 6c in 2017 still tighter requirements will come into play. Real Driving Emission requirements will be applied using Portable Emission Measurement Systems. BASF has developed innovative technologies to address these new regulatory standards. For example, our recently introduced LNT+CS4F™ emissions control system for diesel engines combines the features of a Lean NOx Trap (LNT) and a multifunctional catalyzed soot filter (CS4F).
The LNT+CS4F can remove Particulate Matter (PM), as well as carbon monoxide (CO), Hydrocarbons (HC) and NOx from diesel-engine exhaust. For gasoline engines we developed the FWC™ four-way conversion catalyst. The single-component FWC technology can remove PM, as well as CO, HC and NOx from gasoline-engine exhaust. The California LEV III and US Tier 3 emission regulations also present new emission targets.
The new LEV III emissions regulations which go into effect in 2015 require automakers to upgrade all of their vehicles to Super-Ultra-Low Emissions Vehicle (SULEV) emission standards. Improved BASF catalysts will enable our customers to meet the ambitious SULEV standard for all vehicles, including large trucks. The LEV III/Tier 3 standards impose continual tightening of Non-Methane Hydrocarbons + NOx combined standards. The stringent NOx burden will require high performance catalysts with efficient use of rhodium, while the Hydrocarbon (HC) burden will require “fast light-off” technology with efficient use of palladium.
Direct Ozone Reduction (DOR) technology can also provide HC offset credits, while new concepts such as exhaust HC trap catalysts can mitigate cold HC emissions directly. The PremAir® DOR catalyst is a proven solution that has been used on over three million vehicles. This patented catalyst coating is typically put on the radiator to transform ground level ozone, the main component of smog, into oxygen.
Ozone is one of the 3 pollutants targeted by the World Health Organization and the EU commission in addition to NOx and particulates. At BASF, we have addressed all three: particulates for diesel and now gasoline engines, NOx for all types of engines, and ozone with PremAir technology. Additionally, the new LEV III and Tier 3 SULEV regulations require near-zero evaporative emissions. BASF has introduced the EvapTrap™ automotive air intake system hydrocarbon trap. This patented technology is applied directly onto the surface of a vehicle’s air intake box to adsorb engine hydrocarbons without increasing backpressure.
The EvapTrap provides a powerful solution to meet evaporative emissions standards while allowing auto manufacturers to use their existing air intake box, thus reducing complexity and cost for the OEM. AI: What is the status of production capacity for emission control systems? Ehrhardt: We have expanded and are continuing to expand our production capacity globally. We just celebrated the grand opening of our new plant in Sroda Slaska, Poland, As our largest emission catalyst manufacturing site in Europe it will allow us to meet anticipated demand growth in the region. This site complements our recently expanded site in Nienburg, Germany. We are also building a new facility in Chennai, India, and doubling the size of our emissions catalysts plant in Shanghai, China. In the Americas, we have added capacity in Huntsville, Alabama and Indaiatuba, Brazil.
AI: Is there a different approach in Europe, US, and China?
Ehrhardt: Governments around the world are enacting tighter vehicle emissions regulations to improve air quality. We have a global manufacturing network with local production in all key countries. We also have R&D Centers in Asia, Europe and the U.S. to develop and customize technologies as needed for different markets.
AI: What is BASF doing in platinum group metals (PGM) recycling to help ensure supply?
Ehrhardt: BASF is committed to growing its position in the platinum group metals recycling market and providing customers with a high-quality source of these metals for the long term. Our European hub for autocatalysts recycling is in Cinderford, Gloucestershire, UK. In the U.S. we have a hub in Seneca, South Carolina, and additional operations in Lincoln Park, Michigan, near Detroit. We are continuing to make significant improvements to our manufacturing infrastructure for automotive catalysts recycling to optimize our production efficiencies and position BASF to costeffectively meet growing demand for our high-quality precious metals products.
AI: What is your forecast for the electric vehicles market?
Ehrhardt: While full electric vehicles have not yet experienced high rates of adoption, hybrid sales have continued to accelerate. In our view, the internal combustion engine will continue to drive the majority of vehicles well into the next decade. However, in order to meet increasing demand for powertrain solutions using varying degrees of electrification, BASF has created a business unit within the Catalyst Division that offers advanced battery materials for lithium-ion batteries. BASF is committed to serving the automotive industry with materials, innovations and technologies that can bring battery performance to the next level. The long-term objective is to become a leading provider of functional materials to serve cell and battery manufacturers worldwide. To participate in this market, BASF has committed to invest a triple-digit million euro sum to develop its global Battery Materials business.
AI: Is there a future for use of natural gas as an alternative fuel to gasoline and diesel?
Ehrhardt: Yes, in fact, the number of vehicles using natural gas is increasing. We have developed unique catalyst technology for use with natural gas engines. In addition, BASF is commercializing advanced metal organic framework (MOF) solutions that allow for the efficient storage of natural gas which could increase vehicle range or lower tank storage pressures. MOF materials provide high surface area on which gases are adsorbed. For example, a one gram sample of MOF materials offers a surface area equivalent to a football field.
AI: What is the impact of sustainability on the business?
Ehrhardt: For BASF, sustainable development means the combination of long-term oriented economic success with environmental protection and social responsibility. Our business invests heavily to develop innovative emissions catalysts to enable clean air for a sustainable future. We use resources efficiently to produce our products plus provide training, employment and development for over 3,000 people around the world and support the communities where we operate. Sustainability is the foundation of our business and we are proud that BASF has been recognized as a global leader for sustainability
More Stories
AVL ThermalLab™ brings dynamic road VTMS conditions to the laboratory
Sika – where battery storage technology for EVs, wind and solar meet
Driving Change with Circular Aluminum: Hydro’s Role in the Automotive Future