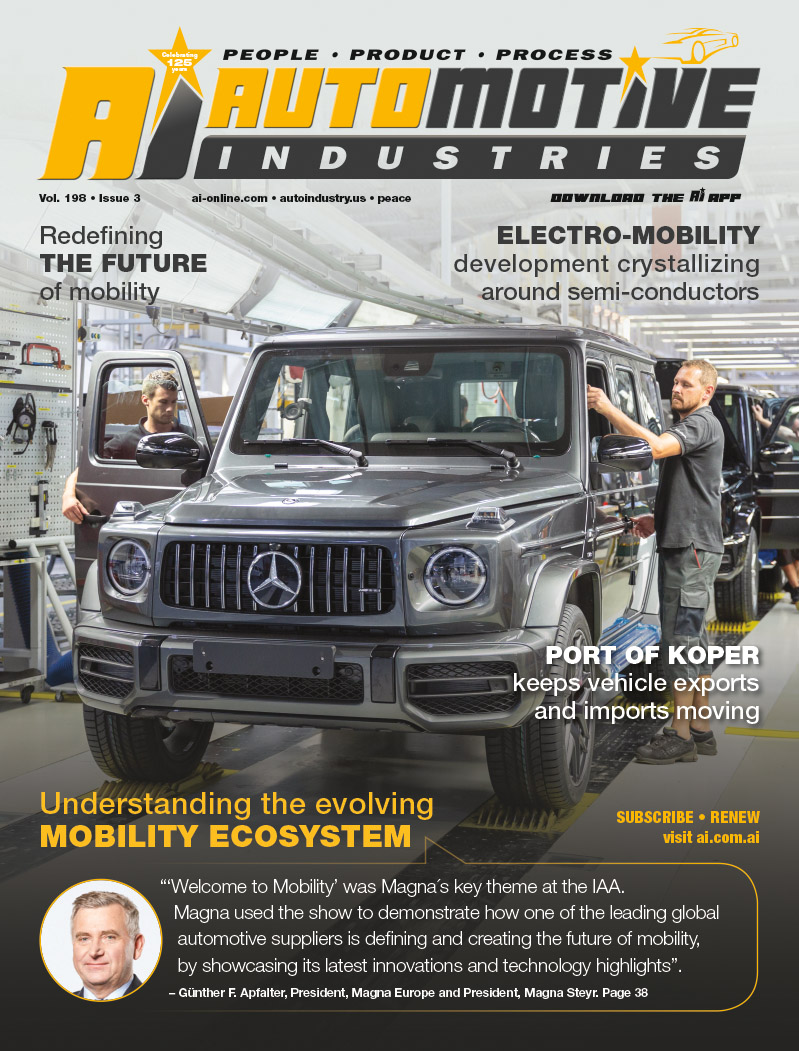
In order to meet emission, safety and other environmental standards automotive OEMs and suppliers need to identify solutions and materials that are lightweight, while providing improved performance. Equally importantly, the durability of the components has to support the trend for manufacturers to offer extended vehicle warranties. In many cases the solution lies in replacing metal components with plastics.
Automotive Industries (AI) asked Jürgen Reinert, Global Automotive Strategy Manager Victrex Polymer Solutions, how polymers can help OEMs meet the challenges posed by the increasing requirements for CO2 reduction.
Reinert: Our 35 years of experience in applying high-performance polymers based on VICTREX® PEEK polymer has resulted in a whole serious of innovative, reliable solutions which have proven that our thermoplastics perform well even in most demanding environments. To gain know-how is important, but it is even more important to genuinely act as a solutions provider by partnering with OEMs and Tier1s next to the enablers, our processors. Let me give you a “simple” example: balance shaft gears when made with VICTREX® PEEK instead of metal saw a 68% reduction in weight. To be quite honest, these gears are really small and do not weigh much, so the saving is not particularly significant. Much more important is the fact that this is accompanied by a 78% reduction in the moment of inertia, which results in a 9% increase in efficiency due to a reduced moving mass and lower frictional losses, not to mention a comfortable “side effect” for drivers: a 3dB reduction of harsh noise and vibration. For the human ear this is equivalent to a 50% reduction in noise level.
AI: How do you help OEMs and suppliers to identify solutions and materials that reduce weight without compromising performance?
Reinert: As the world’s leading solution provider of PEEK polymers, we have a really huge portfolio of products. For each individual challenge we partner with customers to choose the right solution from our product range or even develop a modification able to meet current challenges. As you may know, VICTREX® PEEK polymer provides exceptional performance over a wide range of temperature and extreme conditions. It is the material of choice when an end-use application demands a combination of three or more simultaneous performance properties.
AI: What is Victrex’s contribution to the trend of downsizing engines? Can you give us an example?
Reinert: When Melling Engine Parts, a leading manufacturer of fluid pumps for the worldwide transportation industry headquartered in Jackson/USA, was developing its innovative electric water pump for the automotive industry, it needed a small sliding bushes that would support the pump’s impeller in the highly stressful environment of today’s engine cooling systems. Melling chose an innovative wear grade, VICTREX® WG™ polymer, for the bushes because of its ability to withstand the mechanical stresses of a high-heat environment where metals had previously failed. VICTREX® WG polymer maintains its properties at high temperatures even after 5,000 hours at 250°C and is – despite the corrosive pump media – able to withstand the mechanical stresses of a high-heat environment for a long period of time. At the same time, the high-tech material contributes to the optimal efficiency of the pump by reducing frictional losses. This results in reduced power consumption, less wear on the pump, and therefore a longer lifetime than metal components – and so meeting the extended warranty targets.
AI: What benefits do you offer OEMs in terms of minimizing friction losses, while increasing efficiency and safety?
Reinert: Usually engineers don’t like to see friction losses as they result in heat, abrasion and ultimately a diminished component lifetime. Take thrust elements made from VICTREX® WG101, for example. This grade has excellent frictional properties and is able to withstand extreme conditions up to 20 times longer due to its excellent creep resistance compared to that of other PAEK compounds – even with poor lubrication. But wear resistance, compressive creep resistance, and low, constant coefficients of friction do not usually suffice. Materials also have to withstand both progressively high temperatures and the increasingly aggressive synthetic lubricants used in gearboxes. In today’s transmission oils, VICTREX® PEEK shows no perceptible change, even if extreme pressure (e.p.) additives are added. The result is higher efficiency and safety due to higher reliability, and a longer lifetime, with fewer repairs needed. Of course, cost-efficient production plays a major role in the automotive industry´s decision making. With VICTREX® PEEK produced in a standard injection molding process, typically there is no need for post processing.
AI: How does your aerospace expertise help with the development process of lightweight automotive solutions?
Reinert: With the aerospace industry focusing on reducing aircraft weight engineers are searching for reliable solutions such as thermoplastic compounds that can perform with at least the same assurance as traditional metals and thermosets. For decades, polymer solutions based on VICTREX® PEEK, including VICTREX® PEEK in unfilled carbon fiber-filled, and glass fiber-filled variants, have proven successful in removing excess weight from the likes of aircraft or industrial equipment. Lightweight tubing made of VICTREX® PEEK weight 60 % less than equivalent stainless steel tubing. These VICTREX® PipesTM are used for the drainage system in the cargo holds of the A350 XWB. And with VICTREX® PEEK HMF polymers weight savings up to 80 % compared to metals are possible. The carbon fiber-filled material offers the highest specific strength currently available in the Victrex product range and was therefore approved by Airbus a 31couple of months ago. The inclusion of high-modulus fibers (HMF) into high-flow VICTREX® PEEK offers the strength and stiffness that have given engineers the confidence to displace metals. Having the flying examples that Victrex materials are just as capable as the metals they are replacing in aerospace applications means that Victrex is able to transfer that experience, knowledge and data to the automotive industry to support its overall weight saving efforts and targets. Victrex also understands that, as operating environments become more extreme, material integrity will be critical to performance.
AI: How is Victrex positioned globally to meet the demand for metal replacement?
Reinert: Victrex has continuously expanded its product range, applications and production capacity. With a technical center at its headquarters in the UK and technology centers in Shanghai and Tokyo, Victrex provides testing, prototyping and application development for processors and end customers. Through the targeted expansion of global dedicated industry teams, our automotive experts for example cover important markets worldwide – including those in Europe, the USA and Asia. We have a serious understanding of regional as well as global trends. Victrex is also currently investing in additional production capacity, to ensure we can meet the security of supply that customers need. Furthermore, we use our experience with PEEK to advise our customers at every step of the way, to ensure that their needs are met – from conception to mass production – to boost both profitability and the future performance of their products.
AI: What can we expect from Victrex in the future?
Reinert: Every industry has its own future requirements. Being aware of these industry-specific characteristics helps us to meet the challenges of our customers and to translate these challenges into benefits for customers along the entire value chain from various industries. By taking into account changing requirements ahead of time, and by talking and listing to our customers we can contribute the right know how and material solution according to their needs, today and tomorrow. This enables us to support OEMs as well as their suppliers to move ahead of their competition.
More Stories
Some Ways How Motorists End Up in Collisions at U-Turns
Maximise Margins with Proven PPF Tactics
Finding the Car Boot Release Button – Tips and Tricks