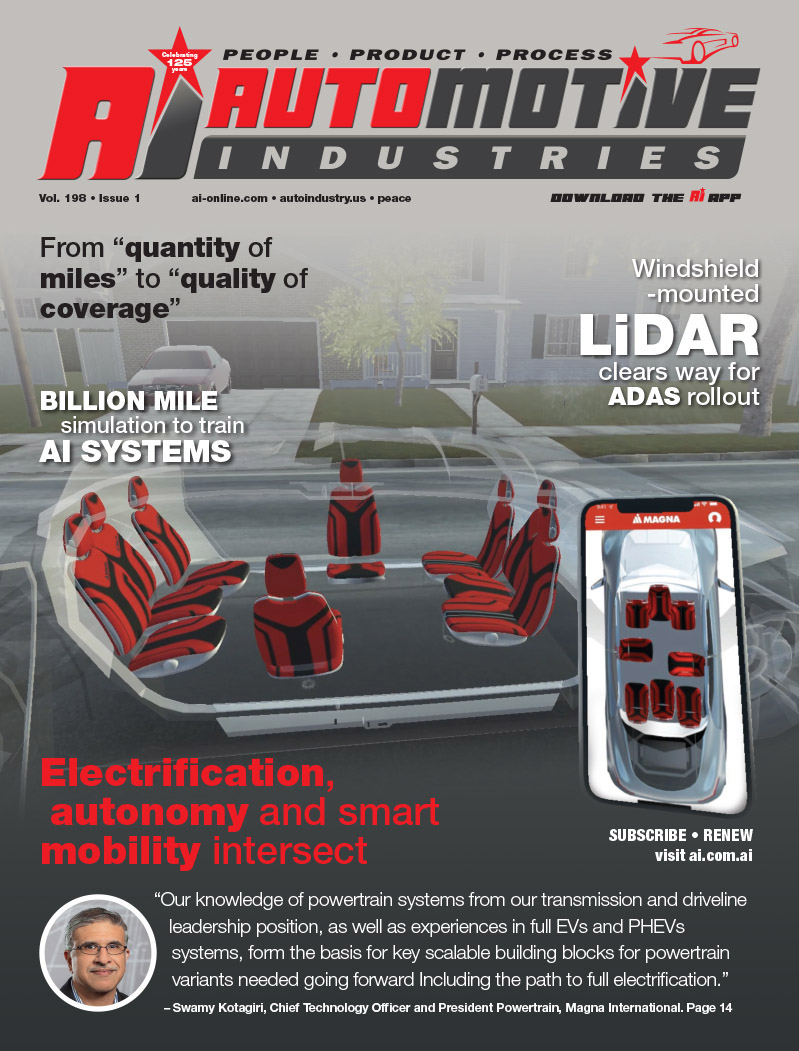
A compact 48-Volt electric drive module with integrated clutch and planetary transmission which can be placed on either the front or rear axle paves the way for cost-effective hybridiza¬tion and the roll-out of electric vehicles.
It complements Schaeffler’s portfolio of solutions for high-performance engine start-stop functions, hybrid clutches, hybrid modules, and drive solutions for hybrid vehicles. Schaeffler has been working with Ford engineers on the eWheelDrive development vehicle which is based on a Ford Fiesta, and was unveiled at the 2013 IAA Frankfurt.
The compact vehicle uses two Schaeffler E-Wheel Drives installed in the rear wheel arches. “Excellent driving dynamics are among the main attributes of Ford vehicles, and our expertise and experience in this area has also been used during this project. The test drives have shown clearly that the driving behavior of this test vehicle in terms of comfort and safety has remained at virtually the same level, despite the higher wheel-sprung masses compared to the conventional basic vehicleâ€, says Roger Graaf, project manager at Ford Research & Advanced Engineering Europe.
Automotive Industries (AI) asked Peter Gutzmer, Chief Technical Officer at Schaeffler, what makes the 48-volt drive module an ideal option for manufacturers looking to electrify their vehicles.
Gutzmer: With the 48-voltdrive module Schaeffler offers an economically attractive, low-cost option that allows CO2 emissions to be reduced by up to 15%. The low-voltage design of the solution reduces outlay compared to high-voltage solutions with their associated requirements. The use of a 48-volt electric system offers the opportunity for entry-level for hybridization.
AI: What was it like working with Ford on the E-Wheel drive concept car? What are the synergies between the two companies?
Gutzmer: The cooperation between Ford Research & Advanced Engineering Europe and us was extremely successful and immensely stimulating. The joint development, coordination, testing and assessment program being carried out for the Fiesta eWheelDrive – which was constructed in cooperation with Ford Research & Advanced Engineering Europe – includes everything from extensive test drives in the cold climate of Scandinavia to comprehensive driving dynamics tests requiring a lot of space. Ford brings of course a lot of vehicle assessment experience to the party, whereas Schaeffler is developing lots of hub wheel drive competence. Schaeffler’s E-Wheel-Drive wheel hub drive is now also part of a research project that is listed by the German Federal Ministry of Economics and Technology. The electric wheel hub drive has the potential to become one of the drives of tomorrow.
AI: What is Schaeffler’s strategy in the electric vehicle/ hybrid vehicle eco-space?
Gutzmer: Legal requirements with regard to lower emissions and fuel consumption are globally increasing all the time. It is clear that drivetrains based on internal combustion engines will continue to play a central role in individual mobility, while solutions such as downsizing and down-speeding lead to new solutions for charging, as well as to new transmission concepts with multiple gear stages and full variability. At the same time, the electrification of the drivetrain is making rapid progress: Engine start-stop systems are becoming standard, the recovery of braking energy is gaining popularity on the roads, and the number of hybrid vehicles – especially plug-in hybrids – is increasing. Regional characteristics, such as those of megacities in Asia or of the western regions of China that have not yet been fully opened up in terms of their infrastructure must also be taken into account. A structure for larger volumes of all-electric vehicles based on new vehicle platforms, e.g. with wheel hub drives like those currently undergoing preliminary testing in concept vehicles at Schaeffler, may arise here. Aside from this, all-electric individual transport – with the exception of e-bikes and e-scooters – still requires significant technological advances in terms of battery technology and charging infrastructure. Schaeffler is developing key components and modules like e-axle platforms that can be used for electric on demand all-wheel drive solutions including torque vectoring or very compact hybrid modules installed between combustion engines and transmission. And, of course, innovations for start-stop and a strong focus on low-cost 48V-Hybridization have a strong part in our strategy in this field.
AI: Your company is pinning its strategy as far as engines go to “smaller is better†– why?
Gutzmer: In the past, a high engine capacity alone was used to generate power, whereas today reducing the engine capacity and the number of cylinders provides performance and efficiency – which also benefits the environment. But this doesn’t mean that the drivers of today and tomorrow have to settle for less. On the contrary, the engines of tomorrow are high-performance, turbocharged machines with direct injection and a wide selection of auxiliaries. The minimization of friction and the reduction of resistances in the drivetrain play an important role in this context. This is where optimized components and surface coatings, such as rolling bearing supports for turbochargers and balancer shafts come into play. The variable valvetrain is a further key element for efficient downsizing. These range from switchable valvetrain components and camshaft phasing units through to UniAir, the world’s first fully-variable electric-hydraulic valvetrain system. Because engines with a small number of cylinders don’t run as smoothly as an engine with twelve cylinders, balancer shafts and vibration dampers are used to ensure smooth running in the engine and transmission. All of these elements combine to create compact engines that are economical, provide high-performance, and comfortable all at the same time.
AI: Tell us about your company’s drivetrains based on ICE.
Gutzmer: The technologies for drivetrains with internal combustion engines include electromechanical and electrohydraulic phasing systems for the valvetrain, double clutch systems, electronic clutch management systems, and many others. Schaeffler’s Efficient Future Mobility North America and Efficient Future Mobility India concept vehicles, for example, demonstrate the effective interaction of these technologies and the potential for the optimization of drivetrains with internal combustion engines that is still available. The internal combustion engine is still the dominant power source for the world´s fleet of vehicle and has great potential for efficiency, which can be harnessed using various technologies for downsizing or increasing specific loading.
AI: How has the downsizing of engines strategy gone down with OEMs?
Gutzmer: Downsizing is helping OEMs and suppliers to meet tough emissions and consumption targets. Therefore Tier 1s must supply answers to questions of friction, NHV and robustness. OEM powertrain strategies will have a big impact on the components and systems that Tier 1s develop. The trends for downsizing and down-speeding are probably the most significant: engines will operate more and more at low-speed, high-load conditions. There´s a big opportunity for the next generation of dual-mass flywheels, downsizing, introducing higher vibration sensitivity and NHV control – both on the clutch side and on the front-end accessory drive. Fewer cylinders mean you have more movement, so there´s opportunities for our vibration damper tension system. At the same time transmission solutions with wider spread range and more gears or even fully variable systems are gaining importance.
AI: What impact has your thermal management module had on cutting CO2 emissions?
Gutzmer: The new thermal management module is another element to reducing fuel consumption and CO2 emissions by up to 4%. The performance of the thermal management module makes this component particularly suitable for use in engines for start-stop operation. The individual components are optimized for friction in accordance with Schaeffler’s requirements in terms of energy efficiency. This means that the thermal management module can be connected directly to the engine control unit without additional power stages thanks to its low power consumption.
AI: What is Schaeffler’s long-term strategy in terms of new technologies?
Gutzmer: Schaeffler is a global supplier of expertise for Efficient Future Mobility. Its’ broad range of products for drivetrain and chassis applications, which is regularly supplemented through the addition of innovative solutions, makes it one of the most important partners for the global automobile industry. The product portfolio and product innovations reflect the company´s diversification strategy in the fields of optimization of drivetrains based on internal combustion engines, electromobility, and hybridization. Meticulously detailed work and new solutions for drivetrains based on internal combustion engines still offer significant potential for reducing fuel consumption and emissions. The increasing electrification of the drivetrain will continue to make an important contribution with regard to the energy efficiency of automobiles with internal combustion engines in the future. This opens the door for us to gain the necessary expertise in the field of electric drives, where long-term predictions for the future are very promising.
More Stories
Some Ways How Motorists End Up in Collisions at U-Turns
Maximise Margins with Proven PPF Tactics
Finding the Car Boot Release Button – Tips and Tricks