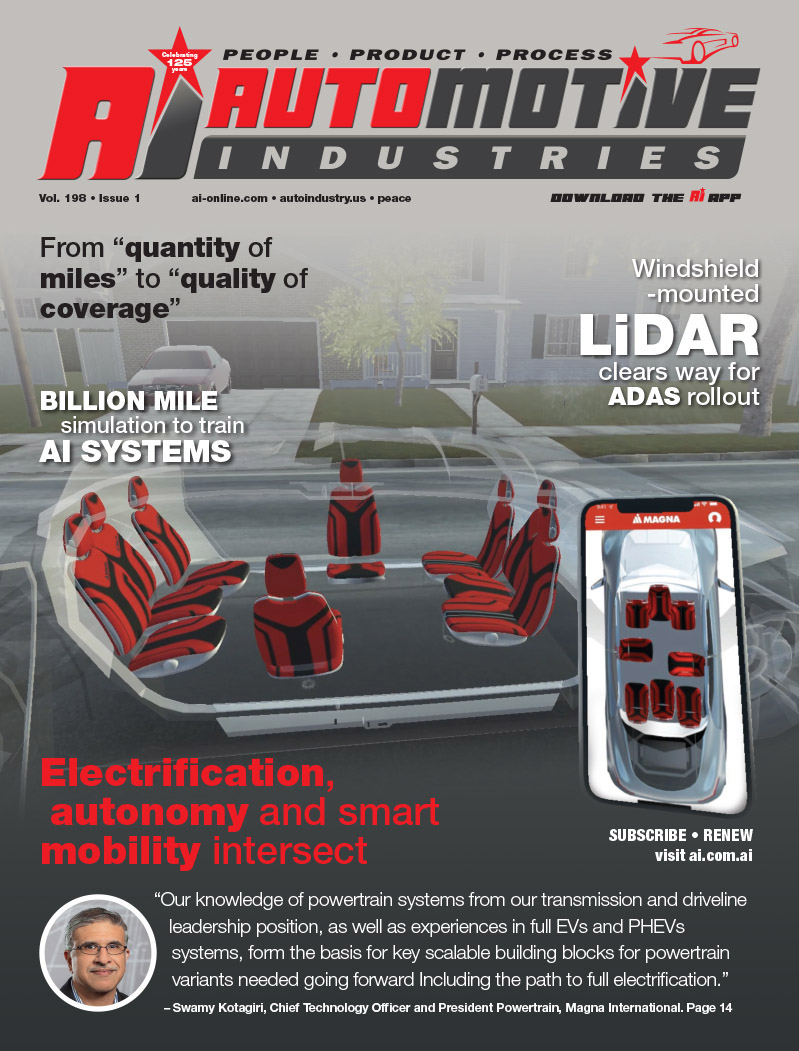
There are literally hundreds of millions of containers, carts and sub-assemblies flowing through manufacturing plants around the world each day – most of them bearing a static paper label. The label is printed and attached during every cycle as a visual flag for workers to do something with the asset. Since being introduced by Toyota, this production signal or sign (literally the translation for KANBAN) has been used extensively within automotive manufacturing more than 40 years throughout manufacturing as the primary shop floor control. This simple visual cue has been the core of systems which balance production and create more efficient “just in time” inventory to great success.
So what’s next? Have there really been no improvements or changes in 40 years? Many candidate solutions have been introduced, including extensive software implementations, tracking systems and worker mobility devices. While some of these have attractive benefits, none have been able to replicate the one key element that is so critical to success – inexpensive operator readable information at every point of action. However a revolutionary new solution has emerged with the convergence of low cost wireless technology, micro-power systems and inexpensive electronic paper. “Visual Tagging” promises to be the first step change in cyclic process efficiency in decades.
Wirelessly updated, the hardened e-paper screen eliminates label printing and placement costs – allowing most systems to be paid for in about 18 months from this direct cost reduction alone. In an environment where sustainability and green initiatives are everywhere, saving millions of prints a year in an average automotive manufacturing plant can also make a large contribution to those goals.
What is most impressive are the indirect benefits through leaps in process effectiveness. These smart containers become immediately traceable, enabling real time data collection on asset flow for advanced process analytics. Real time, accurate inventory counts are achieved with no manual counting. Unlike paper, electronic placards can also be changed dynamically, allowing operators to receive new instructions in real time for light speed corrections and process exception handling. Repurposing some material for another part of the line or staging it to balance flow? No problem. Think about a quality hold appearing immediately on a batch of containers needing to be quarantined through the plant. Those quarantined containers also have memory and can tell you their history, creation date of contents, which operator worked on them, time in inventory, temperatures experienced and many other really smart things. How about a container displaying if it is full or empty so you don’t have to open it to find out? What if the container told your worker where it was supposed to be and when it should be taken there?
Adoption has already begun around the world including several leading automotive manufacturers and supply chain members. Initial results are making a strong case that cycling smart containers will be the center of a revolution in manufacturing and industrial logistics for decades to come.
More Stories
Sonatus – The industry is shifting gears to software
Cybord warns of dangers of the stability illusion
HERE building trust in ADAS systems