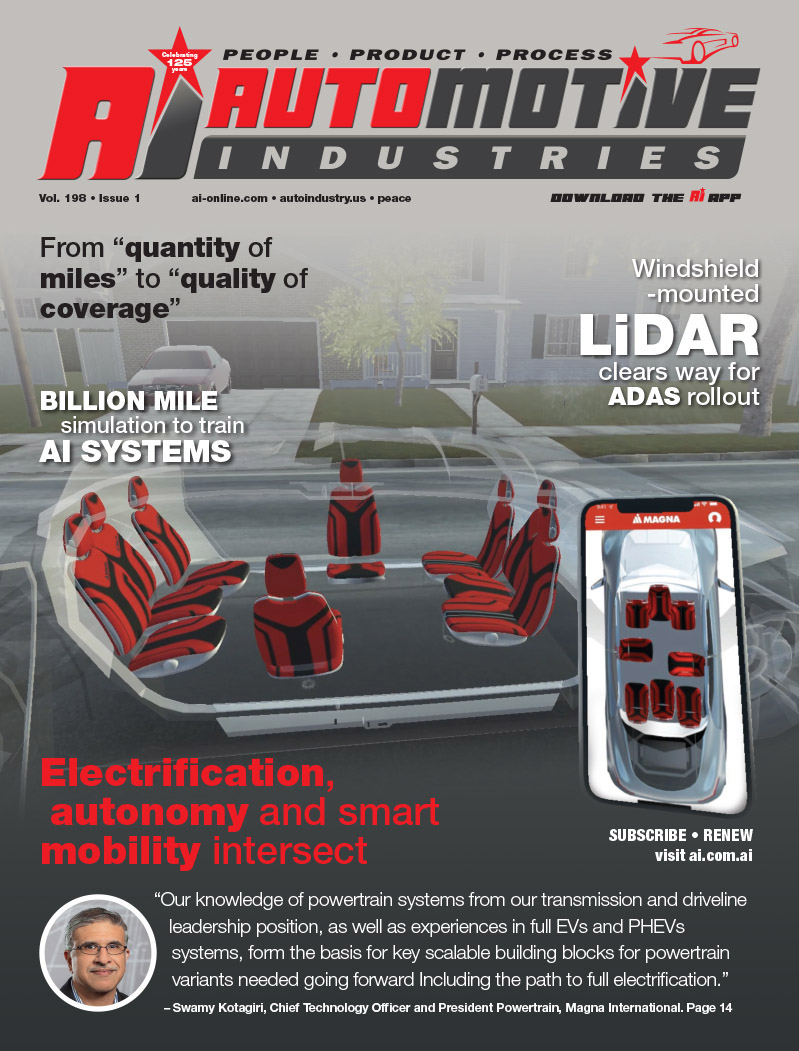
Sulzer Metaplas, a Sulzer Metco company, presents a new Diamond-Like Carbon (DLC) coating development for the automotive industry. The new surface solution A.CARBON combines friction reduction and wear protection to a high performance coating for many components.
The automotive market asks for solutions that combine an eco-friendly coating with higher performance — the key drivers for automotive manufacturers and suppliers. Vehicles with an economical combustion engine are in great demand. Thereby DLC coatings like Sulzers tailored solutions are key to success. For years numerous automotive manufacturer trust in DLC solutions for components of the drive, transmission and especially engine.
DLC coatings are essential
The largest proportion of thin film coating solutions in the automotive industry use diamond-like carbon coatings. By reducing friction, corrosion, and wear, they improve engine performance, extend the life expectancy of components, and reduce emissions. For diesel injection components DLC coatings have become an integral part. They have already led to the development of demanding common-rail and high-pressure injection systems with injection pressure of 3000 bar for diesel generator sets and 300 bar for gas engines. DLC coated pressure pistons and valve seats for example reduce wear by growing contact forces and more narrow lubrication gaps.
Thus, even at high injection pressures in the entire speed range optimal mixture formation and combustion processes as well as low emissions can be achieved. This improvement leads to less fuel consumption in a small single-digit percentage range plus a reduction of CO2 emission per kilometer.
A.CARBON gives a high-performance competitive edge
Our newly developed DLC coating, A.CARBON, helps automotive designers achieve the EU6 emission limit and ensures component reliability. The amorphous coating A.CARBON provides excellent wear protection for dry and starved lubrication applications as well as abrasive and adhesive wear protection in tribological systems. The application of low friction and wear protection coatings ensures the reliability for the entire component life time. Thanks to the amorphous structure and the a-C:H:W layer within the multilayer coating architecture, as well as the resulting high hardness of 22 to 30 GPa A.CARBON is best suited for highly stressed components of modern engine manufacturing while improving fatigue resistance.
Like all DLC coatings A.CARBON is characterized by its extreme smooth surface and its self-lubricated properties. Even in low lubrication conditions, the coating decreased the coefficient of friction significantly, performing as well as in well-lubricated conditions. Even in drive operation the surface remains smooth due to the high wear resistance and oil wetting. A further benefit of the DLC coating is the fact that the uncoated counterpart is protected against wear. It is often sufficient to coat only one surface of a frictional couple.
The coating of components like e.g. injection components, finger followers, tappets or pistons, piston pins and rings contribute to attaining the emission targets.
The benefits based on increased tool life time by reduced friction, corrosion and wear protection, as well as reduced lubricant requirements lead to decreased energy respectively fuel con-sumption, and noise and emission reduction. Based on this, DLC coatings are essential.
Due to our best-in-class coating equipment and ISO TS 16949 certified production processes, we are suited to serve the demanding requirements needed for automotive mass production.
Our know-how and experience in DLC coating ensures that already today we can fulfill today’s automotive market requirements as well as those of the future.
A.CARBON at a glance:
Color: Black
Coating thickness (μm): 2-5
Surface hardness (HV): 2000 – 2800
Abrasive wear resistance: 1 to 0.5 * 10-15 m3/Nm (calomax test)
Adhesive strength: HF1 – HF3
Coefficient of friction against steel (dry, μ): 0.10 – 0.20
Temperature stability: up to 300°C
www.sulzer.com/ACARBON
More Stories
Mosaic Click board from MIKROE delivers global coverage multi-band and multi-constellation tracking ability
Current transducer from Danisense selected for DC charging station testing device demonstrator at TU Graz
New Click board from MIKROE helps develop and train ML models for vibration analysis