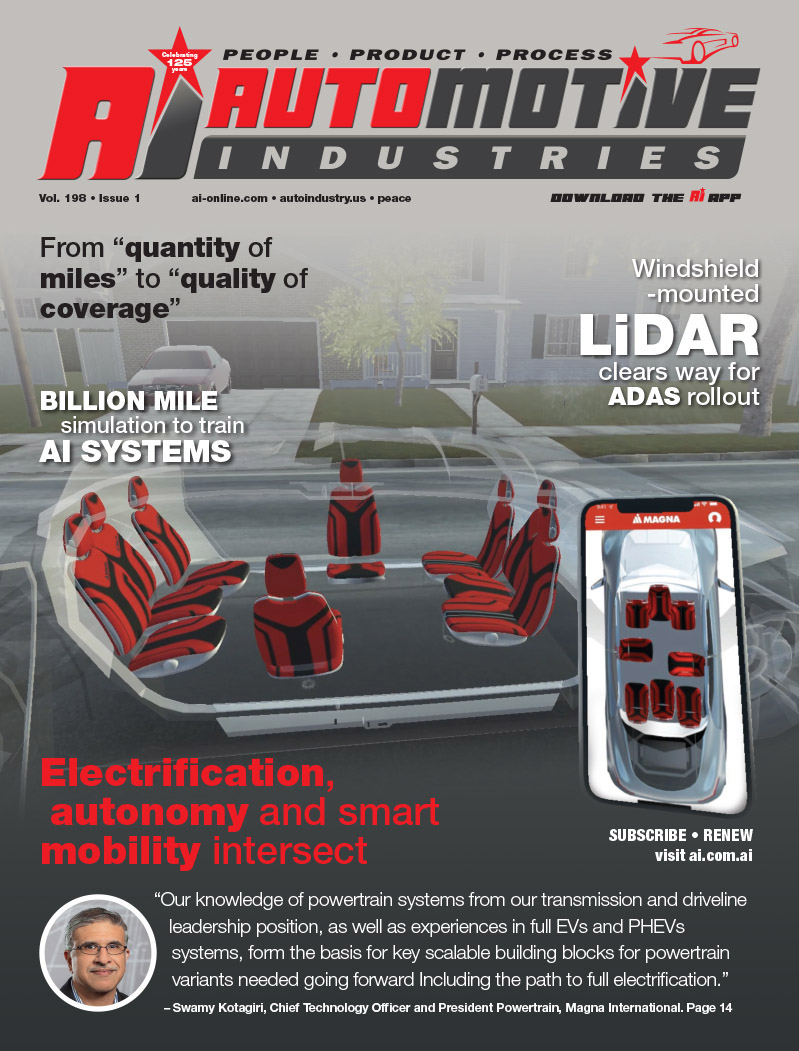
Thailand is well on the road to reaching the government supported industry target production of three million units a year by 2017. Record local and export sales in 2012 saw the country become the world’s 10th-biggest producer of motor vehicles. Now the country is positioning itself as the hub for production for the 600-million consumers in the ASEAN Economic Community (AEC).
The 10 ASEAN member countries making up a massive single market and production base are Thailand, Singapore, Malaysia, Indonesia, Vietnam, Cambodia, Laos, Myanmar, Brunei and the PhilippinesSix of the ASEAN members – Thailand, Malaysia, Indonesia, Philippines, Singapore, and Brunei have been completely duty free since Jan 2010. The remaining four will have dropped all duties by 2015. For 2015 is the target to complete free flow of investment, capital, people, services etc. This will open doors for automotive enterprises in Thailand to enjoy easy access throughout a “seamless AEC market of 600 million consumers,” according to the The Thailand Board of Investment (BOI). Extensive government support is helping fuel the country’s auto sector, which accounts for 12% of Thailand’s gross domestic product (GDP).
The Thailand Board of Investment’s (BOI) investment promotion policy “is to promote sustainable development” to enhance the country’s competitiveness in science and technology and encourage the improvement of manufacturing quality as well as reduce environmental impact,” Ajarin Pattanapanchai, Deputy Secretary General Thailand Board of Investment (BOI) told Automotive Industries.
Automotive is the nation’s largest export sector, with an estimated value of US$23.7 bn.. In 2012 vehicles accounted for the bulk of exports, at 69% of the total, followed by OEM engines (28%), and then spare parts (3%). The market for OEMs and component suppliers based in Thailand is much greater than the AEC. Thailand ships automotive products to more than 170 countries, with Asia absorbing 32% of exports. Japan is the top single-country destination, with Indonesia, Australia, the Philippines and Malaysia completing the top five export destinations.
According to Pattanapanchai, there are still opportunities in the market. Thailand imports about US$8 billion worth of auto parts annually. Government is offering a range of incentives designed to attract as much of this manufacturing volume to Thailand as possible. At the same time, it is geared up to leverage on Thailand’s electronics industry by attracting investment in new automotive technologies. “Sophisticated electronic components are the next great phase of emphasis in Thailand’s robust automotive industry. As consumers demand increasingly smarter vehicles, the R&D and production activity in the country’s automotive electronics sector continues to expand, with unlimited high-tech investment opportunities,” says Pattanapanchai.
Described as “a sector wide open for business growth,” opportunities for Thai automotive electronic component manufacture include: systems for controlling power or engine and transmission electronics, safety systems, chassis and suspension electronics, driver assistance such as collision avoidance warning and night vision sensing, passenger comfort, information systems and in-car entertainment. As technologies converge, a modern car now has more than 100 electronic control units, each with the potential to function better and better through constant innovation. As one example, for higher and higher levels of reliability and functionality, breakthroughs in power performance can involve better fuel injection, shift changes, emission control and lubrication, says the BOI.
Safety is described as “ripe for investment” by developers of improved anti-lock braking, traction control, air bags, hill descent control, blind spot detection, automatic wipers and headlamp beams that adjust on their own. Eco-car project In 2007, the Thai government identified the opportunity and need to be a leader in the supply of a second platform because there was only limited growth left in the pickup market as Thailand was already the world’s second-biggest producer of this type of vehicle, according to Pattanapanchai. From this was born the ecocar project. It is designed to plug into the global trend towards fuel efficiency, reducing environmental impact through lower CO2 emission and greater safety. The BOI introduced a range of incentives to promote the manufacture of fuel-efficient and environmentally safe eco-cars in Thailand as far back in 2009. The policy is aimed at supporting the green initiatives in the global auto industry. The BOI focused first on components, such as batteries for hybrids or electric vehicles, according to Pattanapanchai. These incentives have attracted five eco-car manufacturers. Nissan was the first, introducing its March model and later offering the Almera. Today those compete for Thai market share with the Honda Brio, Suzuki Swift and Mitsubishi Mirage. Toyota is to launch eco-cars in 2013, according to Pattanapanchai.
Among the BOI’s requirements for eco-cars is that such vehicles need fuel economy of at least 20 kilometers per liter, must meet the Euro 4 emission standard, and should have UNECE 94 and 95 safety levels. In addition, four of five main components (cylinder head, cylinder block, crankshaft, camshaft and connecting rod) must be produced in Thailand, she told AI.
Adding a further spark to eco-car production, the BOI is offering tax incentives for investment in the manufacture of the high-tech batteries that are the heart of the EV. Industry experts believe that once mass production commences, local demand for electric cars will increase as economies of scale push down sticker prices. Mitsubishi Motors Thailand is among the enterprises to have already expressed great interest in the EV project. The company said it could launch production of an electric version for its Mirage eco-car in two years as long as the batteries are available, according to the BOI.
With lower energy consumption than gasoline or hybrid-powered vehicles and a high level of material recycling, EVs could make up 10% of global automobile output by 2020, according to the Thai Automotive Industry Association. The incentives are supported through stimulation of the local market. Under a fuel-efficient transportation initiative, thousands of natural gas-powered taxicabs are going into use. By September 2012 Thailand’s had around 480 natural gas vehicle (NGV) service stations. The BOI provides incentives for investments in NGV production, including engines, tanks, other parts, and machinery for service stations of such vehicles.
“A lively domestic vehicle market makes Thailand fertile ground for automotive investment. And as carmakers launch new models to meet rising demand, local auto parts producers are increasing capability to accommodate the upswing,” says the BOI.
According to Pattanapanchai, BOI support for investors includes an investment matchmaking program; 1-stop for visas and work permits – with work permits issued in three hours; a global sourcing program that links suppliers from around the world, access to a database supporting ASEAM producing, and “interaction with other government agencies on behalf of investors,” she says.
Automotive Industry Incentives
Based on the incentive package that was in place to the end of December 2012, support from the Thai government is expected to offer:
• Exemption of import duties on machinery
• 8-year exemption of corporate income tax with no cap
• 5-year, 50% reduction of corporate income tax on net profit
• 10-year double deduction of transport, electricity and water supply costs
• Deduction from net profit of 25% of investment in infrastructure installation and construction costs, in addition to normal capital depreciation
• Projects can be located anywhere except Bangkok
Priority sectors with Maximum Tax Incentives (end by 2013) (8 years tax holidays + 50% reduction another 5 years)
• ABS brake system, regenerative brake system
• Substrate for catalytic converters
• Electronics for automotive: electronics fuel injection, electronics stability control, electric air conditioning systems for vehicles
• Transmission systems
• Batteries for EVs Traction motors for vehicles (hybrids or fuel cell cars)
• Manufacture and repair of aircraft & parts & accessories
• Machinery with design, mold and die capacity
Thai auto sector by the numbers
• World’s 10th-largest automobile producer in 2012
• Second-largest producer and market of pickup trucks
• 14 assemblers
• 635 Tier 1 suppliers
• 1,700 Tier 2 and Tier 3 suppliers
• Local content ranges between 80-90% for pickups, and 30-70% for passenger cars
• Domestic car sales 2012 – 1,436,335 units, or 81% year-on-year growth
• Car manufacturing 2012 – 2,453,717 units, or 68% year-on-year growth
• Exports: 1,026,671 units, or 40% year-on-year increase
• Thailand is also a leading motorcycle hub, producing about 2.5 million units in 2012
Eco-car investments
Thailand is attracting investment in energy saving and alternate vehicles through a number of incentives. To date:
• 5 projects approved
• Production capacity: 585,000 units
• Export prediction: 405,940 units Total employment: 8,081 units
• By the third quarter of 2012, over 200,000 eco-cars had been sold locally
More Stories
TomTom’s Orbis Maps with 3D Lane geometry set new standards for mapping precision
Accelerating The Development of Hydrogen Vehicles & Infrastructure – Europe’s Biggest Players Meeting at Premier Event
Automotive IQ Announces the 15th Annual Automotive Functional Safety Week 2025