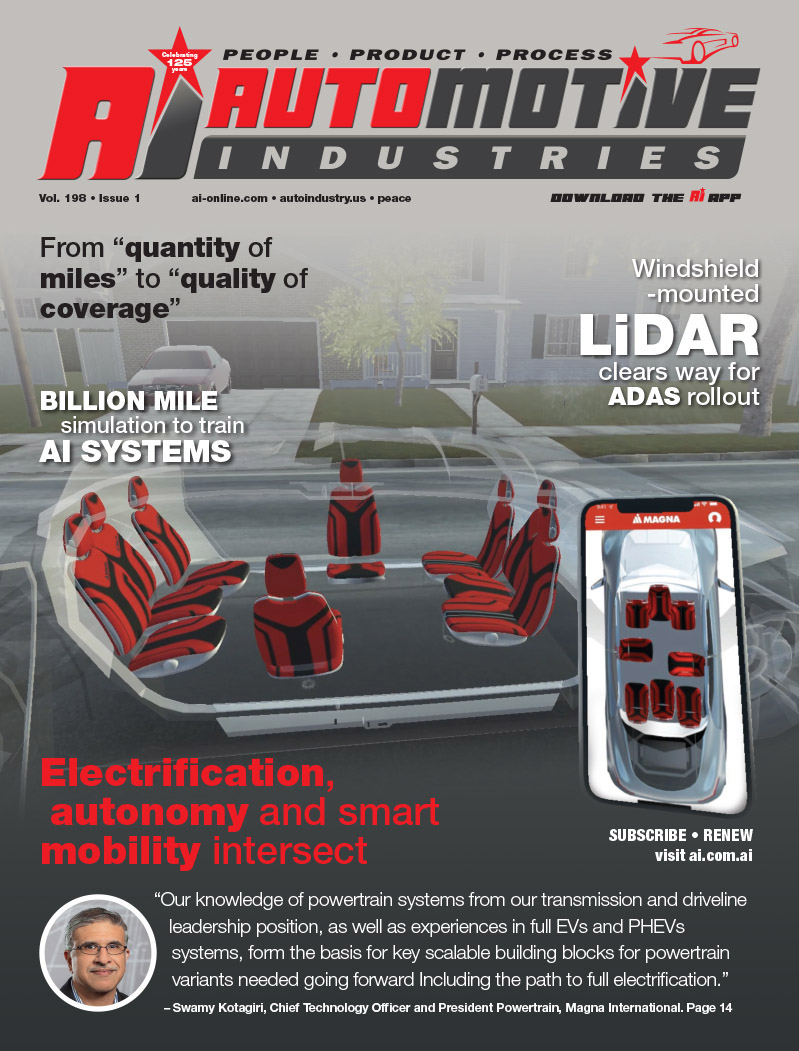
Conductive plastics developed for the space age are now finding their way into the automobile as manufacturers continue to focus on reducing weight and streamlining manufacturing.
Electriplast Corporation, a wholly owned subsidiary of Integral Technologies, is supplying a new generation of high-voltage connectors for the $110,000 Fisker Karma electric luxury sedan. recently named “The World’s Most Interesting Vehicle,” the Fisker Karma is the world’s first premium plug-in hybrid electric vehicle.
According to industry insiders, the ElectriPlast announcement was significant because the application is a high-voltage application, which until now, required the use of heavier metal materials – and because connector applications offer unique challenges requiring tight tolerances and complex molding techniques. “The Fisker application marked an important milestone for ElectriPlast,” states Herbert Reedman, CEO of Electriplast. “We have been working sideby-side with our OEM and Tier1 clients for several years to develop this technology and it is now embodied in the exciting and new Fisker-Karma.”
ElectriPlast™, is a patented line of non-corrosive, electrically conductive resins whose properties allow it to be molded into any of the infinite shapes and sizes associated with plastics, rubbers and other polymers while reducing component weight by 40 to 60%. Applications for ElectriPlast conductive plastics include EMI shielding applications, connectors, wire, batteries and battery enclosures, cable, power electronics, antennas, capacitors, and mobile devices. Reedman, an automotive industry veteran, has been leading ElectriPlast since its inception just over a year ago. The Integral leadership team spent eight years developing their material technology and now manages the world’s leading intellectual property portfolio covering conductive resin technology and its application. “We expected that the automotive industry would be one of the greatest benefactors of this technology,” says William Robinson, Chairman and founder of Electriplast parent, Integral Technologies. “Herb’s leadership skills and knowledge of the automotive landscape made him a natural fit to lead the way forward for ElectriPlast”.
ElectriPlast was set up to function as the sales and marketing entity for Integral’s line of ElectriPlast™ resins. “This is a strategic and very positive move for Integral” states Bill Robinson, Chairman & CEO of Integral. “We are seeing accelerated growth in electrically conductive resins and we want to take full advantage of our position in this emerging marketplace.”
First conceived over 10 years ago, Electriplast found its root in the low orbital satellite industry. “We discovered the need for this technology while researching materials for next-generation antenna applications for the satellite industry,” says Robinson. “After working with materials available at the time we determined there was a performance issue with current materials and we set out to develop a material that could withstand the environment and performance criteria critical for that field. This led to eight years of research and development. Some 50 patents later the Electriplast line of resins was ready for commercialization on a broad scale.”
Currently, Electriplast offers a full line of composites comprised of more than a dozen base resins and numerous conductive-core composites. Two new additions are Electriplast PCS with a Nickel plated carbon fiber core and EP CF/66, a material comprised of PA66 nylon and nickel plated carbon fiber. “We have formulated and compounded more than one hundred recipes using our patented process. We can customize any blend for almost any customer application,” says Reedman.
Electriplast’s Flexible Content Technology – or FCT – is a patented process of manufacturing plastic pellets which allows for a flexible “shift” in the ratio of conductive fiber to base resin. “In the case of high-voltage applications such as the connector for Fisker, the resistivity of our materials must meet more stringent performance conductive-core fibers and dialing down the percentage of resin,” states Reedman, “or in the opposite extreme, shielding requirements for low voltage applications require a lesser degree of core materials which we replace with the lesser expensive resin base material which helps to contain costs.” The constant focus on reducing weight is leading to technology convergence with both the space and aviation industries.
ElectriPlast has signed a collaborative agreement with Volta Volare’, an aircraft maker whose recent launch of the world’s first full performance, hybrid-electric GT4 aircraft referred to some in the media as “A Fisker with wings” represents a milestone in aviation. “We will be working with Volta Volare to develop weight saving technologies for use in future GT4 aircraft as well as solutions which can be applied in the field of general aviation,” said Reedman. “We are also in discussions with a European aircraft maker on lightweighting initiatives and hopefully we can provide solutions which will impact the industry in a big way.”
“Conductive resins is still a very young industry,” states Robinson. “For many, even those who were in the space, there was no clear understanding of how to implement applications or design components with this material. It is not just the weight advantage that comes with Electriplast, it is the design freedom and system cost saving that can be gained with full implementation of the technology. Many of these companies, made up mostly of large conglomerates, are still learning the full scale of the technology.”
Working through their Tier1 and OEM relationships ElectriPlast’s technical team provides engineering support from concept to design, prototype to testing and through final implementation. Led by a renowned and experienced Detroit engineer, Mo Zeidan, former CTO for a leading global automotive Tier1 supplier, ElectriPlast’s technical team is “focused on producing the highest quality, highest performing materials on the market and we understand how to engineer, design and implement the strategy,” says Reedman.
More Stories
Sensor Fusion and the Next Generation of Autonomous Driving Systems
Unique Experiences in Miami: What to Do Off the Beaten Path
The Factors That Impact the Outcome of a Car Accident Claim