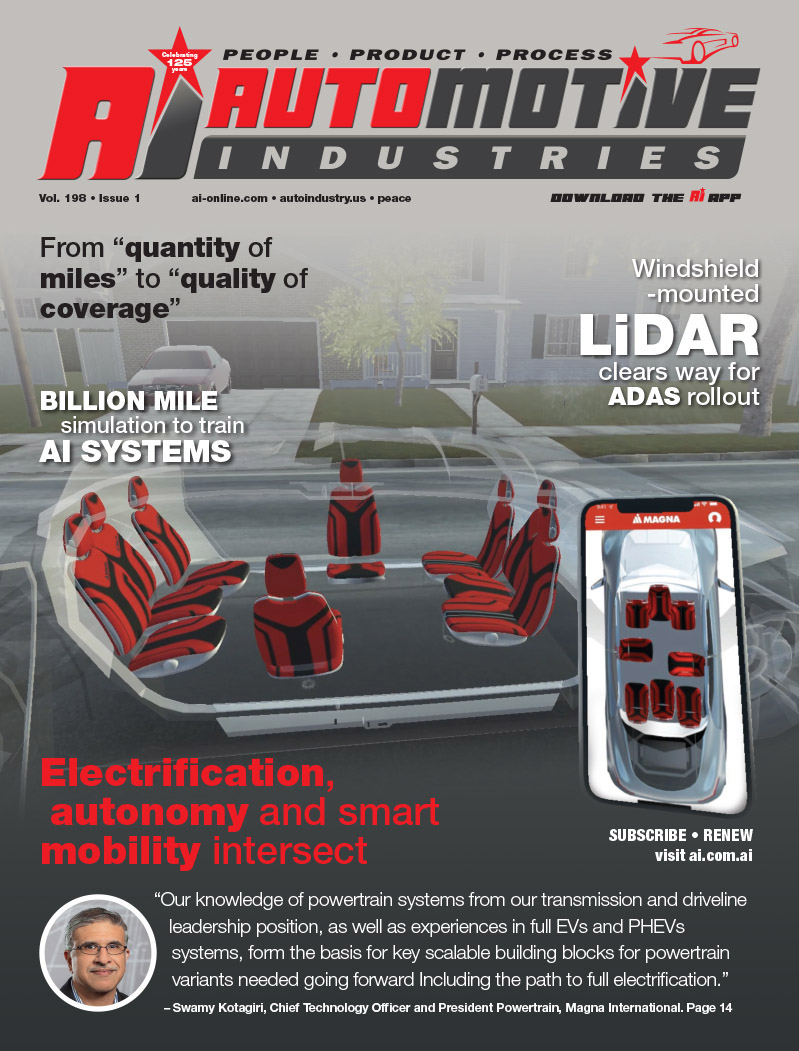
Tier1 suppliers are helping OEMs reduce emissions and im¬prove consumption through investing millions to develop and refine engine and drive-train technology.
One of the leaders is the Schaeffler Group. Automotive Industries (AI) asked Wolfgang Dangel, Schaeffler’s Member of the Executive Board Automotive, what impact the company’s award-winning UniAir technology is having on vehicle design.
Dangel: The UniAir system facilitates the opening and closing of engine valves several times during one camshaft revolution for the first time in mass production. The UniAir technology is a cam-actuated, electro-hydraulic valve train system that can be used in gasoline and diesel engines. With this system, a valvetrain component displaces oil in a gallery that pushes against the engine valve causing it to open.
The timing of the oil pressure required to open the engine valve is managed by a fast-switching solenoid valve. By controlling this oil pressure, the solenoid valve controls the shape of the valve lift curve such that early or late valve opening and/or closing is possible.
AI: How did the system contribute to the performance of the Alfa Romeo MiTo?
Dangel: Schaeffler’s UniAir system made its debut in the Alfa Romeo MiTo (Fiat calls the system MultiAir) in 2009. Combined with the downsizing options, the fully variable valve control system enables reductions in fuel consumption and CO2 emissions by up to 25%. The improvements in starting, part load and acceleration behavior are especially noteworthy. During the warm-up phase, for instance, hydrocarbon emissions (HC) are reduced by 40%, while nitrogen oxide emissions (NOx) decrease by up to 60%.
AI: How does Schaeffler work with automotive manufacturers?
Dangel: Recently we not only got the 2012 Automotive News PACE Award for our UniAir fully variable valve lift system, but we addi¬tionally received – together with Fiat Powertrain and the Chrysler Group – an Innovation Partnership Award in recognition of our col¬laboration in the development of the system. This award recognizes automakers that do an exceptional job of collaborating with a supplier to develop an innova¬tion in an effective way. Close relationships with our customers and collaborative development works are hallmarks of Schaeffler. Our 180 loca¬tions around the world ensure that we are pre¬cisely where our customers need us – nearby. From the moment the initial concept begins to take shape, we are already assisting our custom¬ers with state-of-the-art engineering techniques and our expertise in manufacturing technology.
AI: Tell us about Schaeffler’s innovations in engine technologies – how has your company worked on improving emission solutions?
Dangel: We are convinced that the majority of all automobiles in the future will still have internal combustion engines, serving either as the single or primary drive source, or as a range extender. These internal combustion engine drive trains still have a great deal of room for improvement in terms of fuel consumption and CO2 emissions – up to 30% in practice. When considering these improvements in detail, this potential can be achieved by optimizing the thermodynamics, minimizing pump losses and frictional resistance, using ancillary equipment controlled according to requirements, targeted thermal management, downspeeding, downsizing, and the start-stop function. The micro hybrid, that is the start-stop function, will feature in automobiles across the board in a very short time. Start-stop systems place special requirements on different components, and Schaeffler offers a wide range of customized solutions to fulfill each of these.
AI: What is your company’s strategy in electric and hybrid engines?
Dangel: The complex issue of electric mobility is attracting ever-growing interest. Our product range already includes numerous solutions relating to electric mobility, ranging from sensor bottom brackets for pedelecs (electric bicycles) through start-stop solutions and hybrid clutches right up to electric drives. We set up our eMobility Systems division in 2011 to be able to focus our activities around alternative drives more effectively. In this facility, we are bringing together the expertise in electric mobility from all Schaeffler companies around the world. Several hundred engineers are collaborating here in interdisciplinary networks to develop new systems and units, and these activities are by no means limited to mobility on four wheels.
The eMobility Systems division considers itself an open concept rather than a self-contained unit: collaboration with partners from industry and universities is not only welcomed, but considered necessary. It cuts development times and helps obtain feedback from future users of the innovations being developed as the research progresses. By working with universities, we hope to attract highly talented graduates to our company.
The eMobility Systems division is pioneering technology. For example, an electric axle with torque distribution between the right and left wheels will go into mass production in a few years. In addition, a hybrid module which generates considerable increases in performance by incorporating an electric module is ready for mass production now.
AI: How important is the aftermarket to Schaeffler?
Dangel: Schaeffler Automotive Aftermarket is a major player in the international aftermarket business. More than 15% of worldwide automotive revenues in Schaeffler were generated through our aftermarket activities in 2011. We have acquired our strong position in the aftermarket not only because of our excellent products, but also through customer proximity, market and workshop expertise as well as through a holistic marketing approach – selling not only “products” but repair solutions. This includes providing know-how, tools and services to our customers. In order to understand our markets and deliver to the expectations of our worldwide customer base we have set up local teams and aftermarket organizations.
AI: What are your plans to further grow your INA, LuK and FAG brands?
Dangel: Our vision “together we move the world” is our motivation to provide top performance for our customers every day. To meet this goal, we need the best people. And that is why we consider developing our employees to be the most important investment in the Schaeffler Group’s future. Besides the people, the basis of our excellent success today and in the future is the outstanding strategic position of Schaeffler. We supply tailored products and systems of the highest quality to our customers in the automotive sector and in a large number of industrial sectors. Our operating processes, which hold a leading position worldwide with respect to technology, quality and economic efficiency, are the foundation of this uncompromising focus on customer orientation.
We are developing measures to avoid errors and defects in all areas under our quality program “Fit for Quality,” and are constantly reducing our already very low error rate. We are gradually expanding our “MOVE” program from increasing efficiency in our manufacturing processes, the Schaeffler production system, to process improvements in areas ranging from supply chain management all the way to optimizing our administrative functions.
Extensive research and development turns visions into reality and is the foundation for future profitable growth. With its nearly 6,000 employees in 40 research and development centers and approximately 18,000 patents and patent applications worldwide, Schaeffler is among the most innovative companies in its industry and in Germany. We have again invested approximately 5% of our revenue on research and development in 2011. Our focus is on developing and producing high-technology and innovative components, modules and systems solutions in order to actively drive forward the fundamental trends in the automobile sector and in our many customer sectors in industry – energy efficiency, renewable energy, mechatronic systems and electric mobility.
More Stories
Towing Services Explained: 6 Key Facts You Need to Know
Environmental Factors That Influence Ceramic Coating Choices
Professional vs. DIY Tinting: What You Should Know