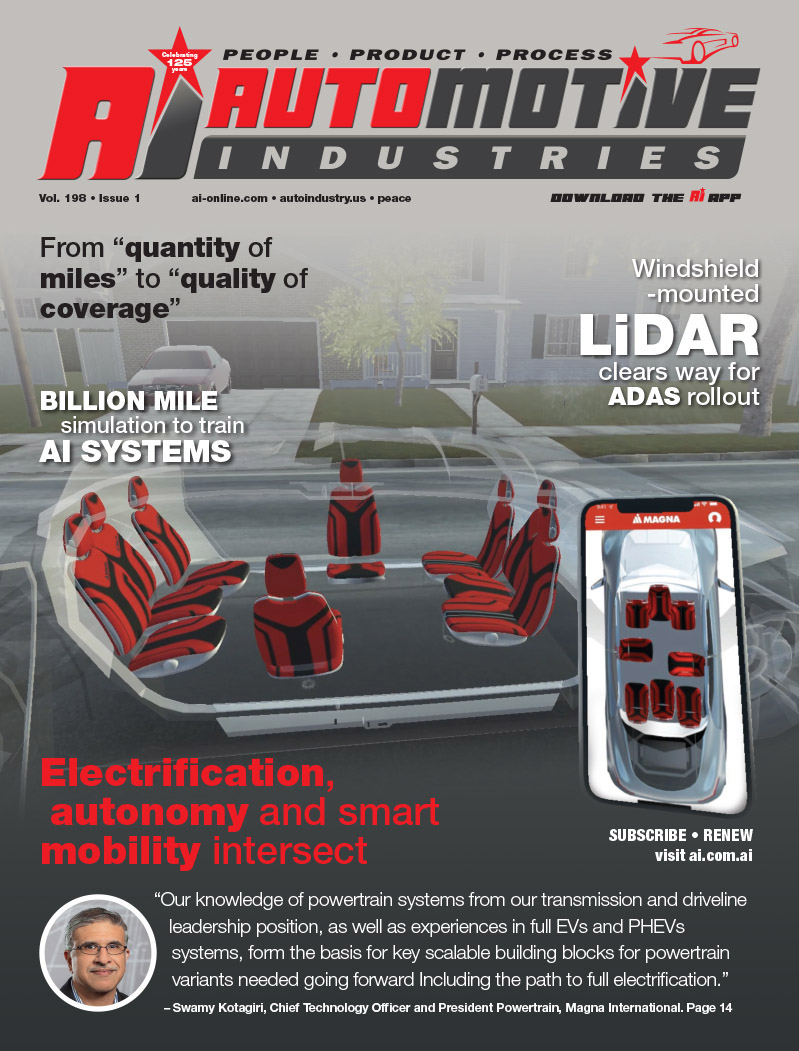
Attempts at modeling the flow of long glass fibers (10-13mm) into plastic parts has been a subject of complex research for years. Today, Michael Wyzgoski, Ph.D., will present newly achieved progress, research findings and recent “lessons learned” at the Society of Automotive Engineers (SAE) World Congress. Wyzgoski is a past GM R&D Group Leader and the former Polymers Group Manager for Delphi Research in Detroit. He is now a consultant to the plastics industry and has been conducting extensive research on behalf of the American Chemistry Council’s Plastics Division.
“Generally, the longer the fiber a material possesses, the better the part’s strength and stiffness,” said Dr. Wyzgoski. “However longer fiber materials flow very differently from all prior process models, so, a new model was needed to predict a part’s mechanical strength or stiffness. This was a major research challenge that remained unsolved for years,” Wyzgoski said. Two models are used to test plastic parts: process modeling (how materials composing the part come to rest after the injection process) and mechanical modeling (after the molding process, how a part stands up to mechanical stresses).
The ability of automotive designers to dependably predict the modulus, impact, fatigue and stiffness of various-sized long glass fiber-reinforced thermoplastics is first built upon reliably modeling 1) the fiber sizes, 2) the fiber orientations and 3) the relative fiber positioning within each part during the process of injection. “Without knowing these three crucial components, we cannot move on to create models that predict reliable mechanical performance modeling,” said Dr. Wyzgoski.
With funding from the Department of Energy, Oak Ridge and Pacific Northwest National Laboratories have validated that these three vital components can now be predicted by process models for long glass fiber reinforced plastics – an important first in plastics engineering. This allows accurate mechanical performance predictive modeling to occur for the first time in the plastics industry.
“Today, my message to engineers is this: You may not think it’s possible, but you can do this. It’s now possible to model long glass fiber parts accurately and dependably.” The confirmed calculations are now in newer versions of Moldflow® process simulation software.” Integration into commercial software is the final step needed by plastics engineers. Mechanical modeling software is already available to complete mechanical performance predictions.
“Lightweight materials with predictable strength are essential to producing more fuel efficient cars for the 21st century. Continuing research like this is helping global automotive companies utilize plastics, composites and other lightweight materials which can help meet that goal.” said Steve Russell, vice president of plastics at ACC.
“Before a part can be designed to resist mechanical “multi-axial” [multi-directional] forces and be accepted for a new application, engineers want to know that the strategic fundamental fiber microstructure and associated mechanical performance were accurately modeled, and now, they can be,” Wyzgoski said. The process models have been confirmed by Prof. Charles L Tucker III, of the University of Illinois at Urbana-Champaign, the original researcher responsible for providing Moldflow® short fiber reinforced plastics modeling software.
This collaborative plastics industry research will bypass the “make it and break it” trial-and-error testing on plastic parts that would have delayed or inhibited the adoption of long glass fiber filled plastics for years, potentially limiting plastics from these competitive arenas. Now, this research can be applied to other market sectors, such as load-bearing structural parts, sandwiched panel core construction roofs, boats, bridges, aircraft parts, composite truck trailer parts, wind turbine parts.
Over the last five years, ACC’s Plastics Division has worked in collaboration with the Department of Energy (DOE) and the U.S. National Laboratories to refine and complete wide-ranging long glass fiber research process models, vital to the successful adoption of these stronger thermoplastic long fiber combinations. This partnership has identified the importance of adopting stronger lighter weight automotive parts to reduce weight, increase energy efficiency and maintain safety.
At the Society of Automotive Engineers World Congress, Dr. Wyzgoski will further demonstrate how the latest research thrusts, including test methods for comparing mechanical properties of long fiber thermoplastics at high strain rates and fatigue of fiber filled plastics are now available and ready to be used by plastics engineers in several industries.
More Stories
6 Common Myths About Motorcycle Accident Claims
Mouser Electronics Paves the Way for Engineers with Online Automotive Resource Center
Barrett-Jackson Kicks Off 2025 with Ultimate Automotive Lifestyle Experience in Scottsdale, Surpassing More Than $198 Million in Total Auction Sales with 100% No Reserve Collector Car Docket