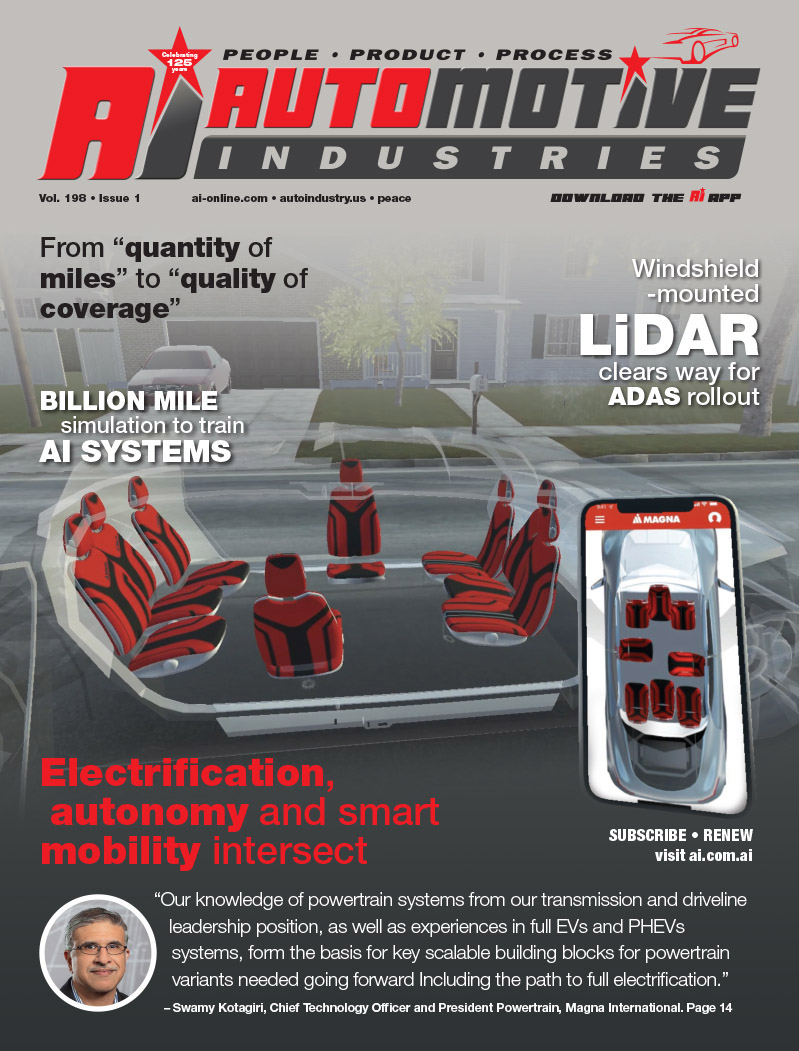
Technological breakthroughs are helping reduce under¬body weight while continuing to dampen sound, with the latest focus area for engineers and designers being the wheel arches.
One of the leaders in automotive thermoplastics is the Röchling Automotive Group, which is headquartered in Germany. It operates 20 manufacturing plants spread across four continents, with four engineering centers focusing on CO2 and noise reduction, as well as lightweight design.
Automotive Industries (AI) spoke to Erwin Doll, chief executive officer, Röchling Automotive, and asked him to tell us more about the company’s expertise in automotive plastics.
Doll: In the last five years, three of our plants received Grand Awards (the Oscars of our industry) from the Society of Plastic Engineers SPE. These awards prove that Röchling Automotive has been successful growing its customer base, improving market share and strengthening its position as a worldwide supplier by solving our customers’ main problems; emissions and weight. One of our plants in Germany recently celebrated its 100 year anniversary. We acquired this plant in 1993 from BASF Elastogran, and immediately set out to develop a number of CO2-reducing innovations which we sent out to conquer the markets. In Northern Italy, our plant has developed a long list of very affordable products for the automotive industry.
AI: What are some of your company’s major achievements in terms of automotive aerodynamics and acoustics?
Doll: Röchling Automotive developed the original shutter systems in 2003, and is still the market leader in this field. However, intelligent cooling air flow, improved thermal management and acoustics are not the only areas in which the group has achieved a leadership position. Another breakthrough was the introduction of Seeberlite, one of the first lightweight reinforced thermoplastics products. We were one of the first companies to focus on improving acoustics without adding weight.
AI: What makes your company’s Softlofting technology superior, and what are its benefits?
Doll: The idea behind Softlofting, and a similar new method which we currently preparing for market, is the identification of zones which behave perfectly acoustically, and zones which offer the best mechanical properties on a D-LFT level, and combining these into one tool and process. We are very flexible, and can optimize designs towards a minimum weight for our customers. The combination of low density while still maintaining good mechanical properties can be used for several applications in the underbody, in the engine compartment and in the interiors of a vehicle.
AI: What are some of the latest innovations in your JectBonding technology?
Doll: Jectbonding has been recognized for its unique combination of blow molding and injection molding, resulting in complex but clean and robust charge air pipes. With these advantages in the bag, the improvements mainly included increased temperature resistance at higher internal pressure.
AI: Tell us about some of your automotive OEM clients’ experiences in the usage of the Projectile Injection Technology (PIT).
Doll: When the first cooling water tubes came out of the machine, they were light and stable with a nice inner surface. Nobody could foresee that the technology would also change the concepts of cowl grilles. But, by gaining expertise, trying out different materials and shapes of components, and improving the manufacturing process, Röchling Automotive has steadily expanded its competences, while the OEMs have found out the various benefits and potentials of this fascinating technology.
AI: What are some of the technological breakthroughs at Röchling Automotive’s technologies for intake manifolds?
Doll: When we started this business, the key driver was to replace steel with plastics. While in Europe most of the intake manifolds are made with a reinforced polyamide, one can find steel solutions in other regions of the world that might be replaced in the future. On the acoustic side, two Röchling Automotive plants (in China and in Europe), have started developing two large-scale series of air intake manifolds made in polypropylene. Only a few insiders know that our intake manifolds can often be found in sports cars, where our manufacturing know-how is key to getting the pieces compact and robust. A new process called Sealbonding was recently invented to manufacture clean parts at very attractive costs, avoiding the typical vibration welding.
AI: What are some of the new technologies we can expect in 2012 from Röchling Automotive?
Doll: Recently a new kind of flexible charge-air pipe was launched in two vehicles, replacing the traditional rubber and metal pipe solutions, and offering big advantages in both weight and cost. We are also testing a number of new materials. Stratura has been developed for electric vehicles (BEVs), and offers acoustically and thermally insulating properties adding comfort to the drive. Interior floor and the rear side panels have already been exhibited in the Streetscooter vehicle at the Frankfurt Motor Show (IAA) 2011. These structural parts with a multilayer construction assume functions which were previously performed by the carpeting, the metal car body and the body undershield. Everything is now in one component.
A new type of part made with bio-polymers has also been presented to our customers. We have made big improvements in thermal resistance, chemical properties and manufacturing of parts for the engine compartment. The first parts made in Plantura are currently being tested on vehicles.
We will also continue to improve our shutter systems with several solutions for a reduced engine heat up time. We also think that interior air conditioning systems and engine air intake systems can be improved with regards to noise emissions and sound, and we are working on solutions for this
More Stories
AVL ThermalLab™ brings dynamic road VTMS conditions to the laboratory
Sika – where battery storage technology for EVs, wind and solar meet
Driving Change with Circular Aluminum: Hydro’s Role in the Automotive Future