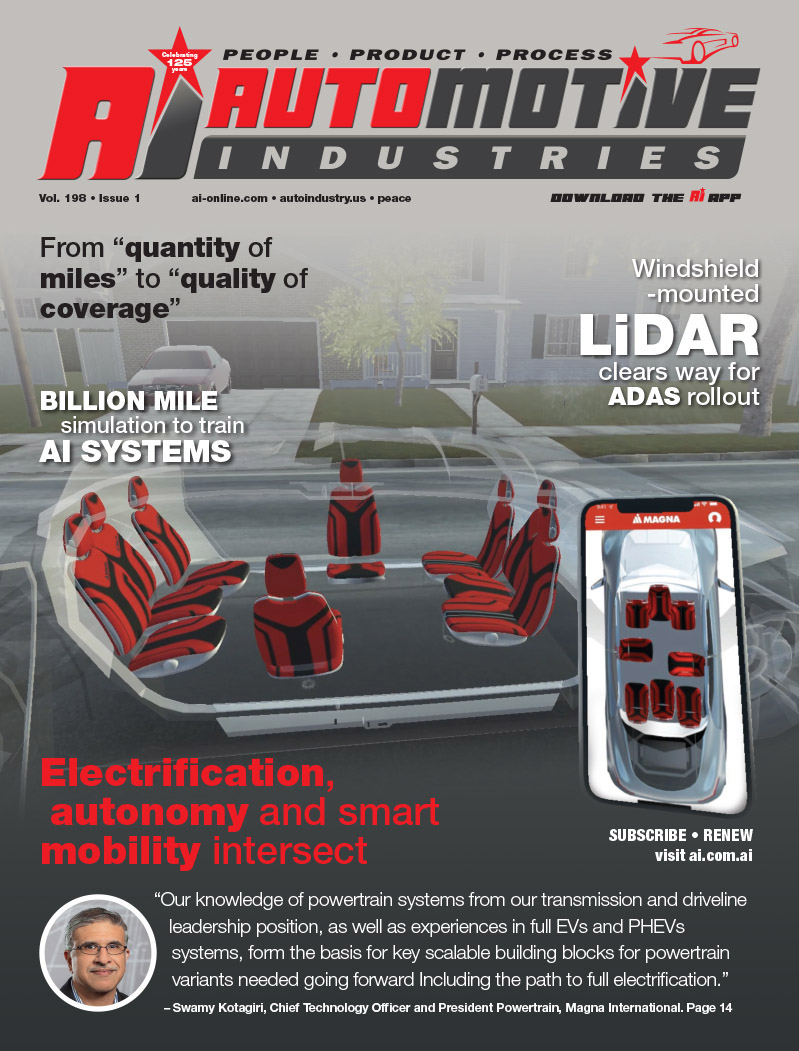
Polypropylene usage by the auto industry is projected to grow rapidly beyond the average of 70kg per passenger vehicle already used in the United States due to the drive for decreased weight, and increased fuel efficiency. In particular, C.A.F.E. standards require automakers to improve average fleet fuel efficiency by 30-40% by 2016.
Another advantage is that polypropylene is one of the most cost-efficient and earth-friendly thermoplastic resins available. It combines a low carbon footprint with excellent physical properties, low density, and good recyclability, giving manufacturers a versatile and sustainable material option. Nucleating agents have long been used in polypropylene to provide increased stiffness and more efficient processing. But, nucleating agents can also cause processing and quality problems, such as warpage or dimensional irregularities in plastic parts. Milliken, a leading supplier of additives to the plastics industry, has recently introduced its Hyperform family of “hyper-nucleating” and reinforcing agents for polyolefins. These new additives, along with continued advances in resin technology, expand the performance range and address quality issues of previous nucleating agents, making polypropylene an even better choice for manufacturers.
Milliken has been involved in research and development since 1865. It has one of the largest patent portfolios of any privately-held U.S. company. Milliken’s expertise encompasses a range of disciplines, including specialized chemistry, floor covering, and performance materials.
Automotive Industries (AI) asked Milliken CEO Joe Salley to tell us more about about Hyperform and Milliken’s other automotive industry innovations.
Salley: Polypropylene nucleation is not a new idea. In fact, the technology has existed since the poly¬mer’s invention. What is new is the focused effort to innovate within this area and to increase the number of benefits that nucleation can provide. Even though nucleation of polyethylene (PE) has been studied over the years, there was never a commercial introduc¬tion until Milliken launched Hyper¬form HPN-20E. Our nucleating agent produces breakthrough performance, enhancing nearly every aspect of PE, including optical and physical properties, processing, and barrier and seal properties. In either application, nucleation technologies fall into three categories: conventional, advanced, and hyper-nucleation. Milliken products are hyper-nucleators developed to offer high crys¬tallization rates and isotropic shrinkage, as well as com¬mon nucleation benefits such as increased stiffness and improved aesthetics.
AI: What are the benefits of Hyperform?
Salley: New technologies in the Hyperform family allow for faster crystallization rates and improved cycle times, delivering faster production times. These nucleating agents also offer superior isotropic shrinkage, leading to controlled and less warpage. The benefits of faster production and reduced warpage mean reduced energy use and better productivity for customers.
AI: How have your Hyperform products helped the automotive industry?
Salley: Hyperform products improve productivity by reducing cycle time. They also improve quality by reducing warpage, sink marks, and push pin marks. In addition, our Hyperform reinforcing agents allow for parts that are lighter, helping automakers produce cars with reduced fuel consumption and lower vehicle emissions.
AI: What are some of the future automotive applications for Hyperform?
Salley: Hyperform nucleating and reinforcing agents are now being tested and commercialized in under the hood, exterior, and interior applications. For example, interior trim parts can benefit from Hyperform in improved quality and cycle time. Automotive headlamps and air-handling components can be made lighter through stiffness enhancement and by replacing higher density fillers or reinforcing agents, such as talc. Relative to glass fiber reinforcement, our Hyperform products give a much better surface finish. Generally, the Hyperform line can provide benefits in production and material efficiencies, reduced weight, and improved surface finish in many polypropylene parts in automotive applications.
AI: What are some of Milliken’s other products that have impacted the automotive industry – for example, Tegris?
Salley: Lightweight and impact-resistant, Tegris thermoplastic composite materials help save lives and reduce injury as part of the blast protective body armor in U.S. military vehicles. They are also used as the front air splitter and right side door panels in automobiles in stock car racing. In addition, if an automotive part contains textile-reinforced rubber, Milliken likely makes it. We produce cord and fabric reinforcements for automotive tires, hoses, belts, and brake diaphragms – reinforcements that increase manufacturing efficiencies for our customers. As an example, MilliCap Cap Ply reinforces tires, while enabling manufacturers to use less rubber, improves the rolling resistance of the tire, and thereby fuel efficiency of the vehicle.
AI: Tell us about Milliken’s range of elastomeric fabric structures– what are some of the automotive applications of this fabric?
Salley: Milliken engineers a high-tenacity, patented group of elastomeric fabric structures, called Gemstone, which are designed to replace foams, springs, and numerous other cushion support components, resulting in lighter weight, quieter and thinner profile seating.
AI: Tell us a little about your Millilock automotive seating loop fabric attachment system.
Salley: The Millilock loop fabric attachment system is designed for a wide range of automotive seating applications, allowing deep and long lasting contours to exist and remain within the foam components. The Millilock system has a proven track record and years of testing and development within automotive seating industry.
AI: What are some of Milliken’s solutions for automotive interiors? Tell us about your roofing substrate solutions.
Salley: For the automotive convertible roofing market, we manufacture interior roofing substrates for cars such as the Fiat 500 and the Mini Cooper.
More Stories
DuPont materials science advances next generation of EV batteries at The Battery Show
How a Truck Driver Can Avoid Mistakes That Lead to Truck Accidents
Car Crash Types Explained: From Rear-End to Head-On Collisions