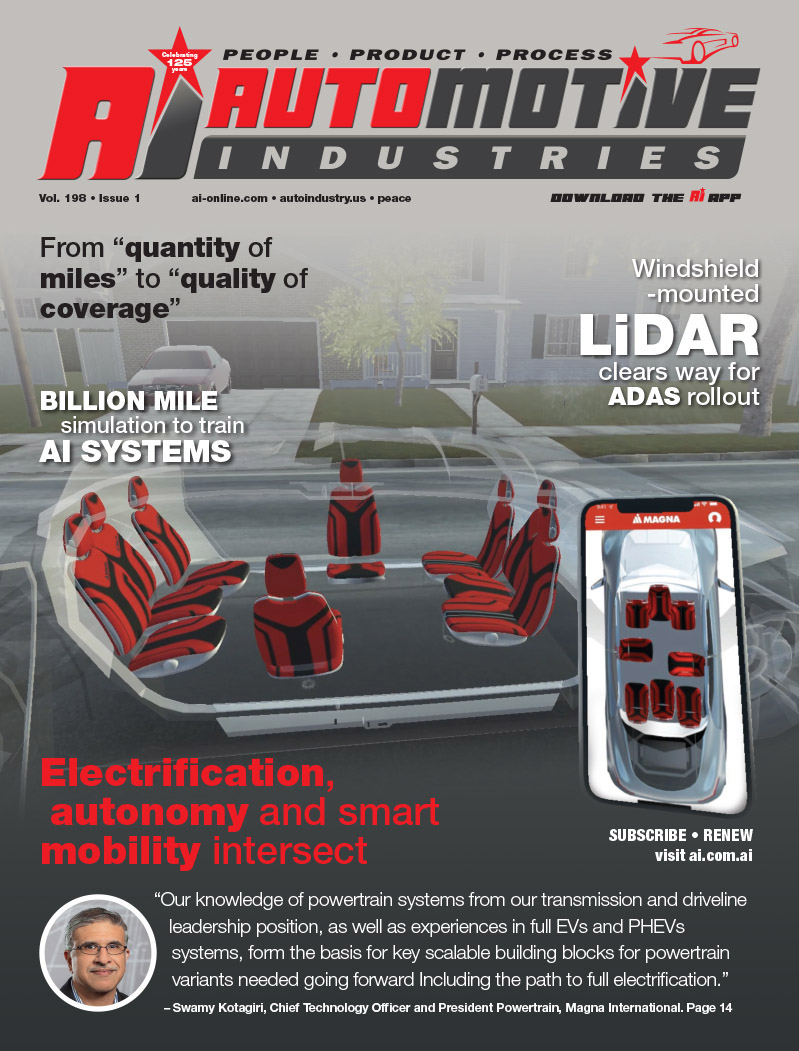
As of March 17, 2011
Further clarity has come surrounding the devastating earthquake and subsequent tsunami off the coast of northeastern Japan, although several unknowns still exist. Outside the horrific human toll/dislocation and infrastructure destruction in northeastern Japan, the growing nuclear radiation situation north of Tokyo has provided an additional brake on meaningful restoration efforts. The combination of a magnitude 9.0 earthquake and the resultant tsunami caused the loss of much of the power distribution grid, clean water/waste water services, passable roads, rail and the critical port system. The modern auto industry has never faced a natural or human calamity on the scale of today’s crisis in Japan.
Production at light-vehicle assembly plants in Japan will be restricted by several factors over the short term: (1) physical condition of supplier facilities and ability to resume produce components; (2) the availability of sufficient numbers of trained workers; (3) issues with the condition of the communication, road, rail and port infrastructure as well as the availability of various fuels; (4) the ability to secure an ample and stable power supply (without rolling brownouts) as well as other necessities such as running water and sewage/waste water treatment; (5) and most importantly, a stable supply of components/systems to ensure output of components and systems. These five critical areas of concern are the absolute minimum required for resumption of part supply from this region. There are substantive challenges over the coming weeks/months.
Condition of the Supply Base is Critical
The state of several OEM production facilities in the affected zone has been roughly established. Most have little or no damage that would inhibit the resumption of output once stable component/system supply resumes. More critical is the condition of the supply chain and its inherent ability to resume output, given the challenges we have outlined. Today’s globally interconnected automotive industry is highly competitive, having emphasized exceedingly technical and specialized components/systems, which are most efficiently produced when production capacity is flexible and well-utilized. Inventory is held as lean as possible to increase turns and bolster asset utilization. In this case, ample extra capacity to compensate for challenged Tier-1, -2, and -3 capability in the northeastern Japan region is difficult to launch quickly and quite possibly nonexistent. Many OEMs and Tier-1 suppliers are still assessing the state of production capability in the region. Communication has been an unexpected barrier.
Condition of the capability to produce integrated circuits, semi-conductors, displays, sensors and even the base material, silicon, is in question. This is possibly most important to global OEMs—the downstream effects are still being assessed. Other issues with petro-chemical feedstocks (resins, synthetic rubber, etc.) are also beginning to surface. Several electronic component facilities can resume output, although the state of the surrounding infrastructure as well as ability to transport goods and workers is still highly variable. Rolling blackouts are not conducive to efficient component output—especially in the materials and electronics sector where tolerances are slim and start-up is protracted. It is this loss of electronics production capability that will extend this supply crisis outside Japan to vehicle output by Japanese OEMs in other countries, and then other global OEMs.
Light-Vehicle Production in Japan
Toyota will idle all its facilities in Japan until March 22, with the announced loss of over 110,000 units of production (including Daihatsu). Toyota is resuming output at several component plants closer to Nagoya (south of Tokyo), although this may be short-lived. Toyota facilities on the island of Hokkaido (transmission) and Tohoku (specialized forgings/castings) in the quake zone are challenged. We now expect output to be impaired through March 23.
Nissan notes that several plants have reported damage in the wake of the earthquake, including the Iwate engine plant. The company is restarting production at select facilities late this week, although component supply is restricted and expected to reach critical levels early next week. Our expectation is that downtime will extend into mid-next week as a base case.
(Fuji Heavy) Subaru has reported that all its manufacturing facilities have been shut through March 18, primarily owing to power-conservation efforts and damage checks. Downtime is expected to be extended into mid-next week as a base case.
Honda has idled several plants today through March 20. Honda’s supply base was undermined (possibly more than others) because of the proximity of suppliers to their final assembly facilities in central Japan. Downtime is also expected to extend into next week.
Suzuki has closed all its plants in Japan through this week, after which the company will assess the situation. Our expectation is that downtime will extend into mid-next week as a base case.
Mazda has reported that although none of its facilities have been affected by the disaster, as its plants are primarily located in southern Japan, well away from the quake-affected areas, it will idle production nonetheless through the end of this week. Our expectation is that downtime will extend into mid-next week as a base case.
Mitsubishi production commenced on March 16, although component supply may begin to reach critical levels toward week’s end.
For each production workday that Japanese light-vehicle production is not functional, around 37,000 vehicles are lost. This loss would need to be compensated for once output can resume later in 2011 if required.
Impact on Vehicle Output Outside Japan
Several Japanese OEM facilities outside Japan have eliminated overtime, including Toyota (UK and US), Fuji Heavy (US) as well as Honda (Mexico), and various facilities in Europe. This is a first step in conserving components. The order of further impact will be highly variable—depending upon the state of inventory, how deep in the supply chain interruptions occur and if other sources can be procured. Production output stoppage will first start with overtime reduction/elimination, possibly altering the vehicle production mix to limit exposure to parts in short supply, a production shift cut or finally, all cessation of output until ample component supplies are procured. CKD production (completely knocked-down kits) will be of lowest priority through this crisis due to inelastic demand. While some Japan OEM facilities outside Japan have self-sustaining supply chains, linkages vary. It is expected that most facilities will be affected in some fashion within the one- to six-week timeframe.
For each production workday that Japanese OEM light-vehicle production outside of Japan is not functional, about 52,000 vehicles are lost. This loss would need to be compensated for once output can resume later in 2011 if required.
Non-Japan OEMs are not immune to the impact of a compromised supply chain in northeastern Japan. Through the Tier-2 and -3 supply chain, the majority of OEMs utilize electronic components from Japan; the race to find ample capacity for these highly specialized components (semi-conductors, displays, sensors, resistors, etc.) before inventory depletes will be very challenging. The effects will emerge in the coming weeks—several variables will influence how quickly these issues take effect and how quickly the OEMs can overcome supply disruptions. Look for most facilities to be affected by compromised supply within the three- to six-week timeframe.
For each production workday that global light-vehicle production is not functional, around 285,000 vehicles are lost. This loss would need to be compensated for once output can resume later in 2011 if required.
Outlook and Implications
The short- to medium-term loss of stable component supply will have a substantive effect on the ability for the final production facilities to quickly resume operations. Lost output in Japan may take OEMs several months to compensate for, given the state of the supply base and its ability to overbuild in the future to raise inventory. This will depend on the extent of the damage to the supply chain. IHS Automotive is continuing to evaluate the situation as it progresses, with teams inside and outside Japan examining the impact of the disaster locally and on the global automotive community. It is still very early in the process, and we expect to have a better idea of the initial impact on volumes as more information is gleaned about the extent of the damage to infrastructure in the country, the manufacturing plants, and, indeed, the communities that support the industry.
More Stories
Horse Logos In Cars – Car Brands With Equine History
Durable Engine Labels for Harsh Automotive Conditions
How Does Motorcycle Transport Work? Costs, Methods & Companies