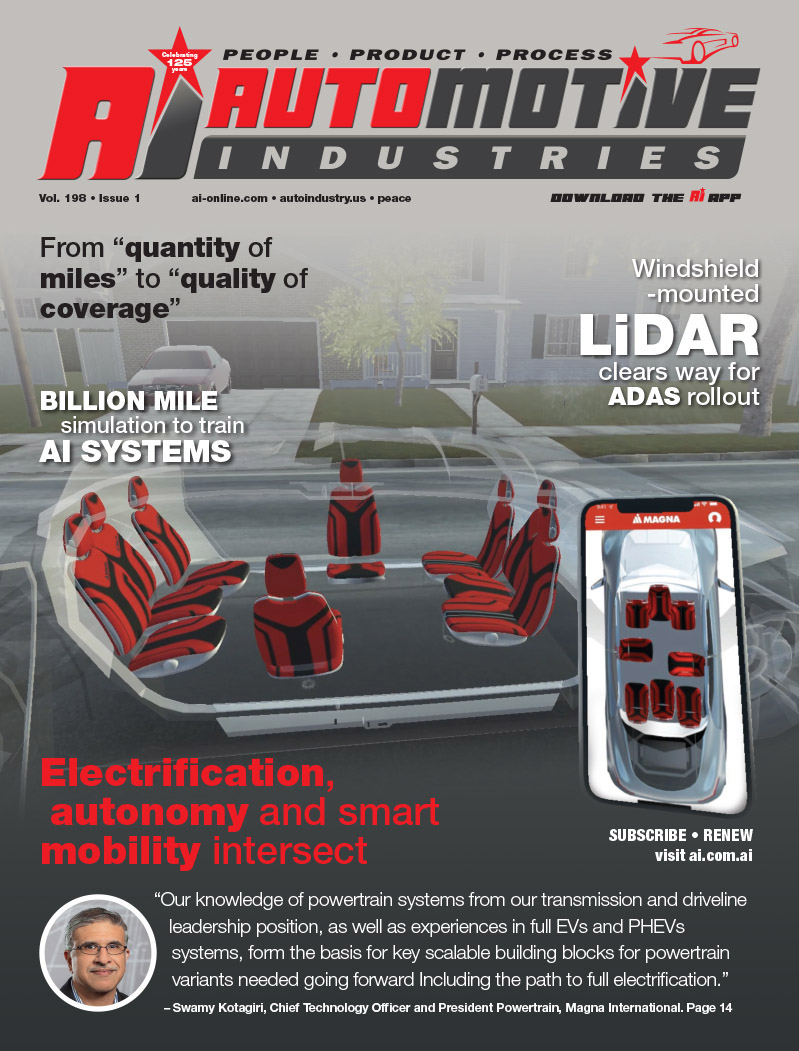
General Motors is emerging as a world leader in green vehicle technology. In the market-place, the Volt is the flagship of what is expected to be a new generation of vehicles powered by a combination of electric and hybrid technologies.
What the Volt also signals is a new culture within GM – one which sees it supporting green initiatives both in the United States and the rest of the world. One of these is the EcoCAR challenge for university engineering students across North America to re-engineer a 2009 Saturn VUE – provided by GM – to achieve improved fuel efficiency and reduce emissions while retaining the vehicle’s performance and consumer appeal. EcoCAR was established by the U.S. Department of Energy (DOE) and General Motors (GM). It is also sponsored by the Government of Canada, and the California Air Resources Board. GM Canada has entered into a five-year, $10.5-million partnership with Waterloo-based Maplesoft, and a multidisciplinary research team at the University of Waterloo to solve some of the challenges of powertrain management, control systems, battery health monitoring, thermal management, and safety in electric vehicles.
In the Far East, General Motors hosted the “Drive to 2030”: Sustainable Urban Mobility Forum series in conjunction with World Expo 2010 Shanghai. The series was created to define challenges for future urban transportation, and develop a roadmap for sustainable mobility. It brought GM engineers and designers closer to the counterparts in China, which already has the world’s largest electric vehicle fleet.
The company is looking beyond vehicle sales, and moving into the community. Chevrolet, GM’s largest brand, has announced it will invest $40 million in eight million tons of carbon offsets — equivalent of roughly a year’s worth of driving the cars it will sell in 2011. The projects it is expected to support include providing energy-efficient technology such as smart energy sensors and solar panels to schools, supporting wind farms and solar projects, and capturing methane from community landfills to deliver clean energy to the grid and improve local air quality and safety.
Automotive Industries (AI) asked Britta Gross, the director of Global Energy Systems and Infrastructure Commercialization for General Motors, whether power grids would cope with the increased demand.
Gross: There’s plenty of power available on the overall grid and electric vehicles will likely improve the overall efficiency of the grid since they will most likely be charge during the night when electricity demand is at its lowest… thereby optimizing the utilities’ use of existing equipment that otherwise sits idle during the night.
Utilities are in the business of providing reliable service of electricity into our homes and places of work and their job is to address whatever needs arise. Utilities had similar challenges in the 1970’s when home air conditioners were growing at a rapid pace and they are meeting the same challenges today with lower cost plasma TVs.
With the help of our 50+ utility partners and EPRI, we have designed a better Volt that includes some charging features that work to optimize consumer charging patterns (such as our charge by Departure Time feature). Utilities and charging installers just need to deal with the inherent variability of age of homes, age of electrical wiring in the homes, desire for 120V vs. 240V, how many other loads the house already supports, etc..
This is why we have partnered with SPX. SPX will provide one-stop shopping for our Volt customers. SPX will sell a variety of home charging stations and manage all aspects of installation for Volt owners, including the home survey, installation permitting, Department of Energy and utility coordination, and identification of available programs and incentives for reduced charging rates.
AI asked Doug Parks, Chevrolet Volt Global Vehicle Line Executive, to estimate what the demand for electric vehicles (EVs) is likely to be.
Parks: It is very difficult to speculate on the number of EVs we will see in the future and industry forecasts seem unreliable. GM plans to produce 15,000 Chevy Volts in calendar year 2011 and we’ll increase that to 45,000 in 2012. We are planning for future production scenarios and will remain flexible in the future so we can respond to market demands. The Detroit-Hamtramck plant, where the Volt is produced, is capable of further expansion if and when required. In late 2011, the Volt will be exported to Europe as a Chevrolet Volt and Opel Ampera. The Volt will also be exported to China.
Oil spill booms to be recycled for Volt
An example of how the Volt has changed the thinking and culture of the General Motors group is a decision to recycle the booms used to absorb oil from the Gulf oil spill along 100 miles of the Alabama and Louisiana coasts and recycle them into parts to be used in the new car.
Creative recycling is one extension of GM’s overall strategy to reduce its environmental impact,” said Mike Robinson, GM vice president of Environment, Energy and Safety policy. “We reuse and recycle material by-products at our 76 landfill-free facilities every day. This is a good example of using this expertise and applying it to a greater magnitude.”
GM estimates it will net about 100,000 pounds of plastic resin from recycling the booms, which it will then use to make air deflectors for the Volt’s radiator. The amount of recycled plastic from the booms will be enough to supply parts for the entire estimated first year of Volt production, according to the company.
The parts, which deflect air around the vehicle’s radiator, are comprised of 25 percent boom material and 25% recycled tires from GM’s Milford Proving Ground vehicle test facility. The remaining is a mixture of post-consumer recycled plastics and other polymers.
GM worked with several partners throughout the recovery and development processes. Heritage Environmental managed the collection of boom material along the Louisiana coast. Mobile Fluid Recovery stepped in next, using a massive high-speed drum that spun the booms until dry and eliminated all the absorbed oil and wastewater. Lucent Polymers used its process to then manipulate the material into the physical state necessary for plastic die-mold production. Tier-one supplier, GDC, used its patented Enduraprene material process to combine the resin with other plastic compounds to produce the components.
“This was purely a matter of helping out,” John Bradburn, manager of GM’s waste-reduction efforts, said in a statement. “If sent to a landfill, these materials would have taken hundreds of years to begin to break down and we didn’t want to see the spill further impact the environment. We knew we could identify a beneficial reuse of this material given our experience.
GM is dedicated to reducing its waste and pollutants, and recycles materials at every state of the product lifecycle. It uses recycled and renewable materials in its cars and trucks, which are at least 85 percent recyclable. Used tires, old plastic bottles, denim and nylon carpet are all redirected from landfills and reused in select GM vehicles.
GM facilities worldwide recycle 90 percent of the waste they generate. The automaker recently announced more than half of its worldwide facilities are now landfill-free – all manufacturing waste is recycled or used to create energy.
GM employees focus first on decreasing the amount of waste generated, and then work to recycle the unavoidable waste. In 2010, GM recycled or reused 2.5 million tons of waste materials at its plants worldwide – enough to fill 6.8 million extended-cab pickup trucks that, if parked end-to-end, would stretch around the world. Through this annual recycling rate, it is estimated that GM has eliminated 8.4 million metric tons of carbon dioxide equivalent (CO2e) emissions from entering the atmosphere.
Critical to the landfill-free designation is the ability for GM to turn material by-products from routine manufacturing operations into vehicle components. GM says plant managers view this waste as potentially useful and marketable, and they work with their teams and suppliers to develop these closed-loop systems. Other operational waste – such as packaging materials – comes full circle as well, and is often recycled into plant supplies.
More Stories
Bangkok International Motor Show 2025 – The Talk of Sensuous Automotive
Earn GHG reduction values through MOL Pure Car Carrier “Book and Claim (B&C)” service
Dry silicon composite by Blue Current is the next generation of battery technology