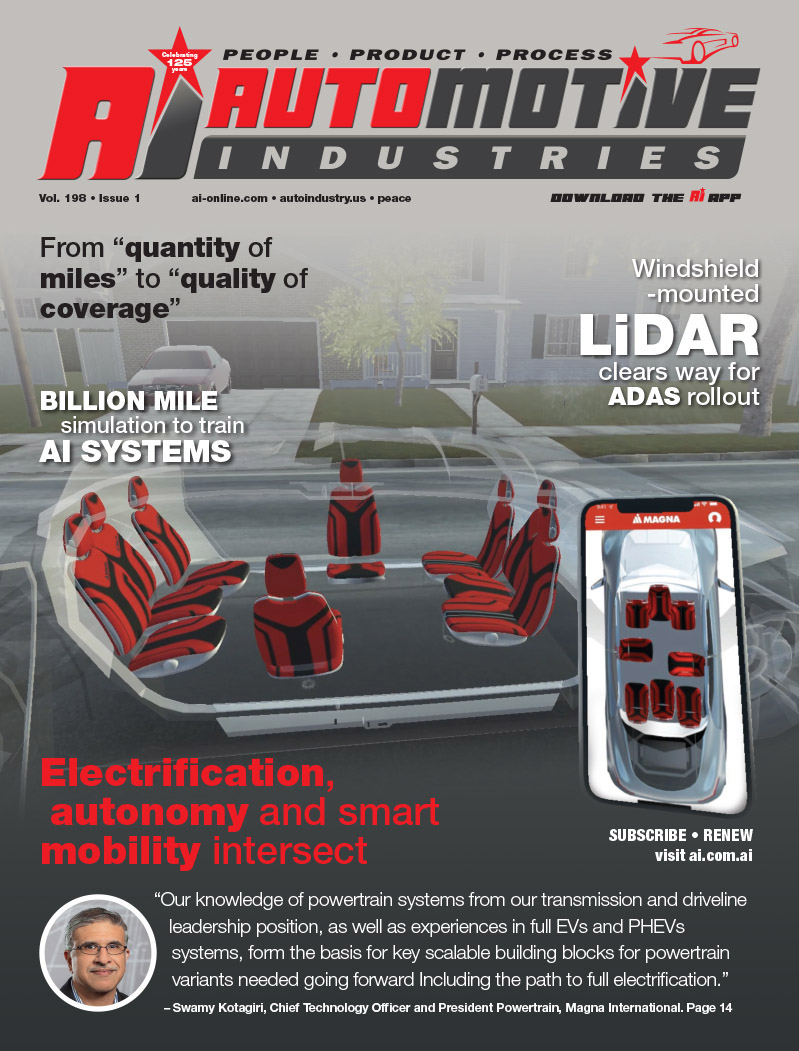
The automotive industry is highly vulnerable to time delays caused by freight and transport problems over long supply chains.
This can lead to the loss of millions of dollars if assembly lines are shut down or if products are not delivered to customers. Priority Freight is an international emergency freight solutions management specialist which helps companies manage such risks.
The family-run company was established in 1996 in Dover, England, and serves a range of time-critical industries such as automotive, aerospace, energy support and defense.
Priority Freight says manufacturers are increasingly seeking the reassurance of emergency response services based on a formalized relationship with known personnel. Should an incident occur, a solution can be instigated immediately based on a firm understanding of the manufacturer‘s own business and unique supply chain. The company’s position as a leading one-stop for emergency freight solutions was recognized when Jaguar Land Rover, part of Tata Motors, awarded a contract to Priority Freight for the provision of emergency freight solutions in early 2010. Priority Freight says it was chosen by JLR for its strengths in the areas of linguistic capability, 24-hour operation, visibility, traceability, ongoing customer support and security.
Priority Freight’s effectiveness was proven soon after the contract was signed, when British airspace was closed after the Icelandic volcano eruption. Priority Freight immediately adapted its worldwide network, utilizing areas not affected by the ash, by chartering an Ilyushin 76 aircraft. The company successfully controlled the rigors and complexities of communicating between the various parties, such as the logistics of varying quantities of products from the involved suppliers and OEMS, in a situation that was changing hour-by-hour. Despite the potential threat of shutdown for three UK manufacturing plants, Jaguar Land Rover was able to sustain its increasing sales volumes (global year-on-year sales were up by 12% in April 2010) during this challenging time.
“What we were most proud of was being able to prove to Jaguar Land Rover the real benefit of us focusing on the premium sector rather than giving all of the business to one operator,” said Neal Williams, managing director of Priority Freight.
The company has significant numbers of multi-lingual staff based in its European offices and a network of over 600 strategically located partner companies that can collect from virtually any global location on the same day, usually in under two hours.
Some of the other critical projects Priority Freight has recently undertaken include the urgent shipment of 51 tons of car parts for a production line from Canada to the United Kingdom. The goods needed to be collected and delivered within five days of request. Priority Freight provided a solution by scheduling air cargo and air charter providers, using flights with scheduled airlines to meet the delivery deadline. The company then organized road transport in Canada and the UK to and from airports and delivered the goods intact and on time. Priority Freight’s rates were significantly cheaper than the nearest competitor, according to the company.
Similarly, a major French Tier I automotive supplier asked Priority Freight to move four cartons of automotive parts from its factory in Northern France to Curitiba, Brazil. “The safest and most cost effective way to avoid a costly line stoppage at the OEM in Brazil was to arrange an on-board courier. A multi-lingual office team member with vast international travel experience, who could also deal with virtually any potential issue en-route was selected to accompany the freight. All flights and train tickets had been booked – including internal flights within Brazil, all customs procedures arranged and agents in Sao Paulo were ready to assist with connecting flights to the destination 450 km south of Sao Paolo. Loading on Friday morning, the courier personally delivered the parts to the factory the next day – and production was not affected.
Automotive Industries (AI) spoke to Andrew Austin, chief executive officer, and Neal Williams, managing director, of Priority Freight.
AI: How much of your business is automotive?
Austin: We are a significant player in the automotive market and find it to be a dynamic and challenging environment to operate in. The size of this logistics environment, plus the willingness of most of those involved in the industry to consider a range of responses to their logistical issues, means that this is the dominant market that we are involved in.
AI: What are the supply chain logistics systems involved in the auto industry, and what are your company’s automotive OEM and Tier I capabilities?
Austin: The complexity of the global automotive supply chain is such that it means that Priority Freight is involved in many aspects of logistical services, everything from scheduled routes to dedicated transport, and all modes of transport – by sea, land, or air. We also perform personalized services including specific air charters of hand-carried consignments, depending on the solutions designed. We work with all major OEMs and Tier 1 suppliers, and are intrinsically familiar with the industry, its requirements, and the various nuances of the automotive sector.
AI: What integrated logistics services and time-critical express transport services do you use for the automotive industry?
Austin: On a daily basis, we “knit” together solutions using a variety of modes in order to provide an integrated solution to the customer’s issue. This can involve collection and delivery by van; trucks of various weight capacities; air-freight or air-charter by aircraft or helicopter, and short- and deep-sea shipping routes. With an extensive network of suppliers, all major eventualities can be resolved.
AI: Are you planning to increase Priority Freight’s global footprint?
Williams: We are planning to increase our presence in a number of markets, as witnessed by the recent opening of offices in both Germany and Russia. We are particularly excited about emerging opportunities in Asia. Further locations are planned for Europe to increase our presence, and to fulfill customer demand.
AI: What are the challenges of doing business in developing countries?
Williams: There are many challenges in working in developing countries, including taut and complex supply chains due to distances involved, cultural differences, and the maturity of support operations in those locations. Additionally, experienced personnel have to be seconded to the various new locations, to supervise the establishment of indigenous manufacturing sites. Priority Freight is regularly called upon to help resolve such issues relating to the supporting supply chain.
AI: What has gone into the development of Priority Freight’s network of associates around the world?
Williams: Apart from a considerable investment in time and money, much focus has been on introducing the Priority Freight culture into the new operations, to ensure that a consistency of service to our customers is achieved, to the benefit of a long-term relationship in the various locations in which we operate.
More Stories
Automotive Industries (AI) Newsletter October 2024
Contechs appoints Christopher Hilts as US Head of Business Development
Automotive Industries Top Auto Shipping Companies, Ranked