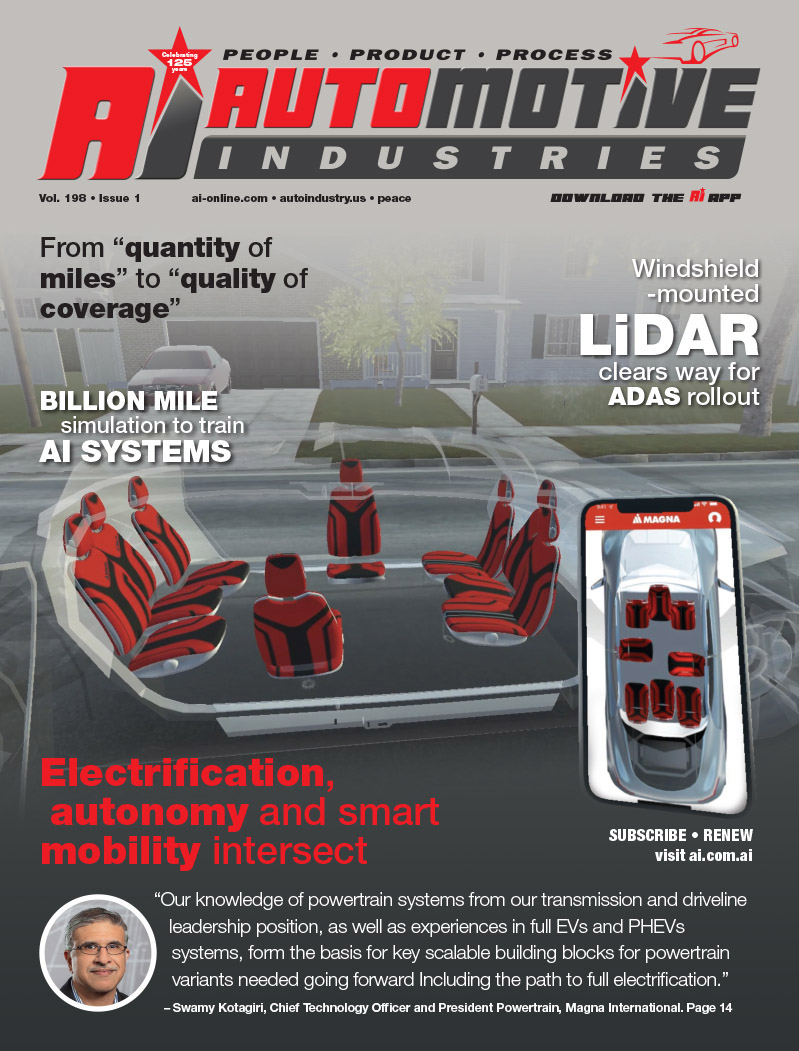
Bietigheim-Bissingen Germany, November 19, 2010 – Dürr, as general contractor, is building a new paint shop in Nanjing for Shanghai SVW. The project is a joint venture between the Volkswagen Group and the Chinese SAIC Group (Shanghai Automotive Industry Corporation). Thanks to innovative technologies, Nanjing will host one of the most environmentally friendly plants in China.
From plant technology to paint application and on to the control systems –except for the building itself, Dürr is providing a complete paint shop for SVW. Since environmental issues are also becoming increasingly important in China, SVW in Nanjing is counting on Dürr’s EcoDryScrubber – an alternative system to wet overspray separation, requiring neither fresh water nor coagulation chemicals. By using air recirculation, the innovative dry separation method reduces energy consumption by up to 60% in comparison to conventional spray booths. After installation in the Nanjing plant Dürr’s trendsetting EcoDryScrubber technology will be in use in 25 lines on four different continents.
The rotating dip-coating system Ecopaint RoDip, with which over 18 million vehicle bodies have already been painted worldwide, comes into play in the pre-treatment and cataphoretic dip-coating. Through this, the rotation of the entire car body in the tank optimizes the immersion, flooding and draining process.
Before applying the primer and top coat, the exterior of the bodies are cleaned with sword brushes by two EcoRS 60 type robots. After this, 24 EcoRP L133 type robots automatically take care of the interior and exterior painting. The opening of hoods and doors for interior painting, as well as measuring the film thickness in the top-coat, is fully automated with robots from Dürr. The EcoLCC linear color changer used in the primer minimizes paint loss considerably when changing colors.
The UBS-line is equipped with four Dürr robot stations which include a total of 14 EcoRS robots and the application technology for automatic seam sealing, underbody protection and rocker panel coating. This type of robot also completes the installations of roof reinforcement dampings in gluing stations.
The new paint shop – designed for a primerless process and the use of water-based paint – has a capacity of 31 units per hour. The possibility of subsequently increasing the capacity in order to double the output has already been planned for. Parts of the plant technology, such as the pretreatment and the cataphoretic dip-coating, are already aligned to manage 62 vehicles per hour.
This especially efficient paint shop, with its very low operating costs, will go into operation in October next year. Then both Volkswagen and Skoda mid-class vehicles will be painted there.
More Stories
Sika – where battery storage technology for EVs, wind and solar meet
Driving Change with Circular Aluminum: Hydro’s Role in the Automotive Future
Transforming automotive paint shops with BASF Coatings’ GLASS Tool: A leap towards efficiency and sustainability